Extendable Robot Arm Tackles the “Last One-Foot Problem”
Research under the supervision of MIT Professor Harry Asada
While robots in Hollywood movies often have arms that effortlessly shoot out like a snake, extending dozens of meters, in reality, we have yet to achieve anything even remotely similar. The fact that we don't have robot butlers that can care for our every need, or more importantly, robots performing dangerous jobs to reduce the risk of injury to humans, is in large part attributable to the “last one-foot problem.”
Profile
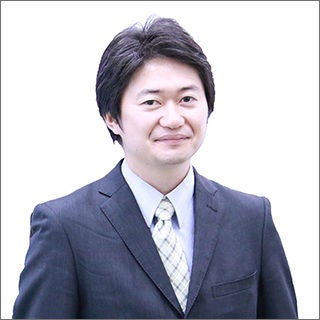
Seiichi Teshigawara
Visiting Scholar (ongoing)
MIT (Mechanical Engineering)
Research Engineer
New Field Products Development Center
Technology Development Division Headquarters NSK Ltd.
Joined NSK in 2012. Fields of interest include collaborative robots, mechatronics for health and welfare applications, and actuator mechanisms. Currently living in Boston with his wife and two-year-old daughter.
── What is the “last one-foot problem?”
In inspection, maintenance, and assembly of complex machines, systems, and products, robots are often required to reach their target through narrow, winding spaces. For example in inspection tasks, often the most challenging space to navigate is the last one foot (30 cm), reaching into tight spaces in between pipes and wires, or around the corner of a ventilation shaft. Such tasks, pose significant challenges in robot design and control, as conventional robots (using a series of servo joints or parallel linkage) are unable to effectively reach into such locations and are often too heavy to be used in mobile applications.
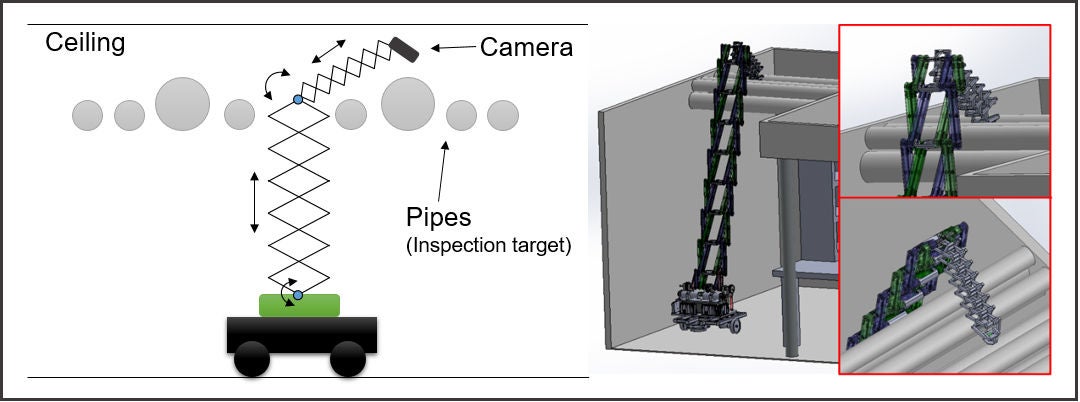
New robot design (MERA) tackling the last one-foot problem
While robots today are capable of moving around in open spaces, the last one foot to a target in a job environment can be cluttered with complex obstacles, making it difficult to complete useful work. In other words, the last one-foot problem is about the difficulty in developing mechanisms that can "finish the job," outperform the human arm and hand, and be used for a diverse range of value-adding tasks.
── How is NSK engaged with robotics and the last one-foot problem?
As a world-class company producing steering systems, direct drive motors, actuators, and other mechatronic components, NSK is actively involved in R&D in the fields of robotics and mechatronics. Previously we developed Lighbot™ to safely guide patients around hospitals, and we recently prototyped two robot arm mechanisms taking on the last one-foot problem: the Mobile Extendable Robot Arm (MERA), and an arm mechanism inspired by plant growth, the "Growing Robot Arm." I developed MERA at MIT last year, where NSK is sponsoring a variety of research and NSK employees like myself conduct research as visiting scholars.
