精機製品・技術レポート:低発塵性LG2グリースの実用性能
近年、情報産業の発展はめざましく、半導体や液晶製造設備に使用されるボールねじ、リニアガイド、転がり軸受の数量は急増している。これらの製造設備においては、ボールねじや転がり軸受などから潤滑グリースが飛散し、その製品例えばウエハに付着すると製品価値を喪失するため、低発塵性グリースの開発が強く望まれてきた1)
現在、真空環境だけでなく常圧環境で使用される半導体や液晶製造設備のボールねじ、転がり軸受などに対しても、蒸発量の少ない真空用フッ素系グリースが多く使用されている。しかし、一般にフッ素系グリースには、高粘度の基油が使用され、さらに防錆添加剤がほとんど配合されていない。
このため、次のような問題点がしばしば指摘されている。
(1) 摩擦トルクが大きく、発熱やモータ過負荷の原因となる。
(2) 鉱油や合成油系のグリースと比較して耐摩耗性能に劣り、比較的短時間で摩耗を生じさせることもある。
(3) 在庫中にさびを発生させやすい。
そこで、NSKではこれらの問題点を改善するため、発塵量が少なく、耐摩耗性、防錆性に優れ、さらに低トルク性能をも兼ね備えたLG2グリースを開発した。
ここに、市販のグリースと比較して、ボールねじや転がり軸受などで使用したときのLG2グリースの実用性能を紹介する。
2. LG2グリースの組成と代表性能
LG2グリースと比較のために用いた市販グリースの組成と代表性状を表1に示す。LG2は、基油として鉱油と合成炭化水素油とのブレンド油を用い、リチウム石けんを増ちょう剤としたグリースである。多くの試作と評価の繰り返しによって、最適組成を決定し、さらに製造条件の厳密なコントロールの末に低発塵性を実現した。
また、添加剤配合にも細心の注意を払い、重金属化合物やウエハなどに悪影響を与えるものは含んでいない。
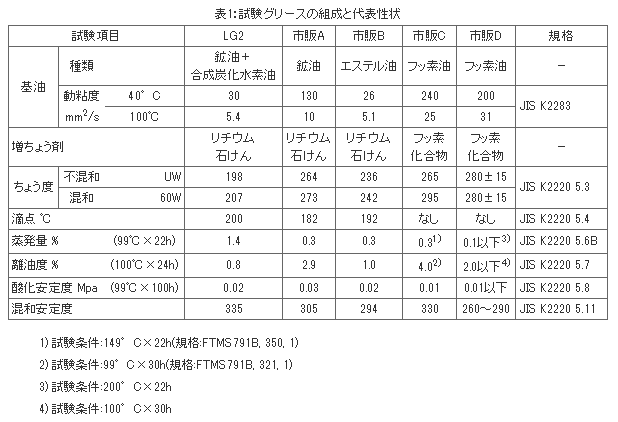
3. 発塵性能
3.1. 発塵量測定装置と測定方法
