11. 異常・損傷と対策
想定していた期間より、早期に軸受が損傷した場合、再発を防止するため、その原因を的確に見出すことが重要となります。
また、損傷前の音響・振動や温度の変化を把握していることも効果的な対策を見出したり、更なる寿命延長を検討するために役立つことが多々あります。
軸受の損傷
軸受は正しく取扱えば、疲れ寿命に達するまで使用できます。しかし、想定時間より早く損傷し、使用に耐えられなくなることがあります。主に早期損傷は、故障、または事故と呼ばれる性質の使用限度であり、取付け、取扱いなどの組立不良と使用中の温度、潤滑剤の選定ミスなどの設計検討不備によるものです。
初期故障期 | 偶発故障期 | 摩耗故障期 | |
---|---|---|---|
特徴 | 僅かに稼動しただけで、故障 | 安定稼動後に故障が起こる時期 | 部品寿命により故障が増加する時期 |
主な発生原因 | 材料欠陥、組立不良、設計不備、操作ミス | メンテナンス不良、使用環境変化 | 寿命 (摩耗・疲労、経年劣化) |
主な故障低減策 | 慣らし運転、異音・振動・温度確認 | 保守品質維持または変化に応じた保守改善、潤滑剤交換、適正運転の徹底 | 予防保全(事前予知に基づく部品交換など) |
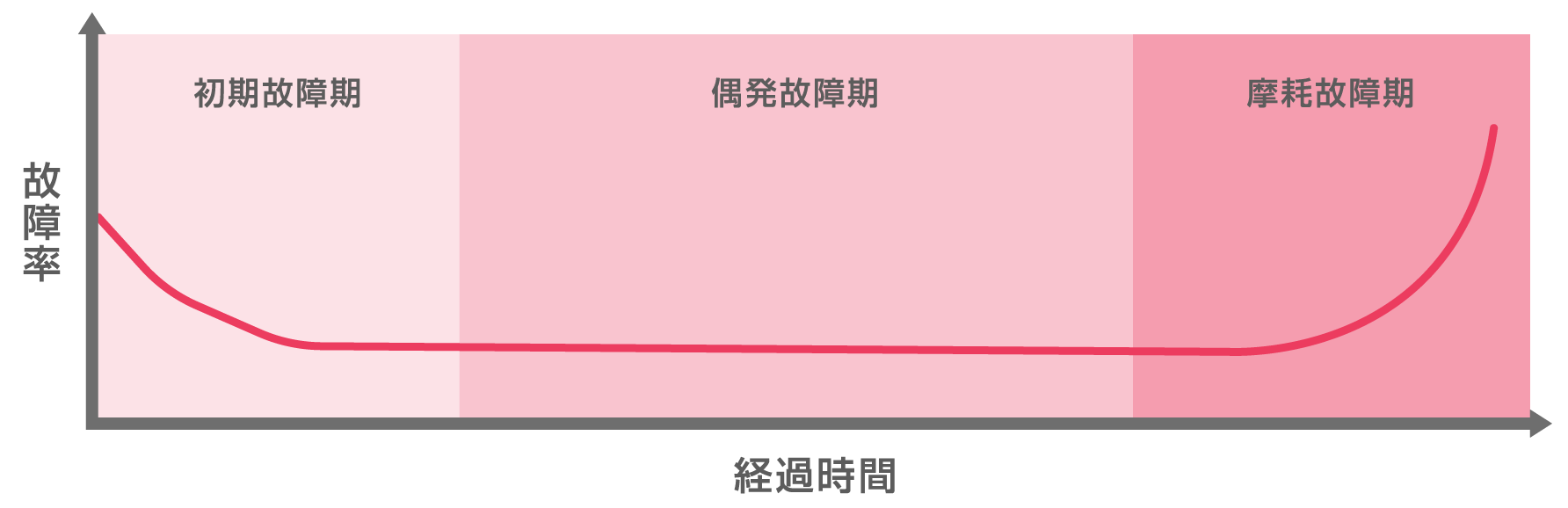
バスタブ曲線(故障率曲線)
発生時期と推定原因
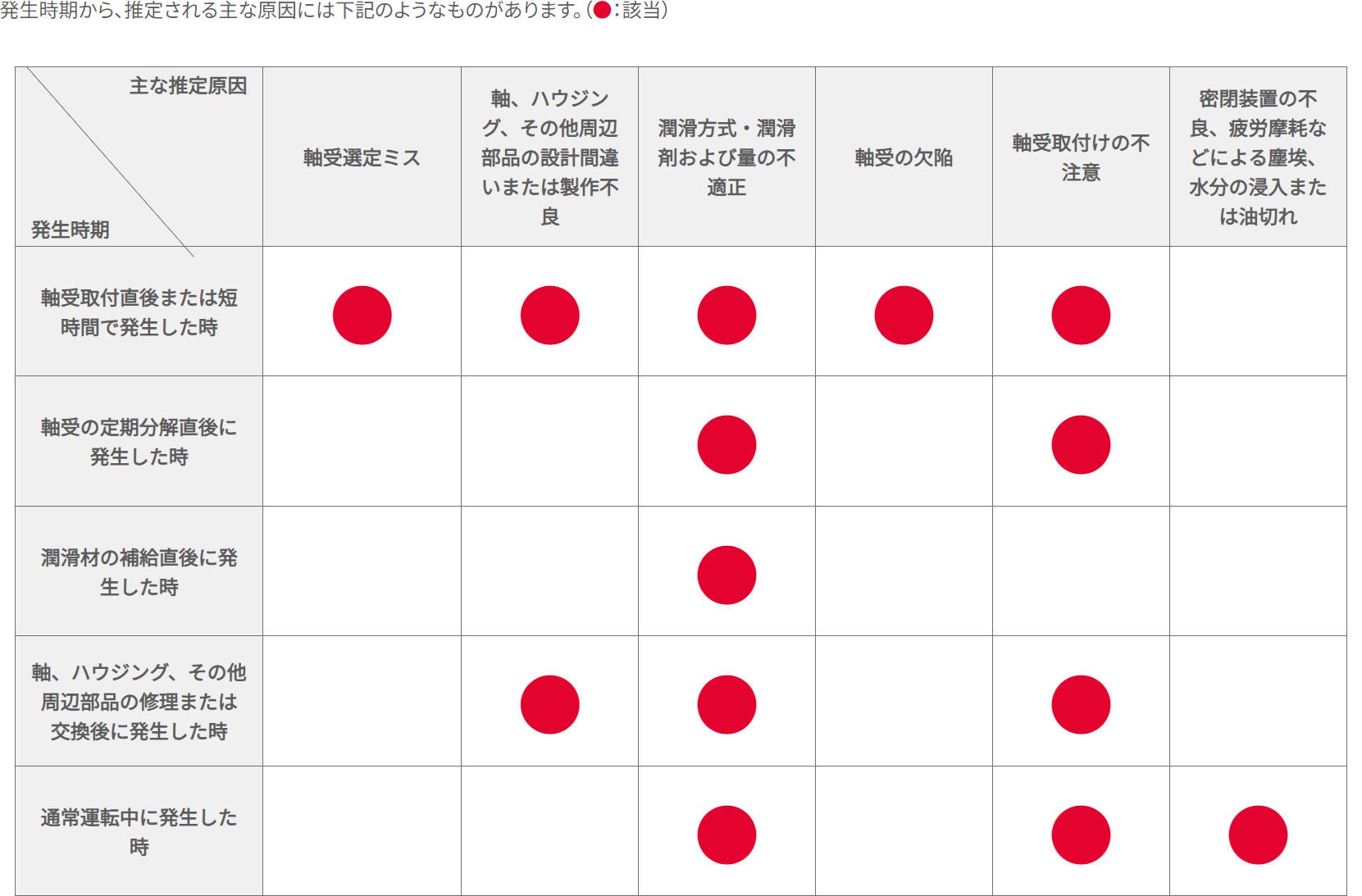
