Setting the Future in Motion with New Ball Screw Units for Advanced Braking Systems: Part 3 (Manufacturing)
NSK started mass-producing ball screw units for electric-hydraulic brake systems at Saitama Plant in March 2018 and at Akagi Plant (NSK Steering Systems) in January 2020. Here is the final part in our three-part series on people who created this product. We asked two NSK employees involved in the entire process, from assessing the production line to mass production at manufacturing sites, about their thoughts on this product.
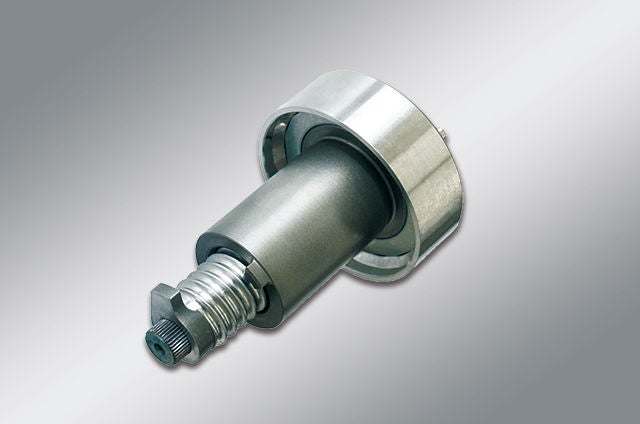
Ball screw unit for electric hydraulic brake systems
Profile
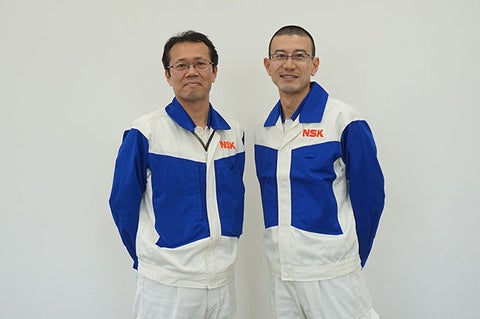
Takashi Ogihara (left)
Coordinator
Automotive Actuator Manufacturing Team
Reporting directly to the Head of Automotive Steering and Actuator Division HQ
Automotive Business Division HQ
Shouji Yokoyama (right)
Coordinator
Vehicle Dynamics Technology Development Department
Automotive Technology Development Center
Challenges in giving shape to new technology
Takashi We organized into a task force to conduct preparations for production, such as establishing production facilities to manufacture the product. While we were doing this, we also needed to deliver samples to customers. We took a trial and error approach to create a schedule leading up to the launch in parallel with production preparation, which was a new initiative for us. We worked closely with other departments and after several years we were able to start mass production in March 2018.
Shouji Our team has supported the technical aspects of the production process and quality assurance. For existing products, we are able to rearrange existing production facilities and equipment to create new production lines. However, this was a new product like nothing we have made before, so we worked from scratch with lots of trial and error. Since we had nothing to go on, there were many times I asked myself if our methods were really okay.
On the other hand, the Vehicle Dynamics Technology Development Department and the Automotive Actuator Manufacturing Team have a lot of experience producing products for new types of automobiles, which are unrelated to bearings and steering. One such product is our toroidal CVT, which NSK was the first in the world to successfully commercialize. With this culture as a base, I feel we were all able to positively take on the challenge of giving shape to a new product.
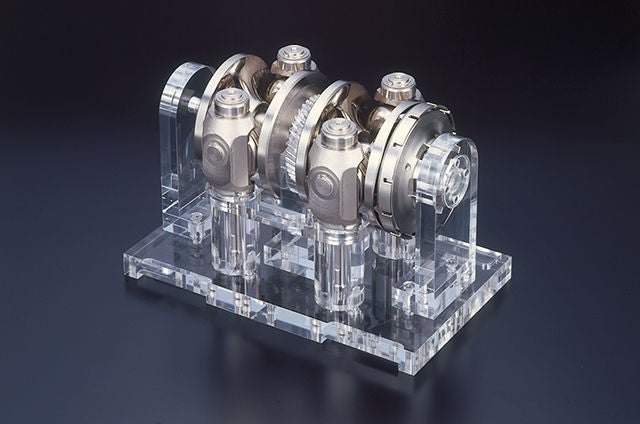
Toroidal Continuously Variable Transmission (CVT)
Our success is thanks to the technology we have worked hard cultivating and strong communication
Takashi The key to this product was the development of new manufacturing methods. To this end, NSK's knowledge of bearing and ball screw technology and production cultivated up until now was essential. For example, in terms of bearing technology, as products are required to be smaller and lighter, we have integrated the ball screw and support bearing. I think we were able to achieve this structure because NSK is a manufacturer that produces both bearings and ball screws, we understand how the components work together.
