NSK Ltd.
Corporate Communications Department
A First in the Mining Industry—Development of Reconditionable Large-Size Tapered Roller Bearings with High Load Capacity
Longer bearing life and a separable structure allows for re-use of bearings after reconditioning,
helping to reduce maintenance costs and cut CO₂ emissions
- Suited for dump trucks, crushers, and other equipment commonly used under harsh conditions
- Long life and a separable structure allow for reconditioning and cost savings
- High load capacity and up to 2x longer life realized by NSK’s exclusive Micro-UT™ method for highly accurate life prediction
- A detachable rim (inner ring small rib) allows for detailed inspections of internal components
NSK Ltd. (NSK; Headquarters: Tokyo, Japan; President and CEO: Akitoshi Ichii) has developed the mining industry's first1 large-size tapered roller bearings that can be reconditioned and put back into service.
Reconditionable bearings must offer long life and a design structure that supports long-term use over the course of repairs and equipment maintenance. These newly developed reconditionable TRBs have up to twice the life of conventional products, thanks to NSK's exclusive Micro-UT™ ultrasonic material testing method and highly accurate life prediction2.
In typical bearings, the inner ring and cage are non-separable, making it difficult to detect and address issues during inspections, but these reconditionable TRBs have a rim (small rib) that can be removed, allowing for detailed inspection of all bearing components. With fewer replacements, mining sites can benefit from bearing reconditioning with reduced maintenance costs and lower CO₂ emissions.
Plans to provide samples to mining equipment manufacturers are underway, with aims to expand offerings to cement manufacturers and other industries in targeting annual sales of 2 billion yen by 2030.
1 Per February 2025 NSK survey of tapered roller bearings for mining equipment.
2 Micro-UT provides detailed statistics on the size and quantity of non-metallic inclusions in bearing steel, facilitating highly accurate predictions of fatigue life for rolling bearings (patent pending).
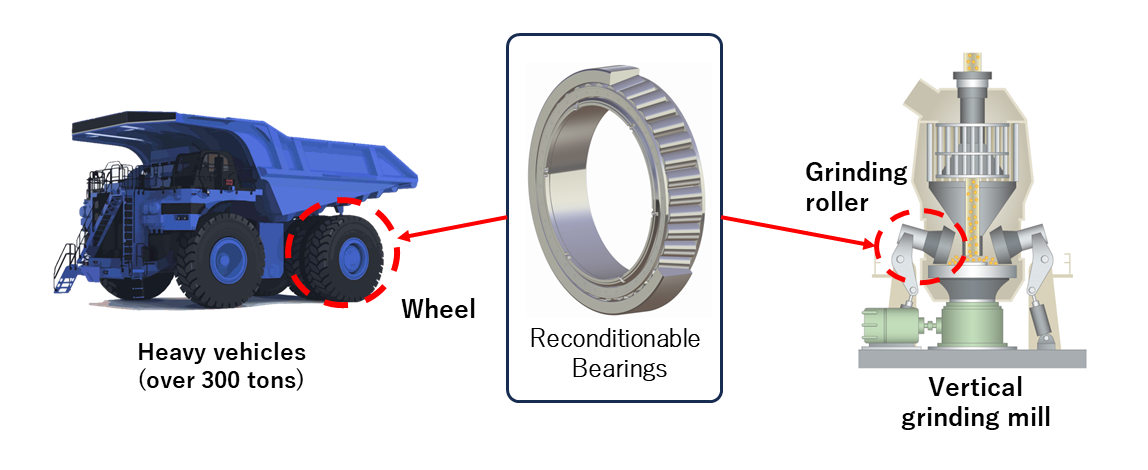
Example Mining Equipment Applications for Reconditionable Tapered Roller Bearings
(Left: Dump Truck Wheel, Right: Grinding Roller (Vertical Grinding Mill/Crusher)
Development Background
With increased urbanization and strong demand for resources such as iron ore and coal around the world, mining sites face growing pressure to take action towards carbon neutrality in energy-intensive operations. Efforts are underway to improve operating efficiency and electrify equipment, and the reuse of equipment components is a particularly important initiative to save energy and cut CO2 emissions.