ボールねじからの発塵量測定装置を図1に、転がり軸受からの発塵量測定装置を図2に示す。ボールねじはカップリングを介してモータ駆動され、磁性流体シールが装着されているため、ボールねじからの発塵粒子だけが測定されるようになっている。軸径15mm、リード10mmのボールねじを使用し、有機溶剤で洗浄・乾燥後、ボールナットの空間部にグリースを2.2ml 充填した。測定装置を25℃に保持したクリーンベンチ内に設置し、1000rpmでストローク210mm動かして、光散乱式のパーティクルカウンタで発塵粒子を測定した。リニアガイドの場合もほぼ同じ形式の測定装置を使用した。ミニアチュアリニアガイド(LU09)を使用し、線速度110mm/sでストローク23mm動かした。
転がり軸受は、ベルトを介してモータ駆動され、磁性流体シールを装着した清浄な箱の中に収められている。一定流量の清浄空気を流し、軸受の回転によって発生する発塵粒子をボールねじと同様にパーティクルカウンタで測定した。
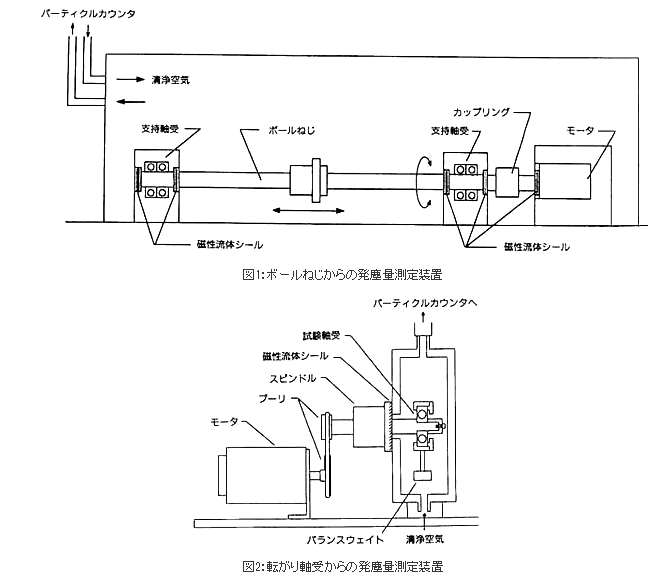
3.2. ボールねじからのグリース発塵量
LG2グリースと市販グリースとの発塵量の比較を図3に示す。鉱油-リチウム石けん系Aグリースとエステル・鉱油-リチウム石けん系Eグリースが多量の発塵を示した。フッ素系C、Fグリースは、市販グリースの中では発塵量の少ない方であったが、使用時間の経過とともに発塵量が増加する傾向にあった。それに対し、LG2グリースは時間の経過と共に発塵量が減少した。僧ちょう剤量の多いグリースが発塵しにくい傾向にあると言える。
ボールねじにシールを装着したときと、しないときのLG2グリースの発塵量測定結果を図4に示す。シールを装着することにより、発塵量は1/10以下に減少し、シールによる発塵防止効果が大きい。
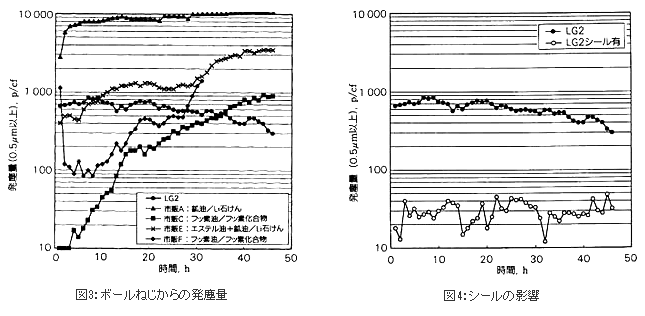
3.3. リニアガイドからのグリース発塵量
LG2とフッ素系Cグリースとの発塵量の比較を図5に示す。ボールねじの場合よりも発塵性能の差が大きく、LG2が極めて良好な結果を示した。
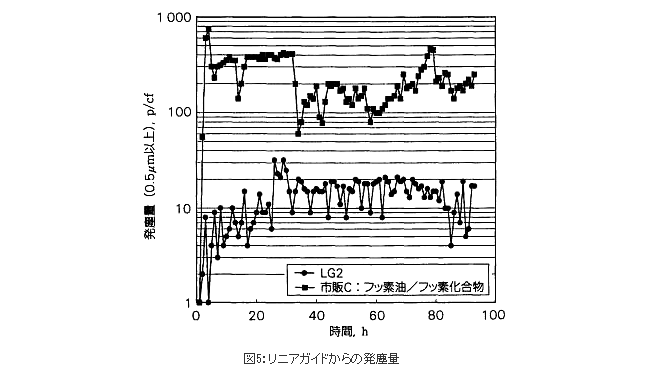
3.4. 転がり軸受からのグリース発塵量