運転状態と推定原因
運転状態から、推定される主な原因には下記のようなものがあります。
運転状態 | 主な推定原因 | ||
---|---|---|---|
騒音 | 低い金属音 |
| |
高い金属音 |
|
| |
不規則音 |
|
| |
漸次変化する音 |
|
| |
異常温度上昇 |
|
| |
精度低下 |
| ||
スムーズでない運転 |
|
| |
潤滑油の汚染 |
|
|
走行跡と荷重のかかり方(深溝玉軸受の場合)
軌道面は転動体との転がり接触で走行跡がくすんだ色になります。この着色自体は異常でありません。下図(a)~(d)は一般的に見られる走行跡です。しかし、下図(e)~(h)の走行跡は軸受に悪影響を与え、多くは短寿命になる可能性があります。
正常な走行跡
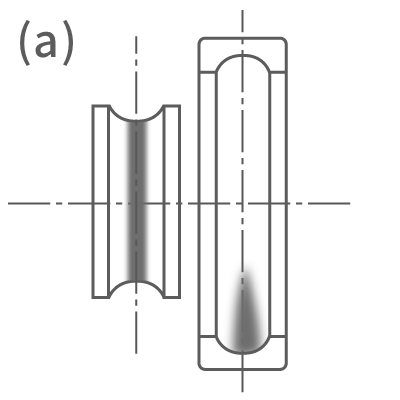
内輪回転
ラジアル荷重
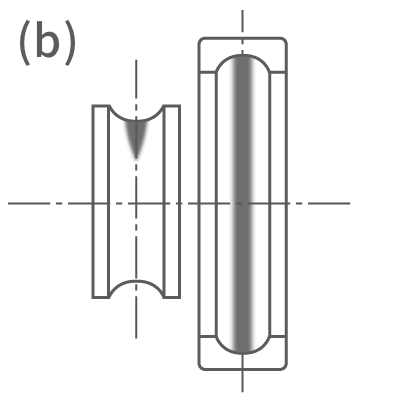
外輪回転
ラジアル荷重
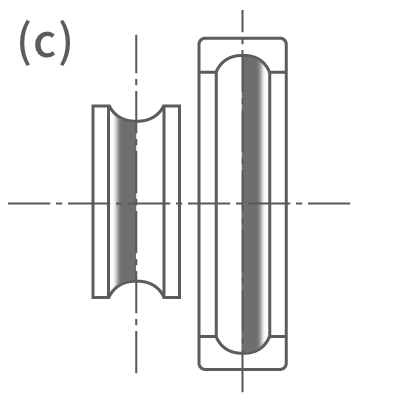
内輪または外輪回転
一方向アキシアル荷重
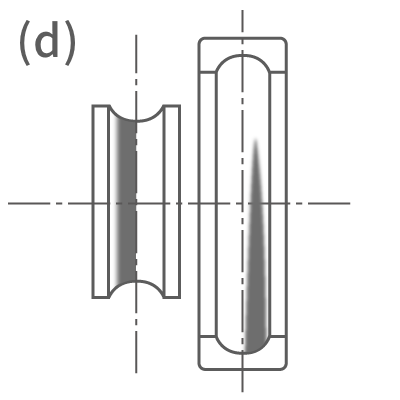
内輪回転
ラジアルおよび
アキシアル荷重
短寿命になる可能性がある走行跡
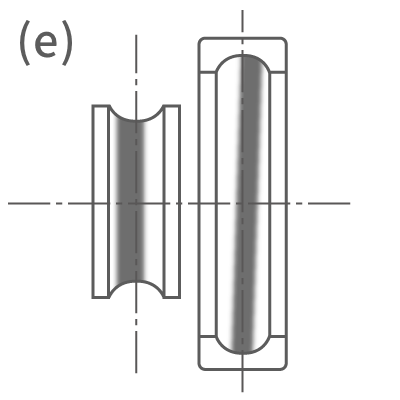
内輪回転
アキシアル荷重および
