NSK Technology Solves the Longstanding Issue of Quadrant Glitches for the Machine Tools Industry
In November 2020, NSK announced an original new technology that reduces machine tool quadrant glitches in circular interpolation motion by stabilizing friction in ball screws. The clues for developing the new technology were actually found in an internal NSK technology report from the 1970s. A world-first for ball screws, the new technology creates a wide range of new possibilities. Here, the principal NSK engineers discuss how it all came about.
Profile
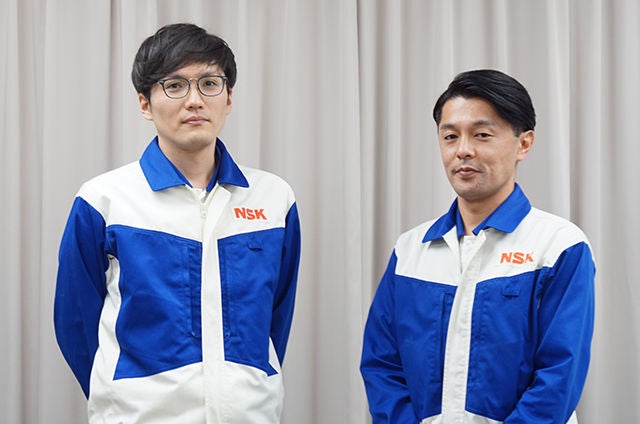
Ruito Kawai (left)
BS Technology Department
Linear Technology Center
Industrial Machinery Technology Center
Masahiro Ueda (right)
Coordinator
Research Department
Linear Technology Center
Industrial Machinery Technology Center
Role of Ball Screws in Machine Tools
Kawai A ball screw can convert rotation into linear motion. There are two major applications for ball screws. The first application is high-precision component machining, which requires extremely accurate motion. The second application is transmission of power-with a ball screw, a small rotational force can generate a much larger linear force. In machine tools used to process machine components, ball screws make high-precision component machining possible.
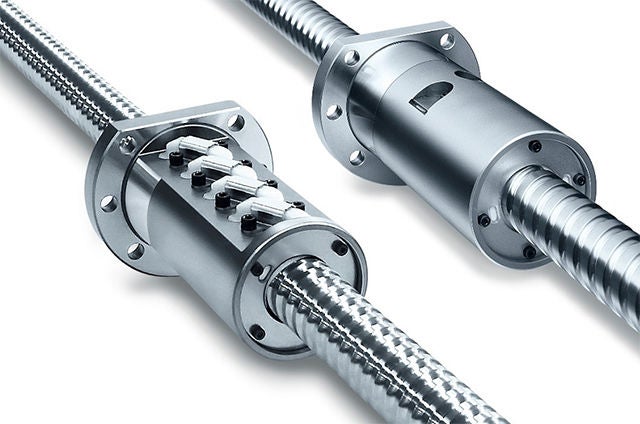
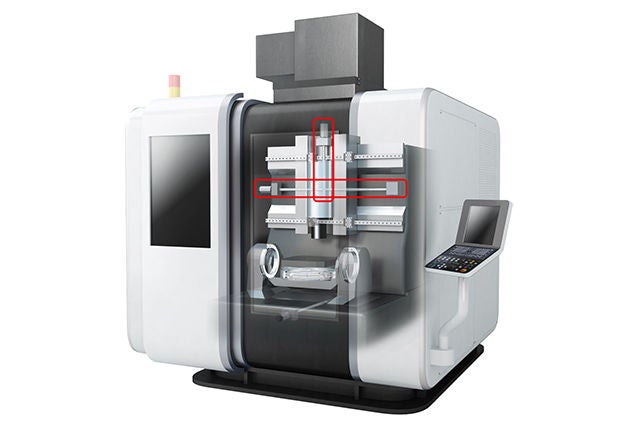
Ball screw used in machine tool (red outline)
Ueda The precision of a machine tool affects how accurately the machined shape matches the design. If precision is low, errors arise compared with the intended design. Using machine tools capable of high-precision component machining, however, ensures the finished components are closer to the ideal shape. For example, when a die is formed from a block of metal using a machine tool, the precision of the tool motion affects the finished quality of the die. NSK ball screws raise the precision of machine tool motion.
NSK’s Powerful Base of Technologies Had the Solution
Kawai One of the trends in machine tools is the effort to improve the finished quality of the machined surface. Everyday items that are made using dies and machine tools include smartphone frames and vehicle headlight components. Both feature smooth curves.
Bends and curves in dies and components are achieved using a combination of circular interpolation motions. However, during the circular interpolation motions, micron-level motion errors called "quadrant glitches" arise during reversals in the direction of ball screw motion, leaving streaks on the workpiece surface. This happens with ball screws of the type frequently used in machine tools. Until now, these streaks had to be removed in polishing process as a finishing process, and so quadrant glitches were obviously considered an issue in the machine tool industry.
