NSK Ltd.
Corporate Communications Department
NSK Develops Compact, Lightweight Deep Groove Ball Bearing for EVs: Helping to Reduce EV Drive Unit Size, Weight, and Electricity Consumption
- NSK’s new "narrow-width combined plastic cage," when coupled with other NSK technologies, delivers significant reductions in both bearing size and weight (approximately a 10% reduction in outer diameter and a 51% reduction in weight compared to conventional products)
- New bearing is also narrower, has lower friction, and supports higher speeds
- Also compatible with various drive units, including eAxles, and hybrid vehicle drive units
Today,NSK Ltd. (NSK; Headquarters: Tokyo, Japan; President and CEO: Akitoshi Ichii) announced the development of a compact, lightweight deep groove ball bearing for electric vehicle (EV) drive units.
To further extend the driving range of electric vehicles, the deep groove ball bearings found in EV drive units need to be further optimized in terms of compactness, lightweight design, reduced width, lower friction, and high-speed performance. By integrating the newly developed narrow-width combined plastic cage with NSK's existing technologies, the company has achieved all these improvements while maintaining high levels of strength and durability. The adoption of this new bearing product is expected to improve energy efficiency by reducing the size and weight of EV drive units and reducing friction. NSK will launch this product for the EV parts market and anticipates global annual sales of 4 billion yen by 2030.
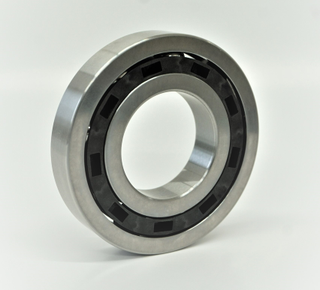
Developed Product
1. Background
Deep groove ball bearings are the most common type of rolling bearings. They are used in a wide range of applications, from industrial machinery to automobiles, and are characterized by their low friction and ability to support high-speed rotation. In EVs, these bearings are primarily installed on the shafts of drive units, such as eAxles, where they support the shaft and ensure the smooth transmission of motor-generated driving force to the tires.
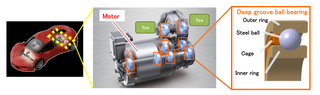
Left and center: Deep groove ball bearings used in EV drive units (eAxles)
Right: Structure of a deep groove ball bearing
As the switch to EVs accelerates, extending driving range remains a key hurdle in securing widespread adoption. To address this, EV drive units require compact, lightweight, and highly efficient designs. Consequently, the motors in these drive units are being designed for higher rotational speeds to achieve both compactness and high power output.*1 As a result, the deep groove ball bearings used in these drive units must meet demands for reduced size and weight, narrower width, lower friction, and higher speed capabilities.
*1 Motor output is equal to the product of rotational speed and torque (the force that rotates the motor). This, in turn, is proportional to the product of rotational speed and the square of the diameter of the motor's rotating part. Therefore, to reduce the diameter of the motor's rotating part without decreasing output, higher rotational speeds are required.
Narrower width means reducing the width of the bearing’s outer ring. Narrower bearings are expected to see high demand, especially in the market for two-shaft and coaxial eAxles, which are projected to expand in market share.