Dump trucks and crushers used at mine sites operate 24 hours a day under harsh conditions with low-speed rotation, heavy loads, and strong vibration, so large tapered roller bearings are generally used for their long life and high reliability.
During equipment maintenance, components such as shafts and gears are reconditioned and put back into service; however, conventional bearings cannot be readily reconditioned, so they must be scrapped and replaced regularly. Therefore, there is a growing need for reconditionable bearings in the market.
Reconditioning requires parts to have long life and a separable structure so that maintenance tasks can be performed easily and accurately. Mining equipment can be used for decades or more, so all components must stand up to years of use across long maintenance intervals. Even if conventional bearings were repaired, their low load capacity makes bearing life too short for the life of the equipment, so they would still need replacement shortly after. Therefore, longer bearing life is essential for long-term bearing use. In addition, reconditioning requires in-depth inspections of bearing internals at the maintenance site, but conventional bearings use an non-separable structure that makes this difficult.
Features
Utilizing technologies exclusive to NSK, reconditionable large tapered bearings deliver three key features: long service life (high load capacity) for long-term use, a separable structure that allows for detailed examinations of bearing internals, and a staked-bolt design that prevents parts from loosening in environments with vibration. This combination of solutions built on NSK Core Technologies provides an industry-first in reconditionable large TRBs.
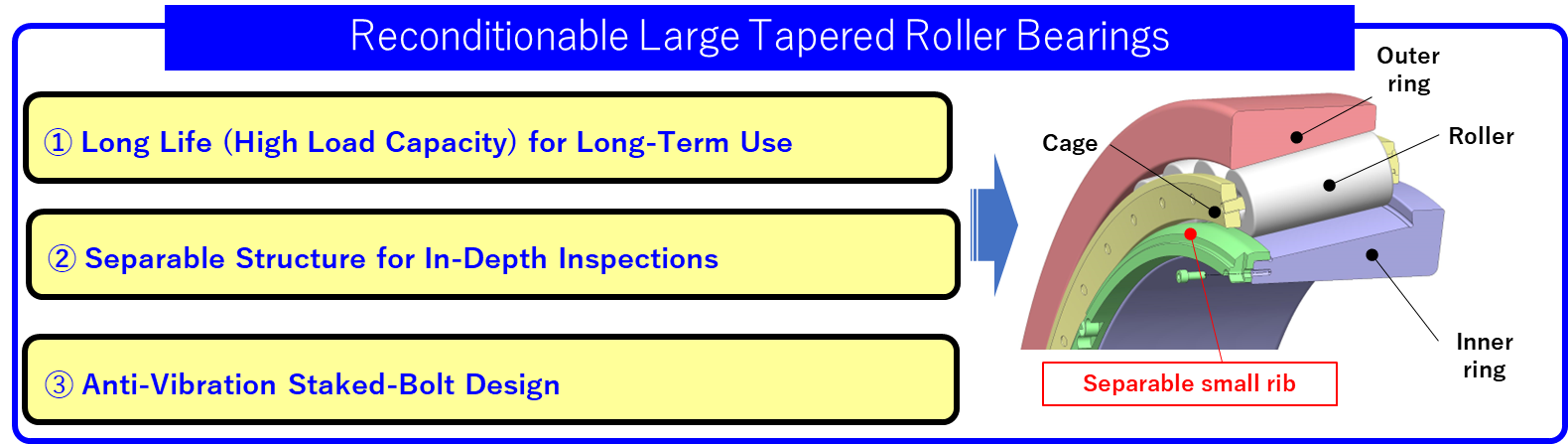

3, 4 Patent pending.
5 Tribology refers to the study of friction and wear between contact surfaces in relative motion and the control of such phenomena through the use of lubrication and specific materials.
1. Long Life (High Load Capacity) for Long-Term Use
Highly accurate bearing life prediction through NSK’s Micro-UT testing delivers a high load capacity design and up to 2x longer bearing life.