非接触型のゴムシールを付けた小径玉軸受695VV(内径5mm、外径13mm、幅4mm)を3600rpmで回転させたときのグリース発塵量を図6に示す。市販グリースに比べ、LG2グリースは良好な低発塵性を示した。市販グリースの中では、エステル油-リチウム石けん系Bグリースの発塵量が際立って多く、鉱油-リチウム石けん系Aグリース、合成炭化水素系-ウレア系EA2グリースの順に発塵量が少なくなった。フッ素系グリースは銘柄による差が大きかった(市販C、D)。ウレア系グリースは、市販グリースの中では発塵量が少ない方であったため、上記EA2グリースとはウレア構造の異なるエーテル油-ウレア系Gグリースをも評価してみた。上記と同じ玉軸受を5400rpmで250時間まで回転させたところ、図7に示すようにウレア系Gグリースは、回転初期にはLG2グリースに近い低発塵量を示したものの、回転時間の経過とともに発塵量が急増した。
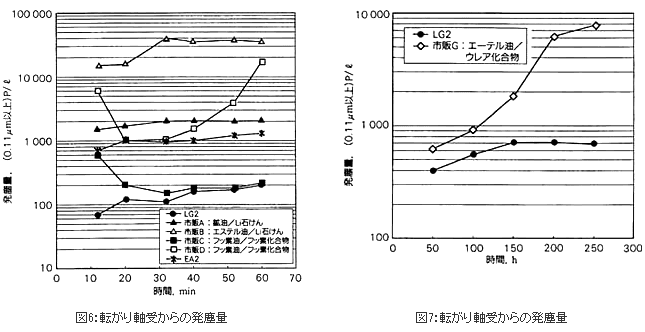
3.5. 発塵粒子の粒径分布
玉軸受695VVを3600rpmで、20分間回転させたときの発塵グリースの粒径分布を図8に示す。いずれのグリースの場合も粒径の小さな粒子が特に多く、粒径が大きくなるに従い発塵量が減少した。発塵量の差は、主に小さな粒子の生成し易さに起因していると言える。
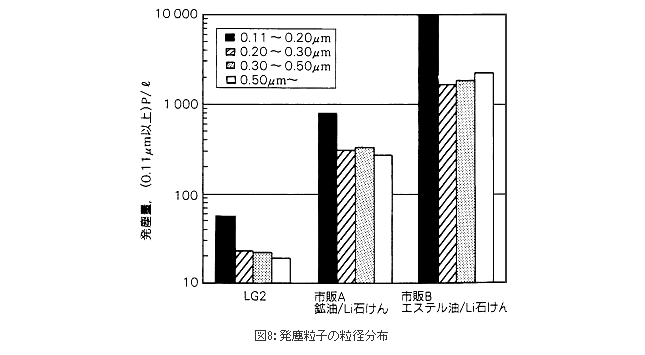
3.6. 発塵物質の同定
玉軸受695VVから最も多量に発塵したエステル油-リチウム石けん系グリースについて、発塵物質を調べた。図9に発塵物質の赤外線吸収スペクトルを示す。発塵粒子数測定用のパーティクルカウンタの前に金属板を取り付け、金属板に付着した物質をFTIRで分析した。スペクトルチャートから明らかなように、リチウム石けんによるカルボニル基の吸収(1555、1585cm-1)とエステル油によるカルボニル基(1740cm-1)の吸収が認められた。従って発塵物質はグリースそのものである。
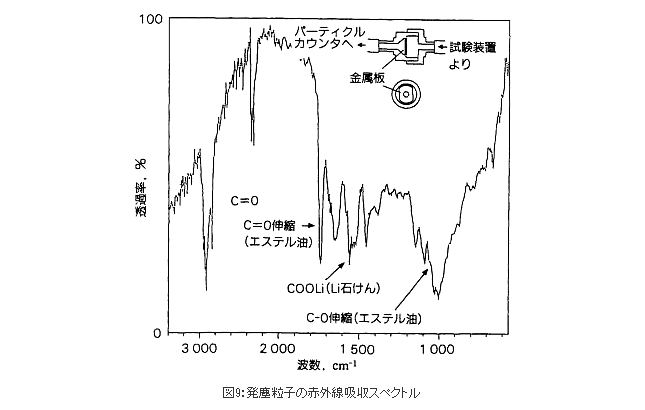
3.7. 雰囲気温度の発塵に及ぼす影響
LG2グリースと発塵しやすいエステル油-リチウム石けん系Bグリースを、上記と同じ玉軸受に封入し、3600rpm、70°Cで回転させた。回転20分後の発塵量の測定結果を図10に示す。両者とも温度の上昇と共に発塵量が急増した。LG2グリースは、鉱油と合成炭化水素油とのフレンド油であり、低粘度のため高温になるに従い蒸発量も増加する。単なる潤滑性能だけでなく、低発塵性の維持をも考慮すれば、雰囲気温度70°C程度が使用限界と考えられる。