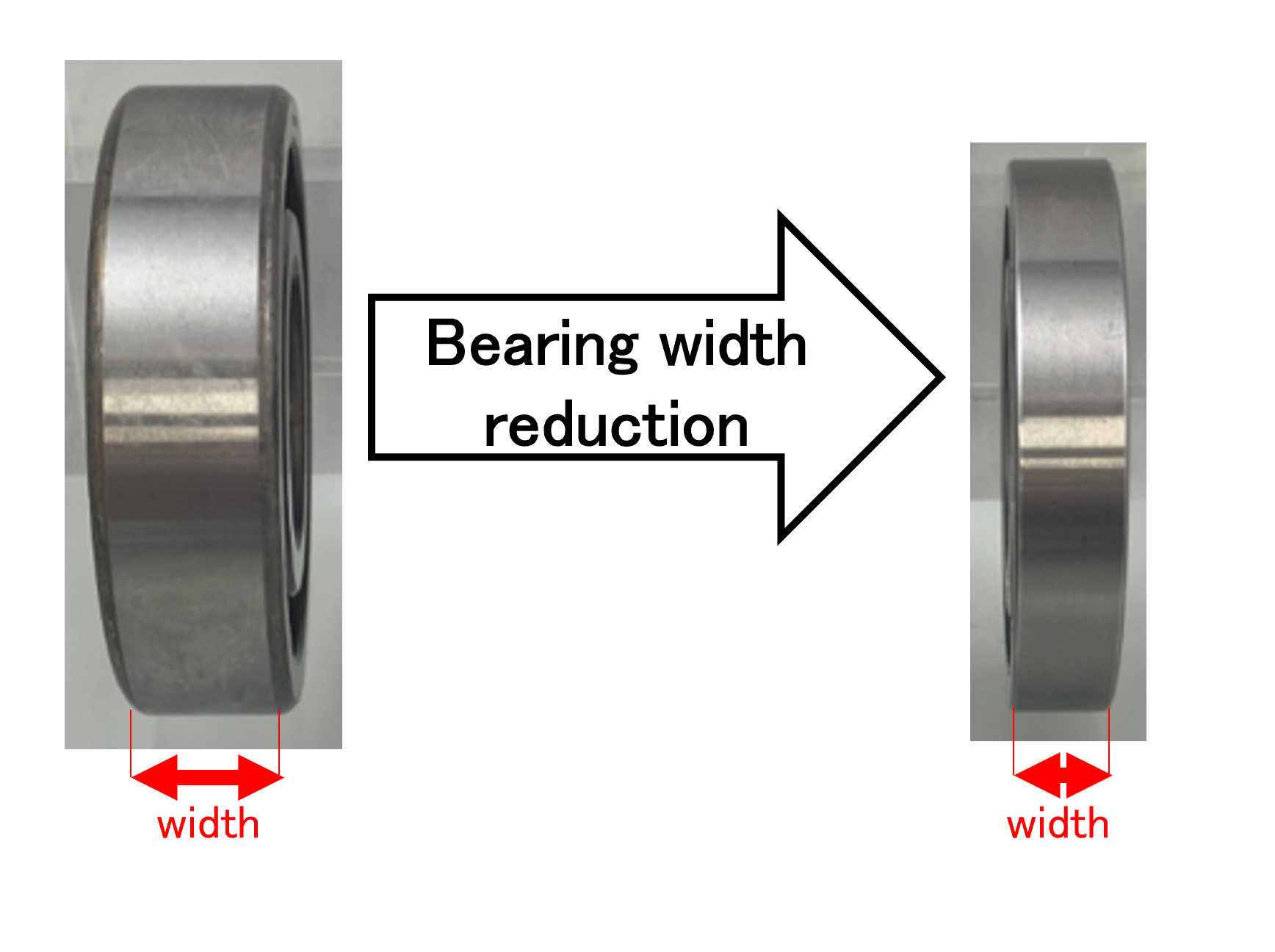
There are three major types of eAxles: parallel three-shaft eAxles, two-shaft eAxles, and coaxial eAxles. Currently, the parallel three-shaft eAxle dominates the market, with a share of over 90%. However, the market share of two-shaft and coaxial eAxles, which offer advantages for vehicle downsizing, is increasing. By 2030, their combined share is expected to exceed 20%.*2 Two-shaft and coaxial eAxles both have a structure where the input and output shafts are arranged coaxially, leading to a tendency for a longer shaft length of the eAxle unit compared to the parallel three-shaft eAxle. As a result, there is a growing demand for narrower bearings that can help shorten the eAxle unit shaft length.
*2 Market share forecast for different types of eAxles in D-segment and larger vehicles, based on NSK research as of March 2025.