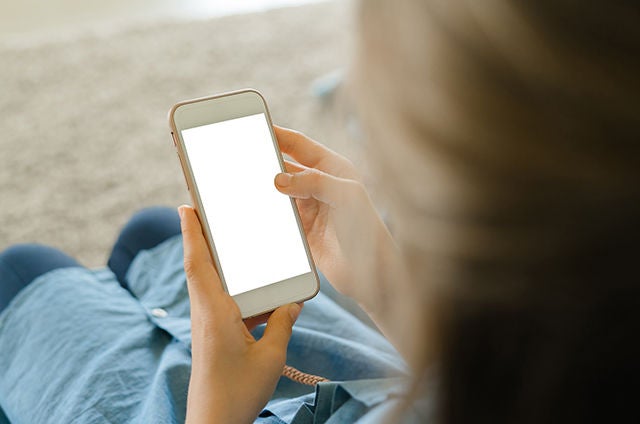
Smartphone frames are manufactured using machine tools
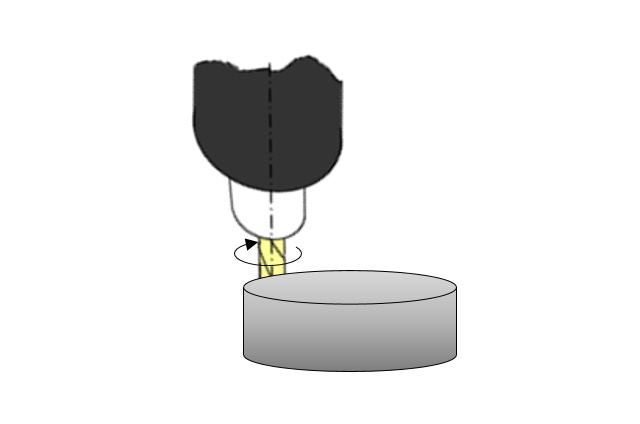
End mill circular interpolation machining
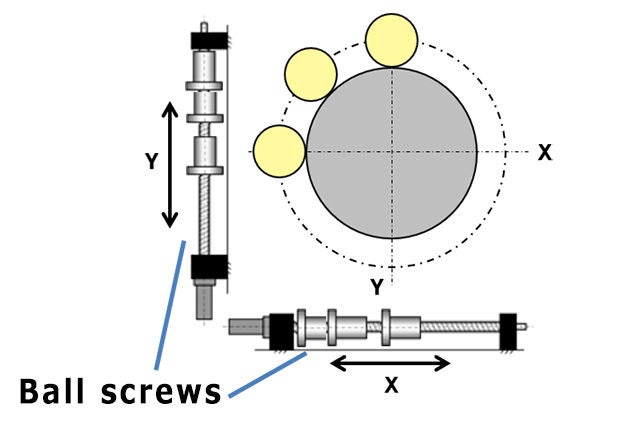
Ball screw circular interpolation feed motion (orthogonal with two axes)
Ueda We began studying ways of resolving this issue around December 2017. Quadrant glitches arise from frictional fluctuations that inherently occur in ball screws when the direction of motion is reversed. These frictional fluctuations are due to the basics of ball screw construction. For years, it was widely believed that there was no fundamental solution to this problem. Then, one day, my manager brought me an NSK internal technology report that was issued in the late 1970s. It was in this report that I found the concept that would ultimately become the driver for the new technology we recently announced. Back then, quadrant glitches in ball screws were not considered as much of an issue as they are today. So, even though the idea was good, it never made it into product development since there was little demand for it in the market. Today, however, technological advances in machine tools have created demand for higher-precision ball screws. Nearly 40 years ago, NSK had already discovered an effective technological solution to a present-day issue. I think this speaks to the strength of NSK’s technology base as a pioneer in ball screws. So, building upon NSK’s years of ball screw technology, we employed our original numerical simulation techniques, which we had invented in the process of bearing development, to find a way to reduce quadrant glitches. We significantly reduced frictional fluctuations during reversals in the direction of ball screw motion to achieve a smoother motion.
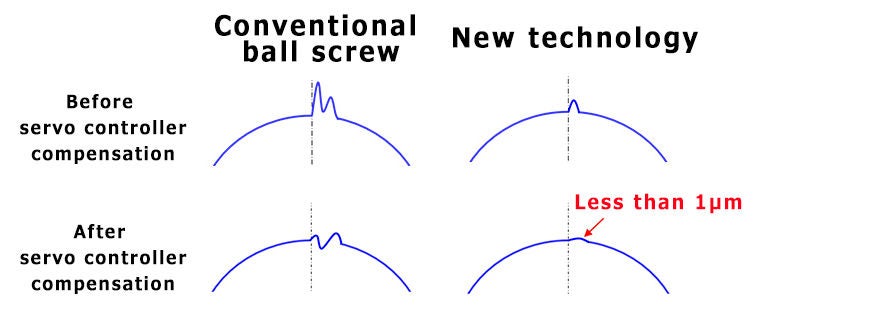
Reduction in motion errors using new technology
Kawai This technology is no mere improvement of an existing product. It is brand new. The internal specifications of the newly developed ball screws are different from that of other ball screws. Consequently, we had to reassess many factors. We steadily evaluated the quality and precision of the new ball screws, identifying the issues and resolving them one by one. The development was tricky because of the broad requirements. We had to achieve long life and suppress friction, not just reduce quadrant glitches. But we pressed on, driven by the determination to achieve a breakthrough that would surprise the world.