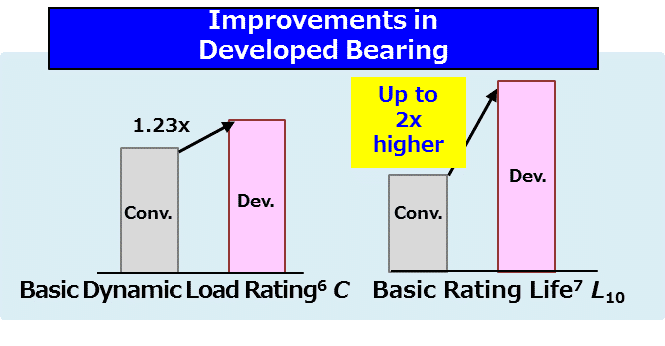
6 The basic dynamic load rating C refers to the constant load that a rolling bearing can endure with a stationary outer ring for 1 million rotations of the inner ring.
7 Basic rating life L10 refers to the total number of rotations (or hours of operation) where 10% of a group of bearings with the same designation operated under the same conditions fail due to flaking from rolling fatigue (90% reliability).
Improvements from Life Prediction Powered by Micro-UT
2. Separable Structure for In-Depth Inspections
In tapered roller bearings, the rollers are guided by rims on the inner ring referred to as the large rib and small rib. In conventional bearings, only the outer ring can be separated easily, but new reconditionable TRBs address this issue with a separable small rib held in place by removeable bolts. With this configuration, the rollers, cage, and inner ring can all be separated, allowing detailed inspections for all parts.
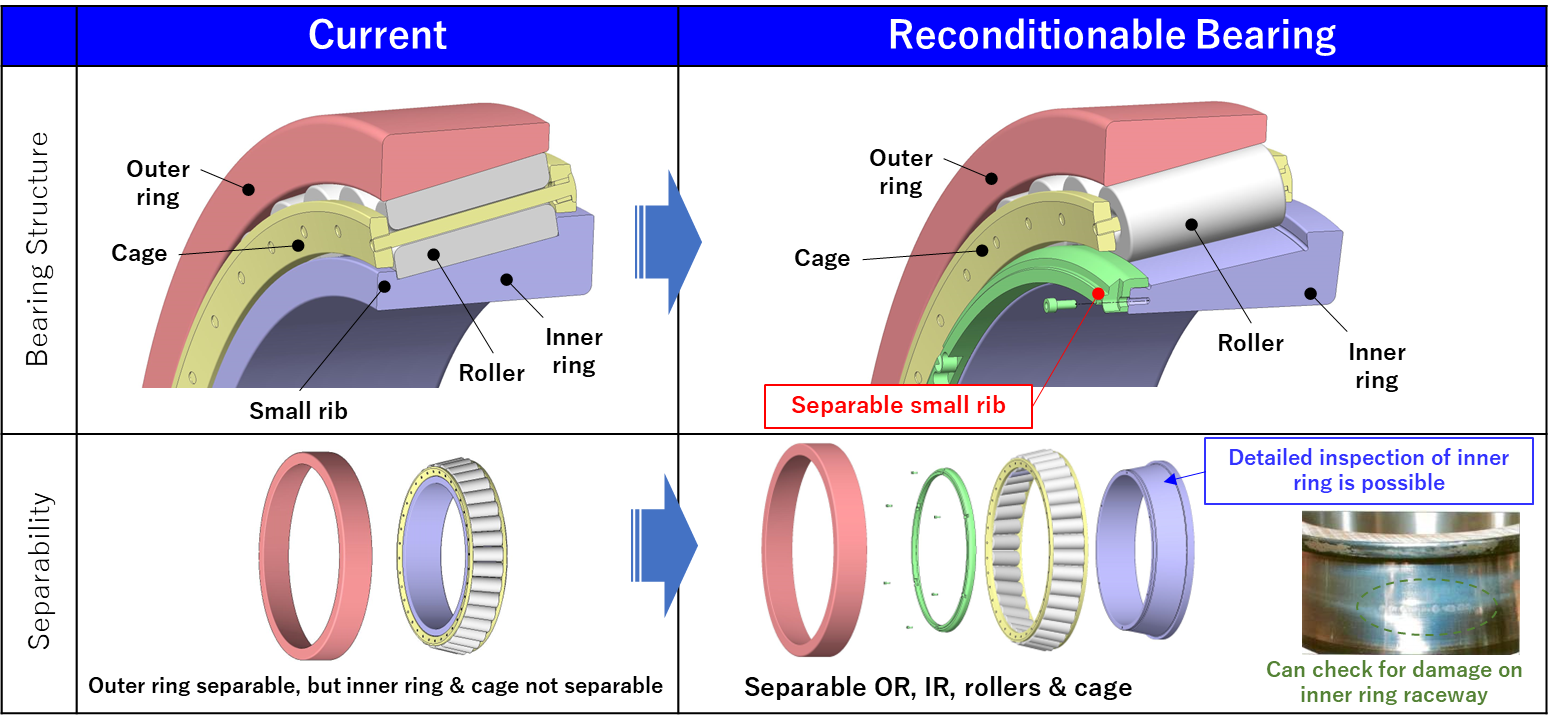
Bearing Structure and Separability (Left: Conventional, Right: Reconditionable Large TRB)
3. Anti-Vibration Staked-Bolt Design
Mining applications are characterized by vibration, which can cause the fasteners for separable parts to become loose or even fall out. The bolts used to hold the separable inner rib of the bearing in place are secured by staked bolt holes to prevent dislocation, helping to further improve reliability in operating environments with vibration.

Staked Design to Prevent Bolt Loosening
Product Benefits
Reconditionable large tapered roller bearings help reduce maintenance costs and cut CO₂ emissions in key equipment in the mining industry.
1) Maintenance Cost Savings (Example)