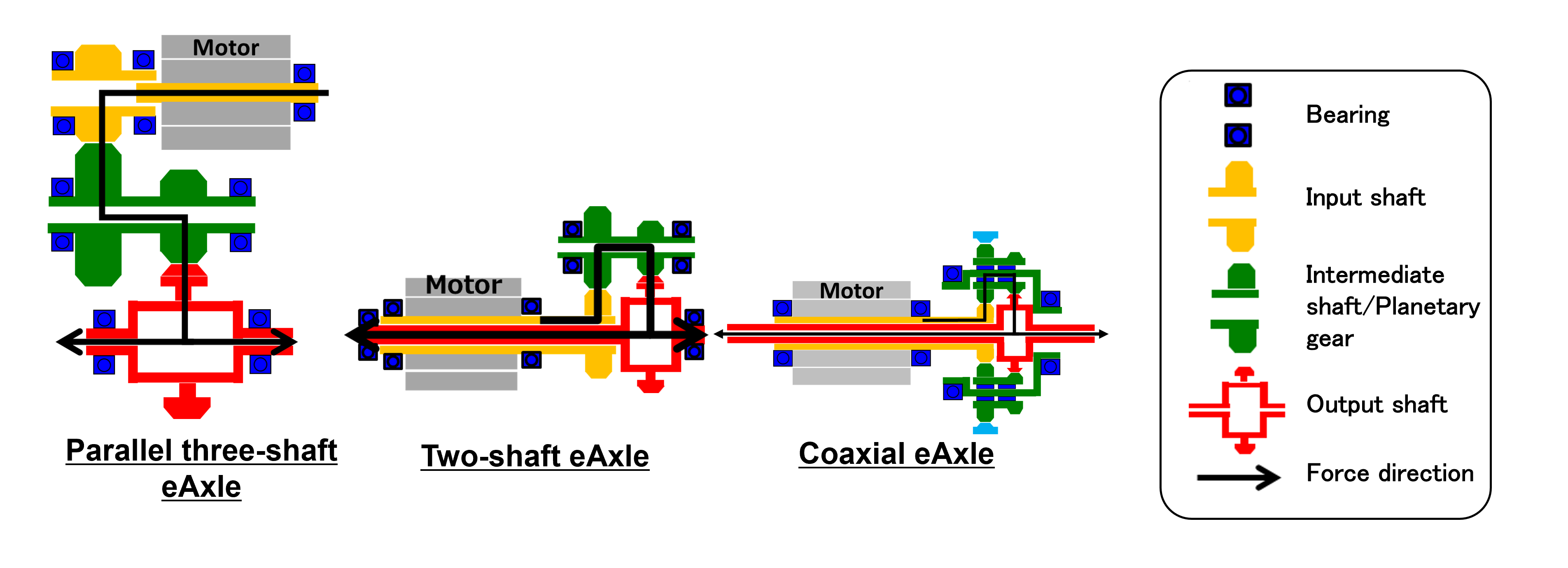
Basic Configurations of Main Types of eAxles
2. Features of the Developed Product
While maintaining high levels of strength and durability compared to conventional products, the following four key features have been achieved:
- Reduced size/weight: An approximately 10% reduction in outer diameter and a 51% reduction in weight (compared to conventional products)
- Narrower width: 38% reduction in width (compared to conventional products)
- Lower friction: 25% reduction in torque (compared to conventional products)
- Higher speed: Supports high-speed rotation with a dmn*³ value of over 2.14 million (compared to 1.8 million for conventional products)
*3 dmn: A performance index indicating a bearing's high-speed capability, calculated as the product of the bearing's mean diameter (dm) and rotational speed (n).
3. Technology of the Developed Product
1) Overview
In developing this new product, NSK applied its newly developed narrow-width combined plastic cage (NSK technology 1 in the figure below) and integrated some of its existing technologies (NSK technologies 2 to 5 in the figure below).
NSK technology 1 enabled narrower width and higher-speed performance. NSK technologies 2 and 3 solved the issue of reduction in impact load strength typically caused by size and weight reduction. NSK technologies 4 and 5 resolved the shortened bearing life associated with compact, lightweight designs. By incorporating these technologies, NSK successfully achieved a more compact and lightweight design with lower friction.
