NSK Prensa
NSK Europe Ltd.
NSK Desarrolla un husillo a bolas de baja fricción para Máquina Herramienta
NSK ha desarrollado MT-Frix, un husillo a bolas de baja fricción diseñado para aplicaciones de máquinas herramienta.
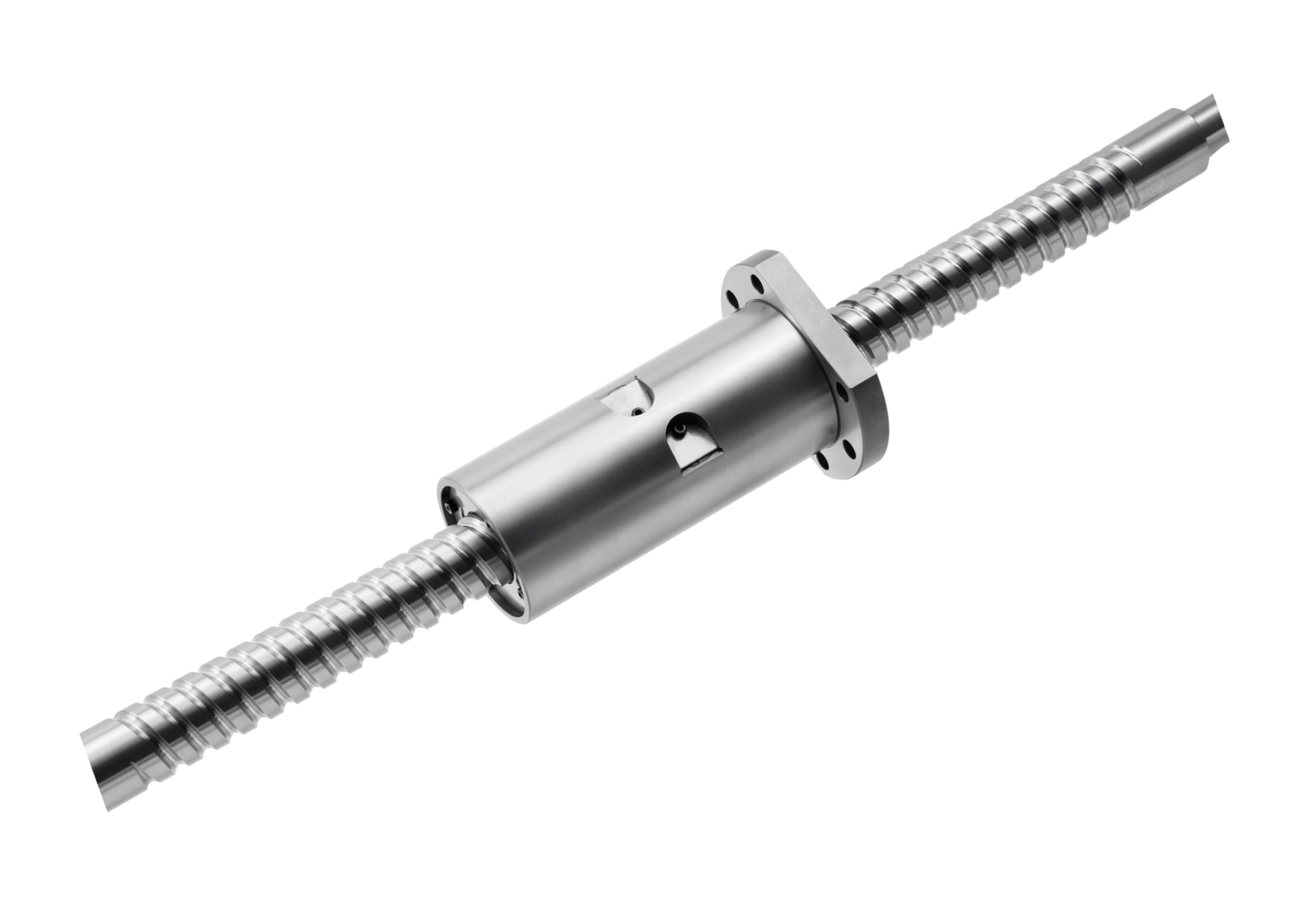
Ya disponible para su compra, el nuevo husillo a bolas ofrece una reducción significativa del par de fricción dinámico, solucionando un importante quebradero de cabeza al que se enfrentan con frecuencia las empresas del sector. Esto se consigue a la vez que se mantiene la rigidez de la tuerca, reduciendo la generación de calor y permitiendo una precisión más sostenible de la máquina herramienta y mayor ahorro de energía.
