自動運転EVに向けた新提案「クラスター・ローバー・モジュール」2輪のインホイールモーターで快適に
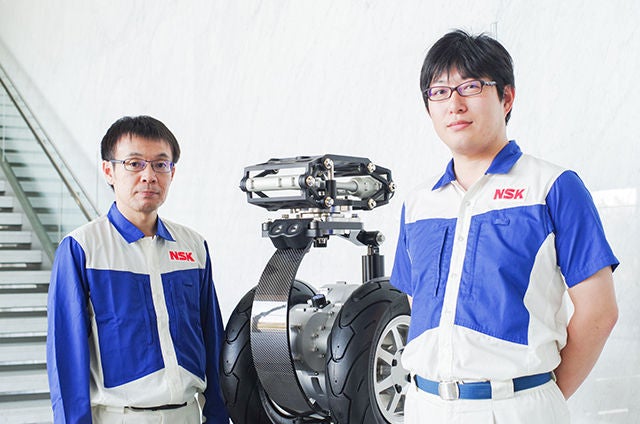
NSKは「第46回東京モーターショー2019」で、「あたらしい動きをつくる。」というコンセプトのもと、数々の技術展示を行いました。展示では、波の力でエネルギーを生み出す「波力発電」や非接触で電力を効率よくクルマに伝える「走行中ワイヤレス給電」、自動運転のEV用の駆動モジュール「クラスター・ローバー・モジュール」など、未来のエネルギー作りから、それを伝え、使うまでの技術を発表。新たな技術を実現するため、日々開発を続けています。
今回は、クラスター・ローバー・モジュールの開発担当者である自動車事業本部 自動車技術総合開発センター パワートレイン技術開発部の疋田真史と、同部の森田竜峰に、仕組みや開発を始めた経緯、NSKがこの技術を研究する意義などを聞きました。
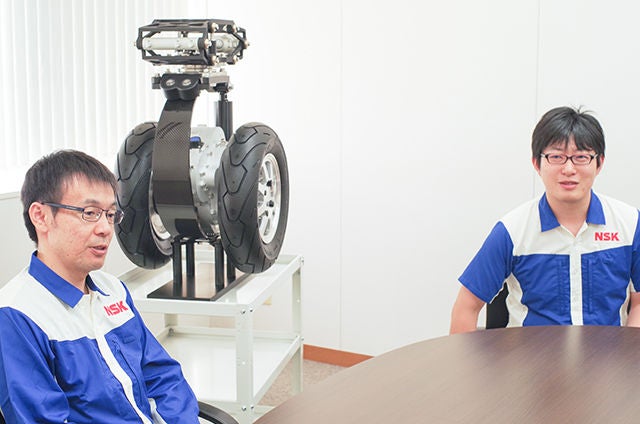
パワートレイン技術開発部の疋田真史(写真左)と森田竜峰(写真右)
2つのインホイールモーターの回転差で曲がる新発想
── クラスター・ローバー・モジュールとは、どのようなものなのでしょうか?
疋田 自動走行をするEVに関連する技術で、自分で所有するクルマというより、公共交通機関の箱型車両の駆動モジュールを想定して開発しています。
特徴は2つ。1つ目は、共通化した駆動モジュールを車両のサイズにあわせて、搭載する数を調整する点です。例えば、小さな車両であれば4機、大きな車両ならば8機といった具合に、どんなサイズの車両に対しても、1種類のモジュールで対応できることが特徴と言えるでしょう。2つ目は、駆動モジュール自体に「走る」「曲がる」「止まる」という機能を集約しており、さらに荷重を測る機能や車高を調整する機能まで備えていることです。
森田 構造を説明しますと、まず一番下に2輪をそれぞれ駆動するインホイールモーターとブレーキが一体化されています。その上に衝撃を吸収するカーボンファイバーの板状のスプリングとダンパーがつながっており、さらに一番上には車高を調整するパンタグラフジャッキが搭載されています。パンタグラフジャッキにはボールねじ式の直動アクチュエータがあり、ねじを回転させることでアクチュエータが伸縮し、車高を変更できる仕組みです。
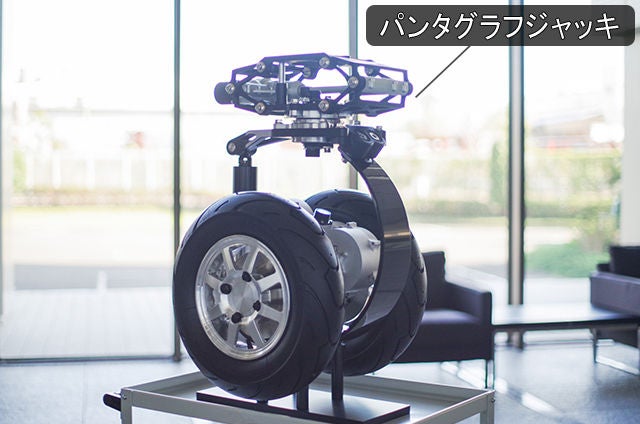
特徴的なのは、操舵を行うアクチュエータがないこと。パンタグラフ部は車体に固定されていますが、その下の部分はフリーに回転できるようになっていて、左右2輪それぞれの回転速度に差をつけたり、回転する向きをそれぞれ逆向きにしたりすることで曲がることができます。「走る」に加えて「曲がる」の機能を実現するために、1モジュールにつき2輪あるわけですね。
曲がるためのアクチュエータを採用していないのは、モジュールの方向を変えるとき以外は使われない、使用頻度の低いパーツになってしまうから。また、車輪の方向を変えるには大きな力が必要で、曲がるためのアクチュエータを搭載する場合は、必然的に大きなモーターを使うこととなります。2輪にすることで、それを採用する必要がなくなるのは、大きなメリットでした。
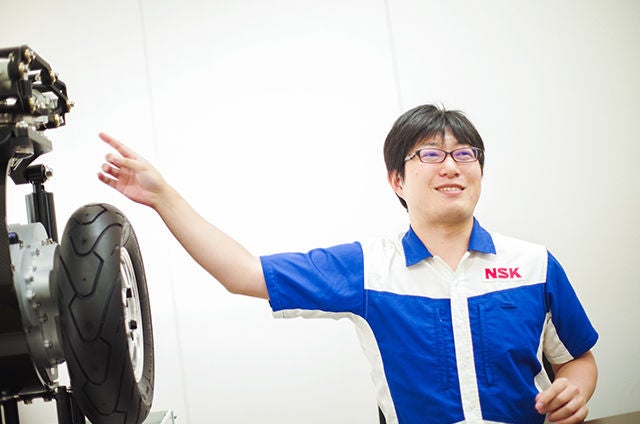
疋田 この構造ですと、車体を支えるバネレート(スプリングの硬さ)と車高調整機能が独立しており、それぞれを自由に設定できます。このため、車高調性により車高を変えても最適な乗り心地を維持できます。通常のエアサスペンションでは、バネレートと車高の関係を切り離すことができません。