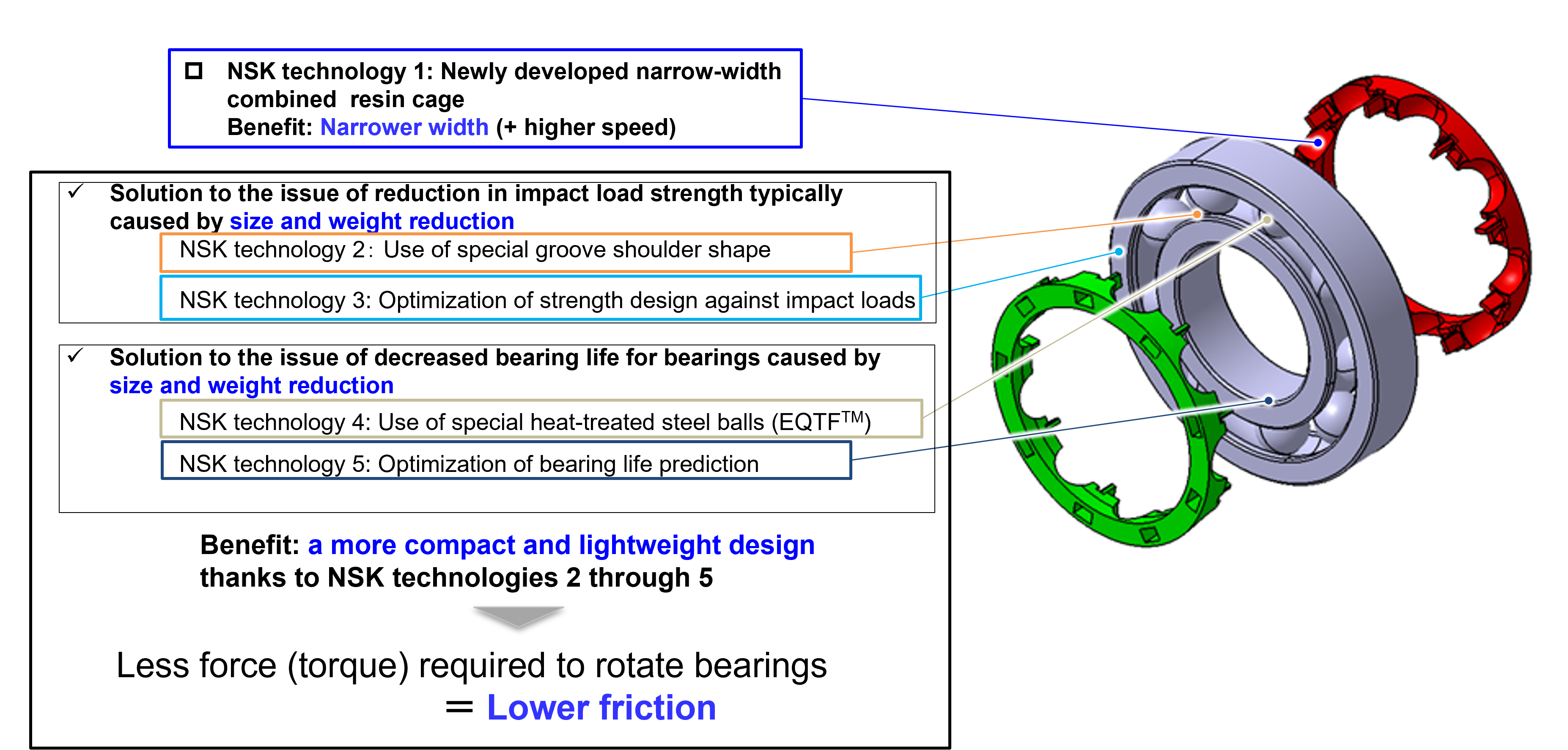
Five NSK Technologies That Contributed to Development of the New Product
2) New technology explanation
NSK technology 1: Newly developed narrow-width combined plastic cage
This new technology achieves a narrower bearing width and higher speed. Conventional cages are prone to deformation due to their one-directional assembly structure, requiring a wider design to prevent deformation.
Therefore, a new cage with improved rigidity was developed and utilized for the new product. Deformation is minimized when a pair of cages are assembled from both sides of the bearing, which allow for a narrower cage width and enables higher bearing speeds.