La reducción del par de fricción fue posible gracias a la tecnología analítica de NSK, que se utilizó para definir las condiciones de contacto entre la bola y el camino de rodadura con el fin de desarrollar unas especificaciones internas óptimas. NSK utilizó entonces esas especificaciones para reducir el par de fricción dinámico manteniendo la rigidez de la tuerca sin alterar las dimensiones del husillo a bolas. Esto, a su vez, permitió una reducción significativa en la generación de calor.
Además, MT Frix también es capaz de mantener una alta precisión de posicionamiento y ofrece una reducción de hasta el 50% en las emisiones de CO2 causadas por el par de fricción dinámico.
Antecedentes y desarrollo
MT Frix representa una solución a varios retos a los que se enfrenta el sector de la Máquina Herramienta. En la industria, los husillos a bolas se encuentran montados en los ejes lineales de las máquinas herramienta y son responsables de posicionar las herramientas de mecanizado y las piezas de trabajo.
En los últimos años, ha crecido la demanda de husillos a bolas que ofrecen una mayor precisión de posicionamiento y ahorro de energía. Un problema que se interpone en el camino es que, cuando se acciona un husillo a bolas, éste genera calor debido al par de fricción dinámico (siendo éste el par causado por la fricción generada cuando un husillo a bolas gira) y el eje del husillo sufre una dilatación térmica, lo que a su vez reduce la precisión de posicionamiento.
Una forma de evitar la pérdida de precisión debida a la generación de calor es la refrigeración forzada (que generalmente implica disipar el calor generado por medio de un dispositivo auxiliar), pero el uso de un dispositivo de este tipo provoca un aumento del consumo de energía. Por lo tanto, para lograr tanto una alta precisión como un ahorro de energía, es necesario reducir el propio par de fricción dinámico.
Sin embargo, con la tecnología convencional, cuando se reduce el par de fricción dinámico, la rigidez (es decir, la resistencia a la deformación debida a una carga externa) también disminuye, por lo que la tuerca del husillo a bolas es más propensa a experimentar desplazamientos. Esto, a su vez, puede provocar una reducción de la precisión del mecanizado. Por todo esto, NSK quiso encontrar una forma de reducir el par de fricción dinámico sin perder rigidez.
Aquí es donde intervino la tecnología analítica de la empresa. Se utilizó para clarificar las condiciones de contacto entre la bola y el camino de rodadura, lo que permitió desarrollar unas especificaciones internas óptimas. Como resultado directo, se redujo el par de fricción dinámico sin afectar a la rigidez de la tuerca ni a las dimensiones del husillo a bolas.
Características y ventajas
En conclusión, MT Frix ofrece una serie de características y ventajas impresionantes. En comparación con las alternativas convencionales, ofrece una reducción significativa tanto del par de fricción dinámico (hasta un 50%) como de la generación de calor (hasta un 40%) sin ningún cambio en la rigidez de la tuerca.
También ofrece una alta precisión de posicionamiento sostenida porque, como resultado directo de la reducción de la generación de calor, la cantidad de elongación axial se reduce hasta en un 40% en comparación con los productos convencionales, lo que minimiza el deterioro de la precisión de posicionamiento.
Por último, permite un importante ahorro energético. De hecho, en comparación con las alternativas convencionales, las emisiones de CO2 causadas por el par de fricción dinámico se han reducido hasta en un 50%.
Compartir