ミスアライメント
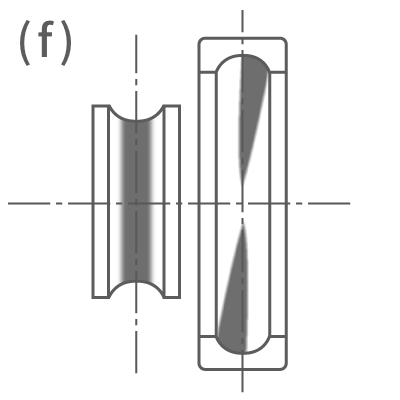
内輪回転
モーメント荷重
(ミスアライメント)

内輪回転
ハウジング内径が楕円

内輪回転
軸受内部すきまがない
(運転すきまがマイナス)
走行跡と荷重のかかり方(ころ軸受外輪の場合)
外輪の軌道面は、転動体との転がり接触で走行跡がくすんだ色になります。走行跡が軌道面につくことは異常でなく、それにより負荷条件を知ることができます。
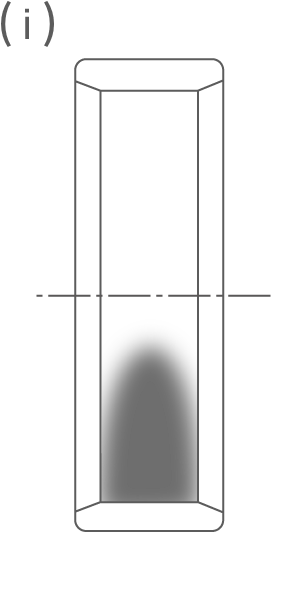
内輪回転
ラジアル荷重
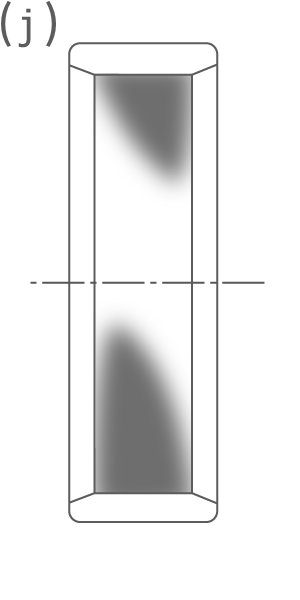
内輪回転
モーメント荷重
(ミスアライメント)
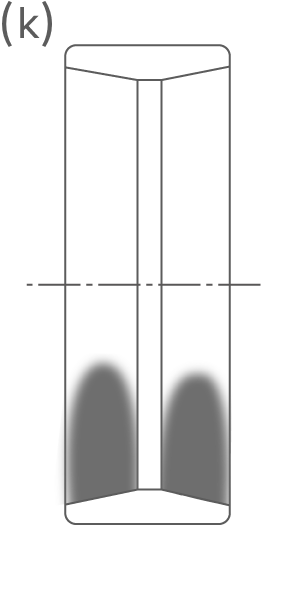
内輪回転
ラジアル荷重
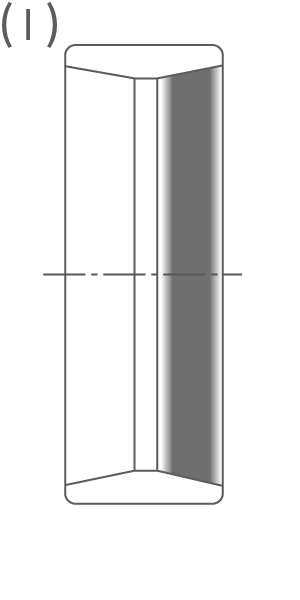
内輪回転
アキシアル荷重
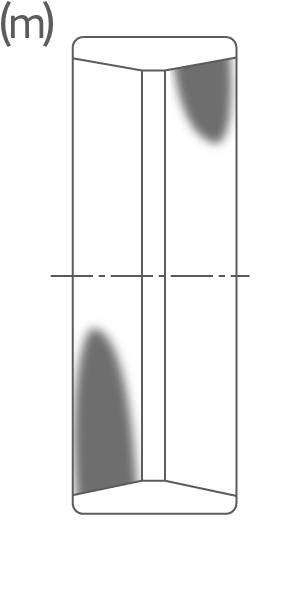
ラジアル荷重および
モーメント荷重
(ミスアライメント)
(i)、(j):単列円筒ころ軸受N形の外輪
(k)、(l)、(m):複列円すいころ軸受KBE形の外輪
軸受の損傷と対策
フレーキング(スポーリング、はく離) | |
---|---|
損傷状態 | 軸受が荷重を受けて回転した時、内輪/外輪の軌道面または転動体の転動面が転がり疲れによって、 うろこ状にはがれる現象。 |