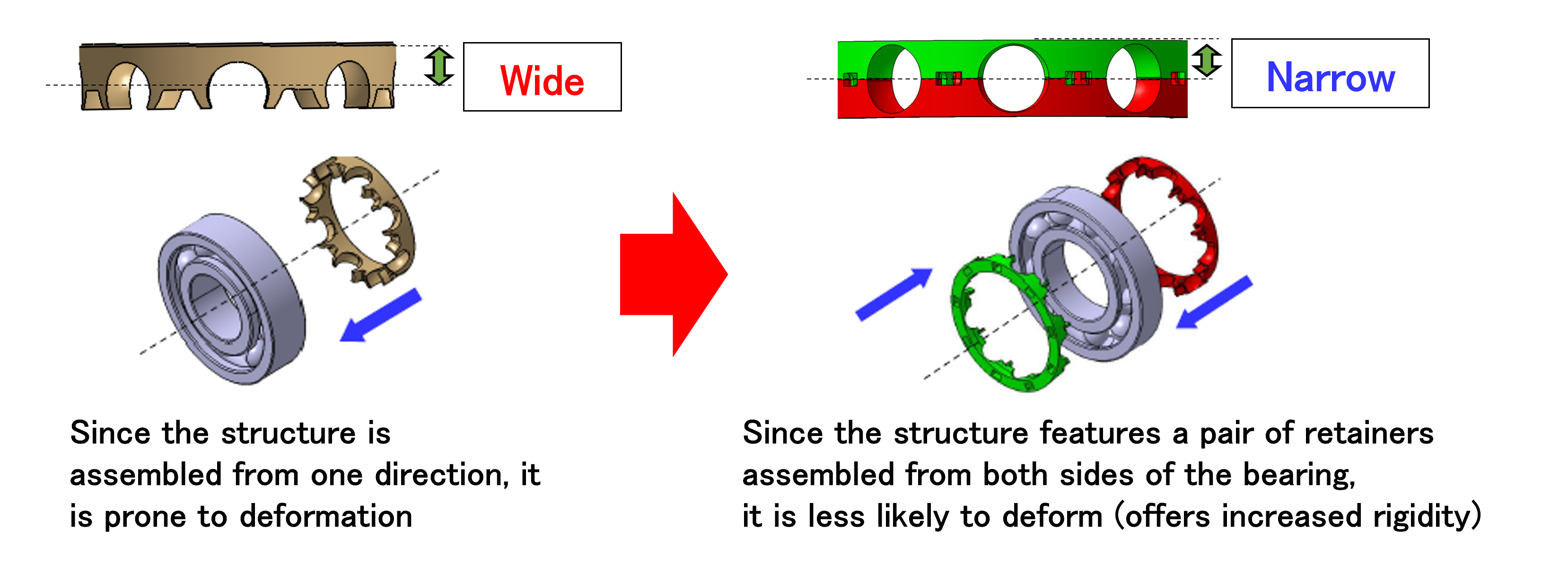
cages Appearance and Structure Comparison (left: conventional cages; right: newly developed cages)
4. Benefits of the new product
The new product can help reduce the size and weight of drive units in EVs, including shortening the shaft length, as well as decreasing electricity consumption*4 by improving bearing properties like friction reduction. It can be installed in a variety of drive units, including parallel three-shaft eAxles, two-shaft eAxles, coaxial eAxles, and drive units for hybrid vehicles.
Example: Benefits of product application in coaxial eAxles
・By adopting the new product for a motor shaft, the shaft length can be shortened by 16 mm, the weight reduced by 2.2 kg, and the electricity consumption improved by 0.09%.
⇒The improved electricity consumption allows for: (1) a reduction in battery capacity, reducing the cost of the drive battery by 960 yen,;*5 and (2) an extension of driving range*6 by 370 m.
・By adopting the new product for both the motor shaft and output shaft, the shaft length can be shortened by 32 mm, the weight reduced by 4.4 kg, and the electricity consumption improved by 0.14%.
⇒The improved electricity consumption allows: (1) a reduction in battery capacity, reducing the cost of the drive battery by 1,665 yen;*5 and (2) an extension of driving range*6 by 590 m.
