Made in Japan / Monozukuri : Building on Technology and Curiosity (Part 1)
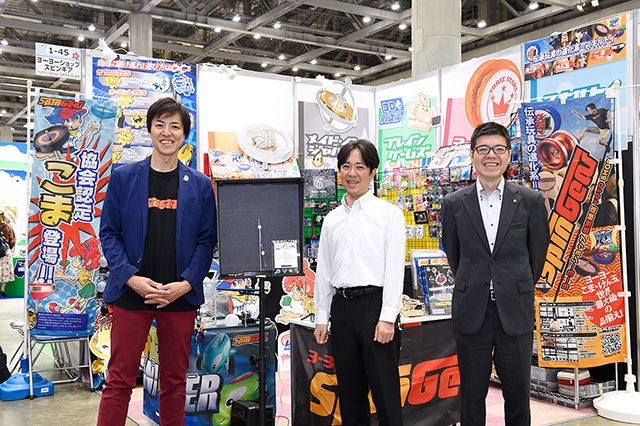
(from left) Takahiko Hasegawa, Kenichi Yamada, and Toshikazu Ishii
Creating something new isn't easy, but it's certainly an adventure. In this two-part series we talk with three leaders that came together to explore the spirit of monozukuri, and ultimately create technology-driven skill toys that have captured the hearts of children and adults alike around the world. How did they get started? What challenges did they overcome? Read on to find out.
About the team
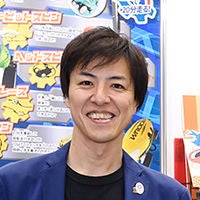
Takahiko Hasegawa
President & CEO, Soloham Co., Ltd.
Owner of SpinGear yo-yo shop
Yo-yo world champion (Over 40 division)
Takahiko has been the driving force behind re-imagining and re-creating many modern and traditional toys-spinning skill toys from around the world including fidget spinners, spinning tops, diabolos, kendama, and yo-yos. Today, the multi-time yo-yo world champion dazzles audiences with live stage performances and TV appearances alongside managing a toy shop and toy production and wholesale company.
Website: https://spingear.jp/index.php?sl=en
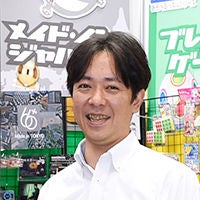
Kenichi Yamada
President & CEO
Mitsumi Factory Limited Company
Kenichi's Mitsumi Factory metalworking shop was founded in 1920 in Tokyo's Katsushika Ward. Inspired to continue the work of his grandfather, a watchmaker who made his own parts, today Kenichi and his team produce precision parts with a focus on automotive, medical, and semiconductor applications. Katsushika is known as the "town of toys," something Kenichi's grandfather took great pride in, and the family has continued to help push the envelope in bringing together leading edge precision manufacturing technology and the world of toy making.
Website: https://mitsumi-seisakusyo.co.jp/
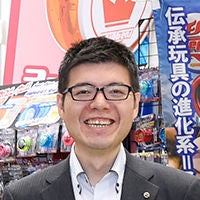
Toshikazu Ishii
President & CEO
NSK Micro Precision Co., Ltd.
Toshikazu leads NSK Micro Precision, an NSK Group company developing, producing, and selling small bearings used in electric vehicles dental equipment, computers, ships, fishing reels, and innumerable other applications. The company also employs its expertise in bearings to help develop fidget spinners, yo-yos, and spinning tops as its contribution to the "Cool Japan" initiative promoted by the Ministry of Economy, Trade and Industry.
The story so far
Toshikazu We were first brought together back in 2008, when Takahiko showed up at the NSK booth at a manufacturing expo and starting asking if we could provide high-quality bearings to use in yo-yos. To be honest, at the time I wasn't even aware bearings were used in yo-yos. We take pride in developing and producing quality bearings, and the phrase "yo-yo world champion uses NSK bearings" has a really nice ring to it, so we were motivated from the start toward the project that kicked-off our relationship.
Takahiko Typically, bearings pre-installed in yo-yos aren't up to scratch and often break during competitive play. Imagine practicing your heart out and making it into a competition only to have your yo-yo malfunction in the middle of a win-or-lose situation. It's not fun to see, and not fun to experience. This got me wondering if I could find bearings that could spin for longer without puttering out. I had no idea where to start or what kind of bearing I needed, so I tried contacting a number of bearing companies, but they all shot me down. That's when I met Toshikazu, who willingly agreed to help out, even setting up a special test bench almost immediately to get the project rolling. From there the rest is history. Over the past decade, yo-yo circles have come to adore NSK Micro's bearings with a strong reputation for high precision and reliability. Today, NSK bearings are used by most of the top competitors at the yo-yo world championship.
Kenichi For our part, Mitsumi Factory was developing its own yo-yo around the same time, and we wanted some expert opinions. We approached Takahiko with an early prototype of our work, and he immediately took it in hand and started performing with it like he had been using it for years. It really blew my mind. It was amazing how we shared in the same feeling of wanting to create something that could spark interest and "wow" the public. Since then we have closely collaborated developing yo-yos and other toys.