Until now, since quadrant glitches resulted in streaks on the surface of die-machined items, a polishing process was required to create an unblemished, smooth surface. We hope that our new technology will make it possible to eliminate the polishing process. This will reduce process times, thereby increasing our customers’ productivity and saving energy. It will also help to reduce work hours, addressing the contemporary social issue of shrinking workforces. Going forward, we will continue with development and collaborate with our production sites to integrate this technology into NSK products.
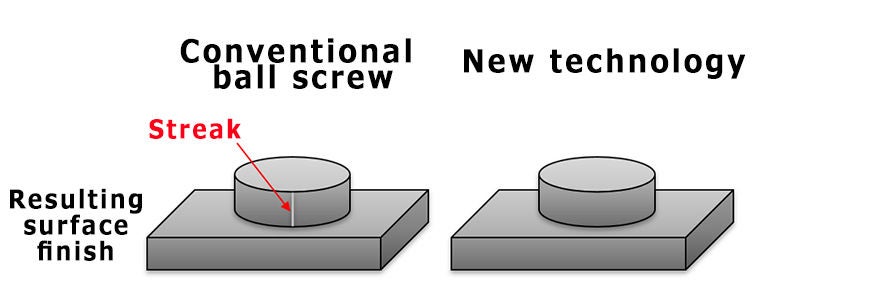
New technology improves quality of surface finish
Developing Technologies with Social Benefits
Ueda The COVID-19 pandemic has given me more time to reflect on things, for instance why I joined NSK in the first place. I have been reminded of the significance of NSK’s mission statement, “We are working across national boundaries to improve relationships between people.” I want to help foster better relationships between people through my work developing technology for ball screws. I think I can do that by improving my communication, both externally with customers and internally with other departments and production sites. I am more motivated than ever about technology development, and I will always keep in mind how NSK products like ball screws and bearings can benefit society and the global environment.
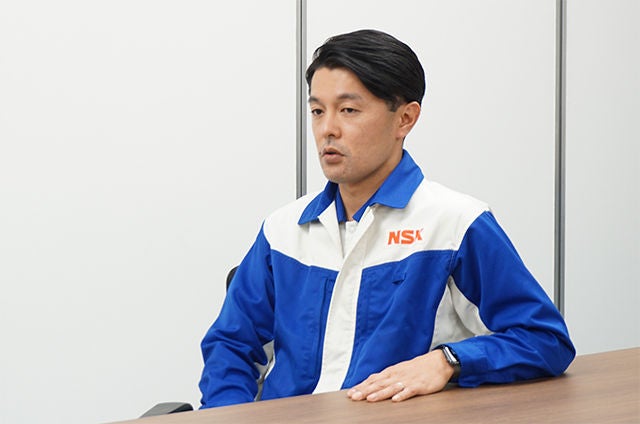
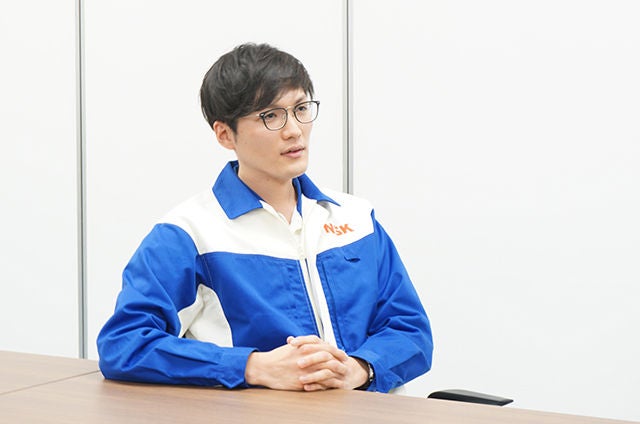
Kawai As an engineer, I feel that my duties include helping to build a safer, more prosperous world. Workforces continue to shrink worldwide, especially in Japan, where the rapidly declining birthrate and aging population present serious challenges to industry. In light of this trend, I am really challenging myself to think about how I can help the economy. I will continue to look to the future and pursue broad-ranging knowledge and information, thinking outside of the box when needed. I will also try to see my own job position objectively, from a bird’s eye view. As an engineer involved in manufacturing, I will consider what we need do to ensure that customers keep using NSK ball screws, and how we can continue to advance these technologies and applications.