原因 |
|
対策 |
|
損傷例 |
|
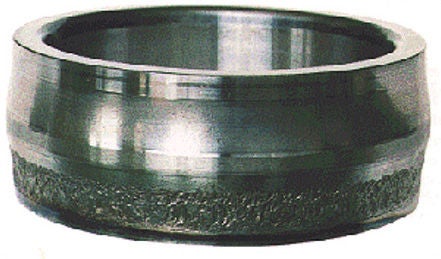
損傷写真
フレッチング | |
---|---|
損傷状態 | 二面間の相対的繰り返し微少滑りによって生じる摩耗。 軌道輪と転動体との接触部や はめ合い面に生じます。 赤褐色または黒色の摩耗粉を発生することからフレッチングコロージョンとも言います。 |
原因 |
|
対策 |
|
損傷例 |
|
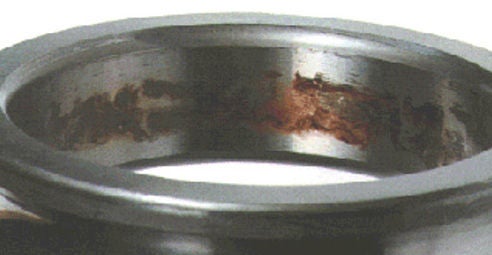
損傷写真
圧こん | |
---|---|
損傷状態 | 金属の微粉、異物などをかみ込んだ時に軌道面または転動面に生じるへこみ。 取付時などの衝撃による転動体ピッチ間隔にできるへこみ。 |
原因 |
|
対策 |
|
損傷例 |
|
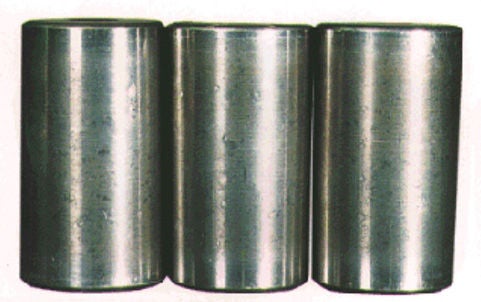
損傷写真
電食 | |
---|---|
損傷状態 | 電食とは、軸受の軌道輪と転動体との接触部分に電流が流れた場合、薄い潤滑油膜を通してスパークし、 その表面が局部的に溶融し、凹凸となる現象。 なし地状に見える部分は小さなへこみ(クレータ、またはピットと呼ばれます)の集合体であり、軸方向の縞模様の凸凹をフルーチング(またはリッジマークとも呼ばれます)、円周方向に生じる溝をグルービングと呼びます。 |
原因 |