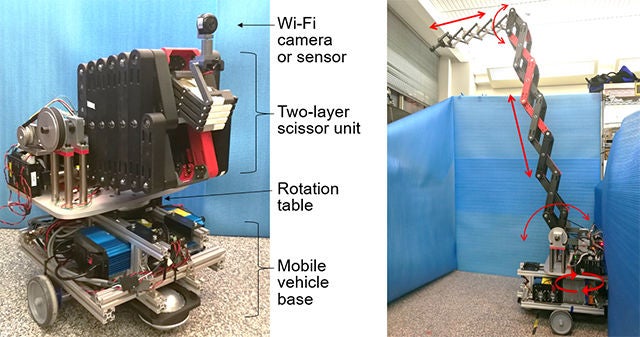
MERA (Mobile Extendable Robot Arm)
── Tell us about MERA.
MERA has a lot of potential for maintenance and inspection applications. Imagine all the pipes, wires, and controllers that our manufacturing plants and infrastructure rely upon. A lot of our plants, train tunnels, and power lines are being used beyond their expected service life, and are only getting older by the day. There is almost unlimited demand for inspection of such infrastructure and facilities, especially in more dangerous spaces.
── What kind of danger/risks can MERA help avoid?
Maintenance and repair often involves climbing up tall ladders and working around risks such as high-voltage power lines, gas pipes, and other physical and chemical hazards. Using ladders to conduct inspections comes with significant risks; falling from ladders accounts for a large portion of occupational accidents every year.
We also need to consider natural disasters and other failure scenarios that can drastically increase risk to maintenance workers such as partially collapsed or damaged roof/ceiling sections, burst pipes, gas or chemical leaks, and tangled wiring.
MERA can be used to conduct preliminary inspections with a sensor array, removing the need for a person to climb up a twelve foot ladder to a potentially dangerous situation. MERA can also perform more hands on work such as lifting ceiling panels or as an automated inspector at construction sites, taking photos of joints, wiring, or other quality-sensitive work for review by an off-site expert.
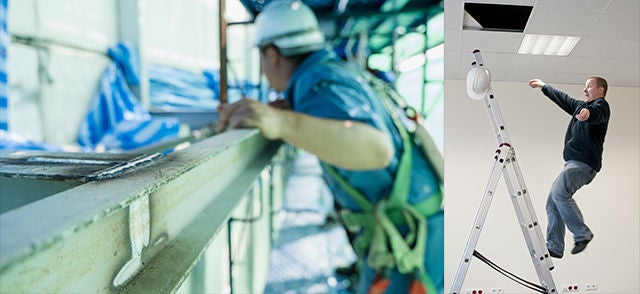
Maintenance and inspection scenarios
── What did you learn in developing MERA?
This research is part of our efforts to explore new and future applications, so unlike other projects that build on previous research, we basically started from zero, which certainly posed a challenge.
The MIT philosophy toward developing new ideas focuses on making real-world models and prototypes on a weekly schedule - "Just make it already!" So we discuss ideas, identify challenges, conceptualize a solution, 3D print a prototype, and conduct tests to see how things turn out. And again, we do this all in just one week, repeating the process every week - the pace and mentality at MIT is completely different to anywhere else.
This trial-and-error focused style is extremely motivating and rewarding, because you actually get to hold your theories and models in hand on a weekly basis. This really drives home that feeling of success or progress and makes it easier to identify new or remaining issues. I think many companies could learn to apply faster, leaner development cycles by following a similar style.
── What has been the initial response to MERA?
After exhibiting MERA at ATX East in New York, we received a number of inquiries from maintenance companies, which are a perfect fit for MERA's capabilities. What came as a surprise for us is that some companies want to use MERA to inspect sewers and narrow tunnels. Popping off the manhole cover and letting MERA extend down into the hole is definitely possible, but it was interesting because we were mostly thinking of using MERA to reach up to high places.
── What comes next?
Many companies are doing similar exploratory research and future oriented projects, but these are often one-off short term endeavors. The big question still remains as to how we take our research efforts to the next level and jump start the journey to commercialization.
The research done on MERA will certainly be expanded upon in academic circles, but we want to deliver a solution that makes a difference in society - like reducing workplace accidents. For this we will need to get the word out and form new partnerships with companies who are ready to set the future in motion alongside NSK.