現在開発しているものでは、1輪のホイールサイズが10インチで、タイヤはオートバイ用です。1輪当たりの出力は12kWなので、1機のモジュールで24kW。4機使えば96kWになり、小型車として十分なパワーになります。箱型の自動運転のEVということで、それほどスピードを出すことは想定していません。最高でも時速50㎞程度です。
通常のサスペンションよりもシンプルな形状なので、部品点数が少なく、スペース効率に優れています。もし故障したときはモジュールごと交換すればいいだけなので、修理が簡単なのもポイントです。
未来に必要な技術を考え、それに挑戦することで知見を広げる
── どうしてNSKで、このようなものを開発することになったのでしょうか?
疋田 当社では、未来の自動車には何が必要になるのかを、よく話し合っています。地球環境の変化や技術の進歩が起きた先にどういう部品が必要になるのか、発想をぶつけあってブラッシュアップしているんですね。
将来的に電動化や自動化、「サステナビリティ」をベースとした企業の取り組みが進むことから考えて、「波力発電」や「走行中ワイヤレス給電」、自動運転車の駆動モジュールである「クラスター・ローバー・モジュール」という解が出てきました。
クラスター・ローバー・モジュールで言えば、公共の交通機関の自動運転が実用化されるときに問題になるのは、いかに快適に過ごせるかだと思います。やはり広いほうがイイだろうと、クルマは箱型になるんじゃないかと考えました。そこで必要になるのが、新しい駆動モジュールです。
アイデアをまとめて形にするのにかかったのは1年ほどでした。意外に早く実行できたのは、インホイールモーターの減速機を小さくする技術やパンタグラフのアクチュエータ構造など各要素の部品に、当社が過去に取り組んできた技術を採用したのが大きな理由です。
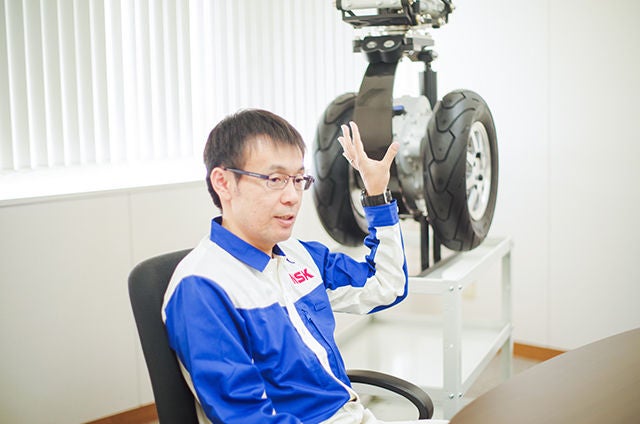
── 軸受メーカーのNSKが、そうした新しいことにチャレンジする意義は、どんなところにあるのでしょうか。
疋田 当社がクラスター・ローバー・モジュールを製品として量産していくことはあまり考えていません。どちらかと言えば、そこに使われる軸受やボールねじ、アクチュエータなどの部品が当社のビジネスとなるでしょう。
モジュール全体を開発する利点は、部品の使われ方を先行して把握することができ、最適な軸受やアクチュエータの設計ができる点。将来的に、箱型の自動運転EVの駆動モジュールは、当社が予測する形そのものにはならないかもしれませんが、機能としては大きく外れていないのではないでしょうか。
森田 クラスター・ローバー・モジュールの開発は、当社としては新たなプロジェクトで、取り組む上でいろいろと勉強になりました。当社はスプリングの知見は、そんなにあるわけでもありませんし、パンタグラフの構造も荷重センサーも新たな挑戦です。
さまざまなアプリケーションを作ってみないと、適応する軸受やボールねじのノウハウも蓄積されません。そうした意味で、新しいことに挑戦することで、今後の可能性が広がることは、大きな意義があると思います。また個人的には、自分たちのアイデアが直接形になったことで、非常にやりがいある仕事だと感じました。
疋田 新しいモノをやってみることで、次に新たな挑戦をすることへのハードルが低くなってきます。技術や知見の幅も広まっていくのが大きいところですね。社内外に「あたらしい動き」を起こしていきたいですね。
将来のモビリティのあり方がどうなるかは分かりませんが、NSKが社会課題を解決していくことで、社会から必要とされ、NSKという企業自体の持続可能な成長につなげていきたいです。