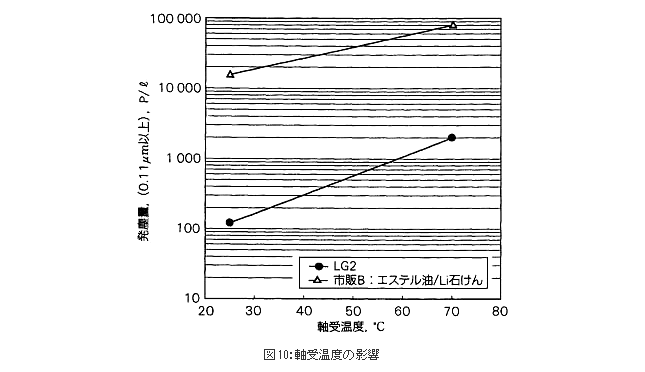
3.8. 回転速度の発塵に及ぼす影響
LG2グリースとフッ素系Dグリースを封入した玉軸受695VVを1800、3600、5400rpmで回転させたときの発塵量の測定結果を図11に示す。
また、フッ素系Fグリースを封入したボールねじの回転速度を100から1760rpmまで増加させたときの発塵量の測定結果を図12に示す。回転速度が2倍になると、いずれのグリースも発塵量が約10倍に増加した。グリースの発塵に対し、遠心力の影響の大きいことがわかる。
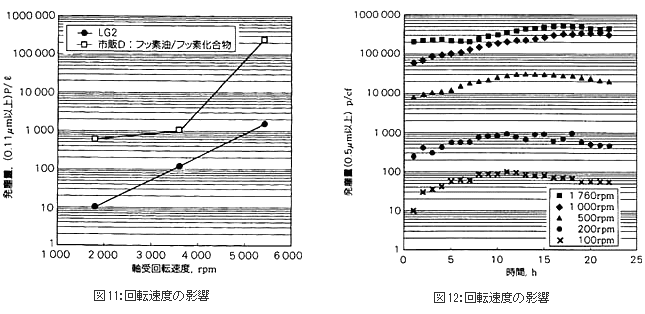
4. 動トルク性能
4.1. 動トルク測定方法
軸径25mm、リード5.08mm、ダブルナット予圧方式のボールねじに、5mlのグリースを入れ、回転速度を500rpmまで順に上昇させながらナットに取り付けたロードセルによって、動トルクを測定した。
4.2. ボールねじの動トルク測定結果
LG2グリースとフッ素系Cグリースの動トルク測定結果を図13に示す。LG2グリースに比べて基油動粘度が約8倍のフッ素系Cグリースは、回転速度の増加と共に、急速に動トルクが増加した。それに対しLG2グリースでは、500rpmまでほとんど動トルクが一定で増加が見られなかった。
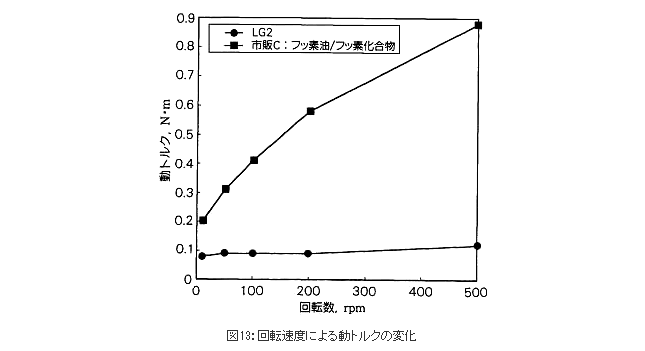
5. 耐久性・耐磨耗性能
5.1 ボールねじ耐久試験方法
軸径14mm、リード5mmのボールねじに1.5ml(ナット空間容積の50%)のグリースを入れ、回転速度2400rpmで、アキシアル荷重280Nを負荷し、耐久試験を行った。試験後の軸方向のすきまを測定し、摩耗状況を把握した。
5.2. ボールねじの耐久試験結果
LG2グリースとフッ素系Cグリースとを封入したボールねじの耐久試験結果を図14に示す。フッ素系Cグリースは、360km走行時点ですでに摩耗が進行しており、12μmもの軸方向すきまを生じた。一方、LG2グリースでは3500km走行後も摩耗した形跡はなく、全く異常は認められなかった。