(From first use of bearing use to second equipment maintenance when bearing is scrapped)
Reconditionable bearings can be repaired and reused, reducing the number of replacements required during equipment maintenance.
Number of bearings replaced per dump truck: 8 ⇒ 4
Number of bearings replaced per crusher: 12 ⇒ 6
2) Reduction of CO2 Emissions (Example)
(From first use of bearing use to second equipment maintenance when bearing is scrapped)
Using reconditionable bearings in the wheels of dump trucks wheels could lead to a 3,102 kg-CO2 reduction across the equipment’s carbon footprint.8
These bearings also serve as a key product and functional example of NSK’s efforts to establish and expand PLM9 models with reconditioning as a core component.
8 Based on NSK carbon footprint calculations of the estimated reduction in CO2 emissions if developed product is used in dump trucks (wheels) at an Australian mine. Usage period: 60,000 hrs, Calculation scope: From procurement of raw materials to scrapping. A calculation report is being prepared for web release.
9 Product Lifecycle Management considers a product’s manufacture and use throughout its entire lifecycle. NSK’s PLM strategy envisions equipment maintenance and repair as a key service after the sale of a product.
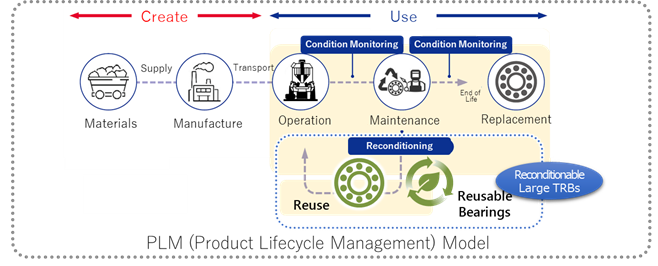
About NSK
NSK produced the first bearings in Japan in 1916 and over the past 100 years, it has supported the development of industries worldwide by creating various innovative products and technologies in bearings, automotive parts, and precision machinery. Since the early 1960s, the company has expanded overseas and now has operations in about 30 countries. It ranks third in the world in the field of bearings and leads the world in ball screws, electric power steering, and other products.