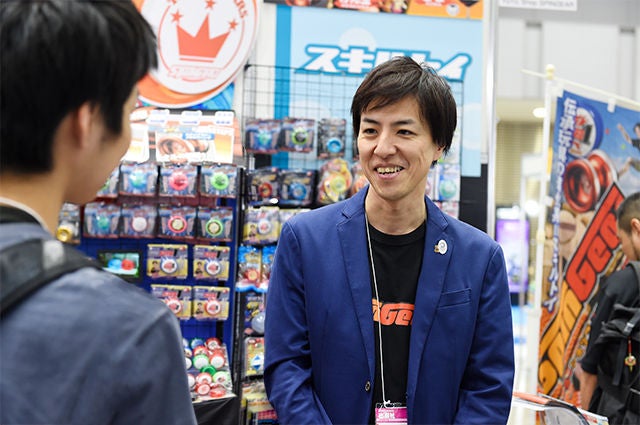
Key ideas jump from the user perspective
Toshikazu Takahiko is an absolute idea-generating machine. He doesn't just churn out ideas, his concepts are accompanied by a narrative plan-a story-that goes hand in hand with the product. It's beyond just "I want to make a really good yo-yo," he envisions how to stimulate our imagination and pioneer an evolution in toys, especially skill-based toys.
Takahiko After building up a relationship over several years, the three companies joined forces in 2017 in a closely combined effort to develop a series of fidget spinners. Each product was a big hit, garnering public attention that helped fuel the fidget spinner boom, and providing the momentum needed to expand the project. I advised the team on how internet circles were competing to see who could get the record for the longest spin. Our first prototypes could only spin for around two minutes, but despite our failures we refused to give up, and ultimately created the Saturn Spinner, capable of spinning longer than 14 minutes. We refused to compromise every step of the way as we were striving to make the best of the best.
Kenichi Takahiko really understands the product from the consumer's perspective, so we work from his ideas and refinements and build them into the product. Until joining this project, Mitsumi Factory had really only worked in a B2B capacity. It has been a real adventure to create something directly for the end user. Seeing the end user's reaction and getting feedback in person made our efforts all the more worthwhile. It gives a sense of meaning to our work.
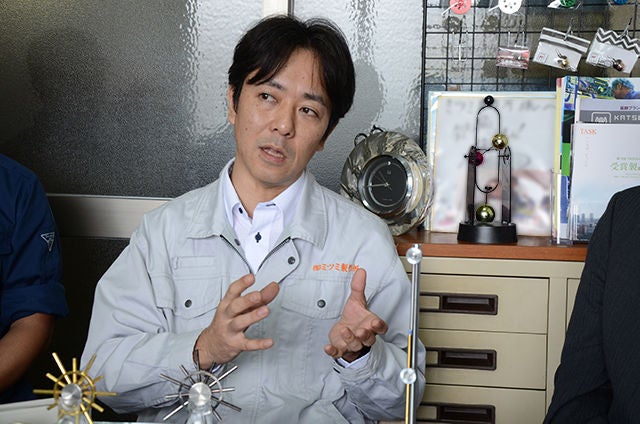
The 66% brand
Takahiko When we were developing our first yo-yo, trial and error was central to the process. We ran through our ideas, found what worked, and repeatedly refined the product. NSK Micro and Mitsumi Factory have a highly agile attitude toward product development, and abstract concepts were frequently transformed into functional prototypes. Your typical yo-yo has a diameter of 55 mm, but Mitsumi Factory pulled up its sleeves, made the most of its technology, and managed to produce a 38 mm yo-yo body that met our requirements. Combining the body with NSK Micro's precision bearing resulted in a yo-yo that is easy to use, compact, and spins super smooth-all at a never before seen level. With our newly developed product in hand, we established the yo-yo brand "66%," a lineup of mini yo-yo's with all components made in Japan. I'm exceedingly grateful for the support and companionship from both companies as we worked to create something new.
Toshikazu Yo-yos often spin at about 10,000 rotations per minute, and are swung around vertically, horizontally, and diagonally, meaning the bearing bears loads from many directions. These conditions are highly challenging, and it's common for conventional yo-yo bearings to break within a week of use. Until we took on this project we couldn't fathom how demanding yo-yo play, especially at the competitive level, could be on bearings. But we refused to give up, and redoubled our efforts to create a bearing that could last longer at high level play. We didn't stop after achieving our goal, and went on to use the technology and know-how for bearings used in other fields. All-in-all we are really happy to have pursued this project, which was beyond the scope of our typical activities.

Hear more from the team in Part 2 here.
Made in Japan / Monozukuri : Building on Technology and Curiosity
Part2 : Tokyo Gyro
Like our official Facebook page to receive updates.
[Related articles]
CHAOS MAKER: New Double Pendulum Toy with Precision Bearings