5.3. リニアガイド耐久試験方法
リニアガイド(LS20)の軸受部にグリースを満たし、予圧1.37kNをかけ、線速度30m/minでストローク500mm動かした。走行距離1000km毎にプッシュプルゲージを用いて動摩擦力を測定した。
5.4. リニアガイドの耐久試験結果
LG2グリース、EA2グリース及びフッ素系Cグリースを封入したリニアガイドの耐久試験結果を図15に示す。フッ素系Cグリースでは、3000km走行後多量の摩耗を生じ、5000kmでエンドキャップが破損した。一方、LG2、EA2グリースでは、10000km走行後でもほとんど摩耗が見られず、剛性も問題ないレベルにあった。
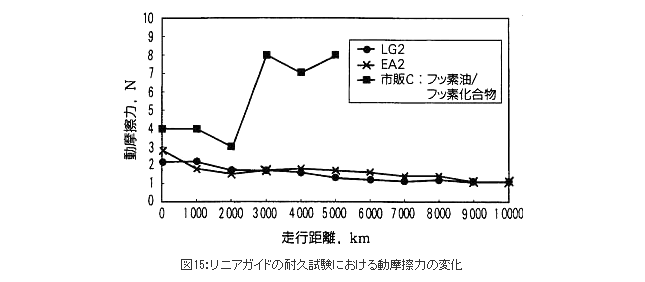
6. 防錆性能
6.1. 防錆試験方法
浸炭鋼(SCM420H)を用いたボールねじに約10μmの厚さでグリースを塗布し、相対湿度95%、雰囲気温度70℃の中に96時間放置した。試験後の錆発生状況を観察した。
6.2. 防錆試験結果
写真1に示すように、フッ素系Cグリースは、防錆剤配合タイプであるにもかかわらず、ボールねじ表面に多量の赤さびの発生が認められた。一方、LG2グリース塗布ボールねじでは、全くさびの発生が見られなかった。
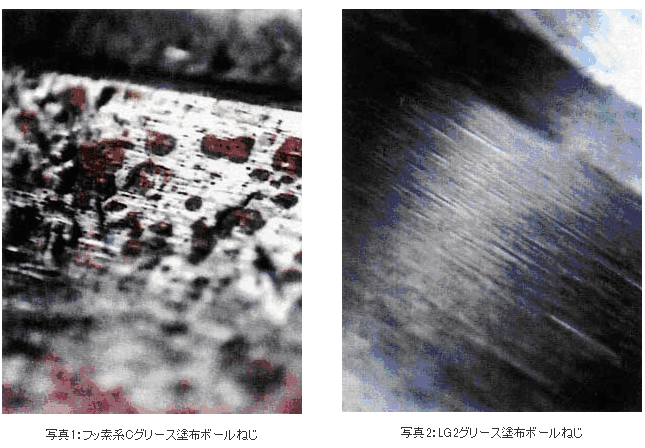
7. まとめ
(1) LG2グリースは、半導体や液晶製造装置などの中で常温・常圧のクリーン環境で使用されるボールねじ、リニアガイド、転がり軸受に最適なグリースである。
(2) LG2グリースは、市販されているグリースよりも発塵量が少なく、さらに耐摩耗性、低トルク性能、防錆性能にも優れている。
(3) 発塵物質は、グリースそのものであり、粒径の小さな粒子が多い。グリースによる発塵量の差は、主に小さな発塵粒子の生成しやすさの違いによるものである。
(4) 雰囲気温度、回転速度の増加は、グリースの発塵量を急増させる。低発塵性能の維持を考慮すれば、LG2グリースの使用限界は、70℃程度と考えられる。
参考文献
1) 三宅正二郎: “クリーン環境用軸受”、精密工学会誌、57(4)27 (1991)