Eliminating Bearing Failures in High-Temperature Concrete Thickener Applications
A paving producer in Poland was facing repeated equipment breakdowns due to frequent bearing failures in its vibrating thickener machine. Over the course of just four months the bearings, which were installed within an electric motor, failed an astonishing 10 times. Each failure required a minimum of two hours of downtime for replacement.
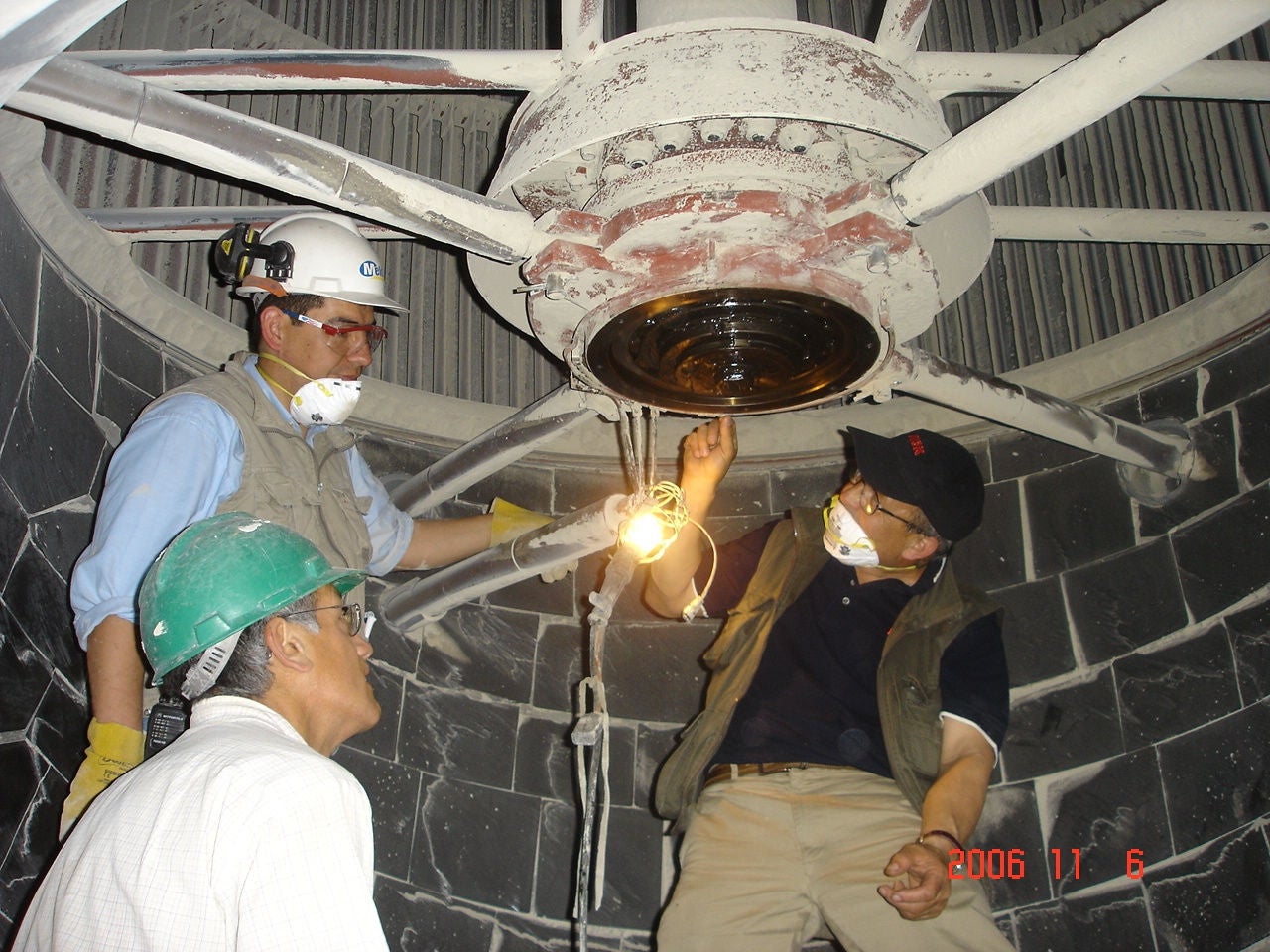
We saved them €32,100
The company asked NSK for help and our team of highly-trained engineers conducted a thorough Application Review. The found that, in an environment where operating temperatures regularly exceeded 110°C, the existing shielded Deep Groove Ball Bearings were unable to withstand the high temperatures and strong vibrations they were subjected too. Specifically, they determined that the root cause of the failure was grease leakage and overheating, which were directly leading to the breakdowns.
"NSK’s tailored high-temperature bearing technology can deliver outstanding reliability in harsh, vibration-intensive environments."
Anton Mozhaev, NSK Europe’s Sector Manager for Cement
NSK advised the company to adopt a more robust solution, Deep Groove Ball Bearings with high temperature fluorine rubber contact seals, specially selected heat-stabilised steel rings, and C3 internal clearance to accommodate the thermal expansion and dynamic loads. These enhancements were designed to prevent (or at least drastically reduce) grease leakage, maintain optimal internal temperatures, and prolong bearing service life under even these demanding conditions.
The company agreed to try the solution on a trial basis. Over the course of four months (the same duration they had endured the regular failures) the company operated without any bearing failures or any maintenance interventions.
Want to learn more about how NSK can reduce your downtime and costs?
Click the button below to contact us and we'll put you in touch with one of our sales representatives who will help you find the right solution at the right cost.
‘This success story highlights how NSK’s tailored high-temperature bearing technology can deliver outstanding reliability in harsh, vibration-intensive environments,’ said Anton Mozhaev, NSK Europe’s Sector Manager for Cement. ‘By understanding the specific challenges of the application and engineering a targeted solution, NSK enabled the customer to achieve long-term stability, efficiency, and significant cost reductions.’
In conclusion, by switching to the high-temperature solution, the customer completely eliminated the need for unplanned maintenance and therefore downtime, and went from needing to replace their components 10 times in a four month period to not at all. These improvements led to not just greater operational reliability but a total cost saving of €32,100.
Share