In terms of internal communication, I think it was also important that we had close exchanges of opinions with the department that designs products during the production line design stage. I think it was good that we had a lot of constructive discussions in each of these roles, and we were all working towards the same goal.
Shouji The "low resistance ball screw for regenerative brake system" announced back in 2011 gave us a footing for this product. The automation of the production line for the new ball screw unit was based on the process and equipment design knowledge from the launch of this product.
Many processes on the line were automated for this product. Since automation means no longer relying on work by humans and human judgment, it is imperative to have equipment in place which is reliable and makes it impossible to make mistakes. With limited time and resources, and with the cooperation of the relevant departments and production equipment manufacturers, I think that thinking and working together have allowed us to realize the mass production of this product.
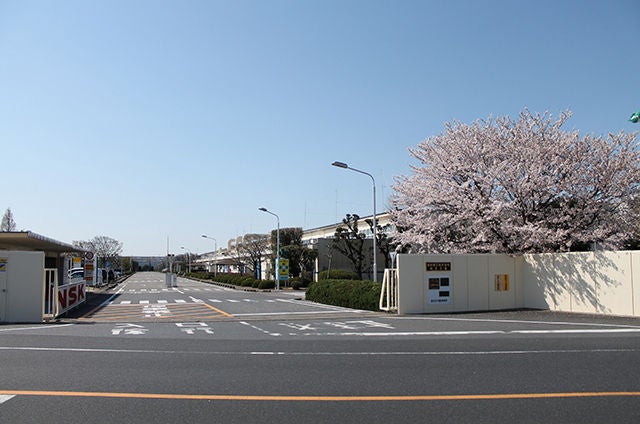
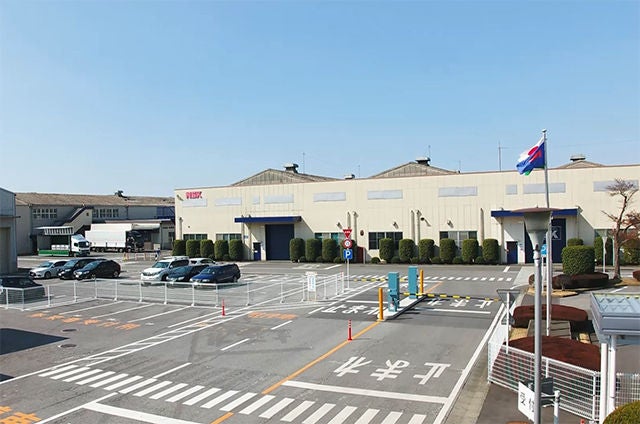
Saitama Plant (left) and Akagi Plant (right). Plants which both produce ball screws for electric-hydraulic brakes
Examples of making new ideas a reality
Takashi We have only just began, finally having a product we can deliver to customers. I believe that we cannot allow ourselves to be content with how things are and must go on making improvements in order to achieve cost competitiveness while maintaining a high quality. I feel very privileged to have had the experience of giving shape to a new product.
Looking forward, I think it is important that the organization steadily increases its ability to work on new projects whenever they may come about.
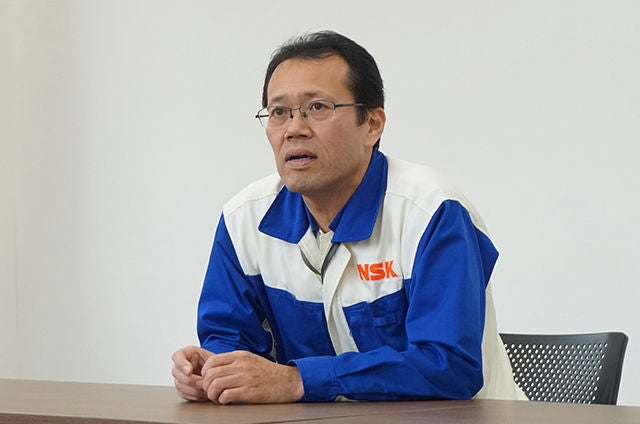
Shouji Going forward, we believe it will be essential to take on the challenge of creating new products in line with dramatic changes in the social environment, values and needs. I hope to utilize this experience of giving shape to a new product to help set the future in motion. We are also working on employee development with the aim of rolling out new products on a global scale.
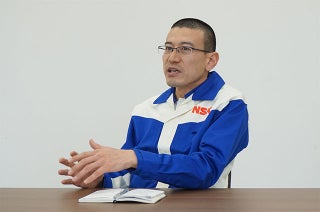
[Related article]
NSK Expands Production of Ball Screw Units for Electric-Hydraulic Brakes