|
対策 |
|
損傷例 |
|
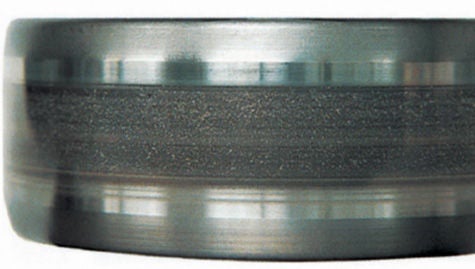
損傷写真
焼付き | |
---|---|
損傷状態 | 回転中、急激に発熱し軌道輪、転動体および保持器が変色、軟化、溶着し、破損に至ります。 |
原因 |
|
対策 |
|
損傷例 |
|
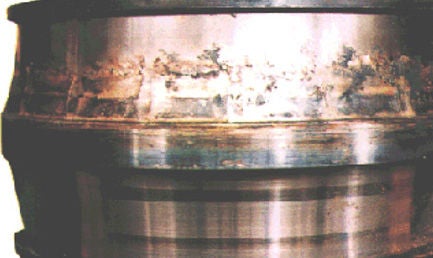
損傷写真
変色 | |
---|---|
損傷状態 | 温度上昇や潤滑剤との反応などによって、軌道輪、転動体、保持器が着色すること。 |
原因 |
|
対策 |
|
損傷例 |
|
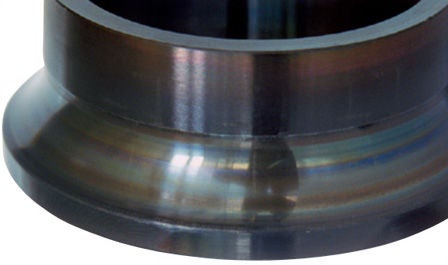
損傷写真
かじり | |
---|---|
損傷状態 | かじりとは、滑り面などに生じる部分的な微少焼付きの集成によっておこる表面損傷。 軌道面、転動面の円周方向の線状の傷。 ころ端面のサイクロイド錠の傷。ころ端面に接するつば面に生じる傷。 |
原因 |
|
対策 |
|
損傷例 |
|
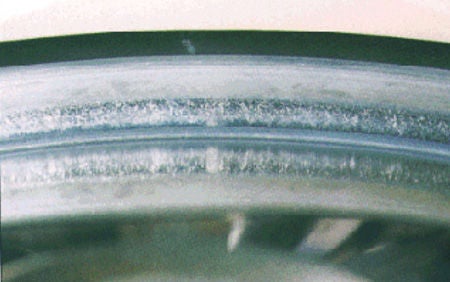
損傷写真
組込み傷 | |
---|---|
損傷状態 | 取付け、取外しなど取扱い時に軌道面および転動面に付いた軸方向の線傷。 |
原因 |
|
対策 |
|
損傷例 |
|
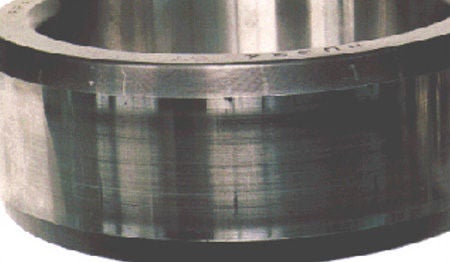
損傷写真