*4 Electricity consumption: The amount of electricity required to travel 1 km. Equivalent to fuel economy in a gasoline vehicle
*5 Assumes a battery price of 13,500 yen/kWh
*6 Driving range: The distance that can be traveled on a single charge
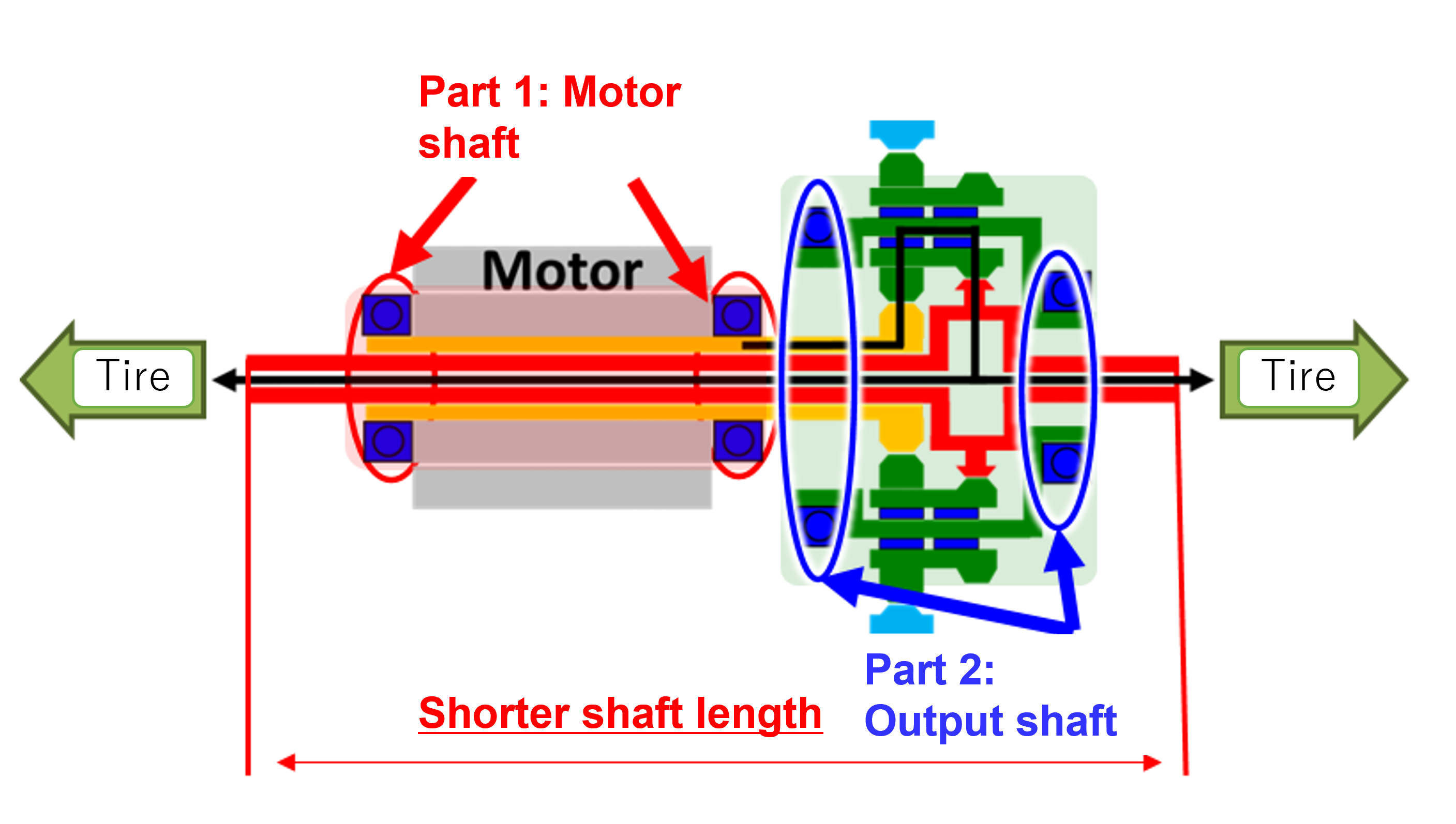
Benefits of New Product Application for Coaxial eAxles
About NSK
NSK produced the first bearings in Japan in 1916 and over the past 100 years, it has supported the development of industries worldwide by creating various innovative products and technologies in bearings, automotive parts, and precision machinery. Since the early 1960s, the company has expanded overseas and now has operations in about 30 countries. It ranks third in the world in the field of bearings and leads the world in ball screws, electric power steering, and other products.