Keine Lagerschäden mehr in Hochtemperatur-Betonverdichteranwendungen
Bei einem polnischen Pflastersteinhersteller kam es wiederholt zu Betriebsstörungen durch Lagerausfälle in einem Rüttler zum Verdichten. Innerhalb von nur vier Monaten fielen die Wälzlager in einem Elektromotor insgesamt zehnmal aus. Jedes Mal kam es zu einer Ausfallzeit von mindestens zwei Stunden für den Austausch.
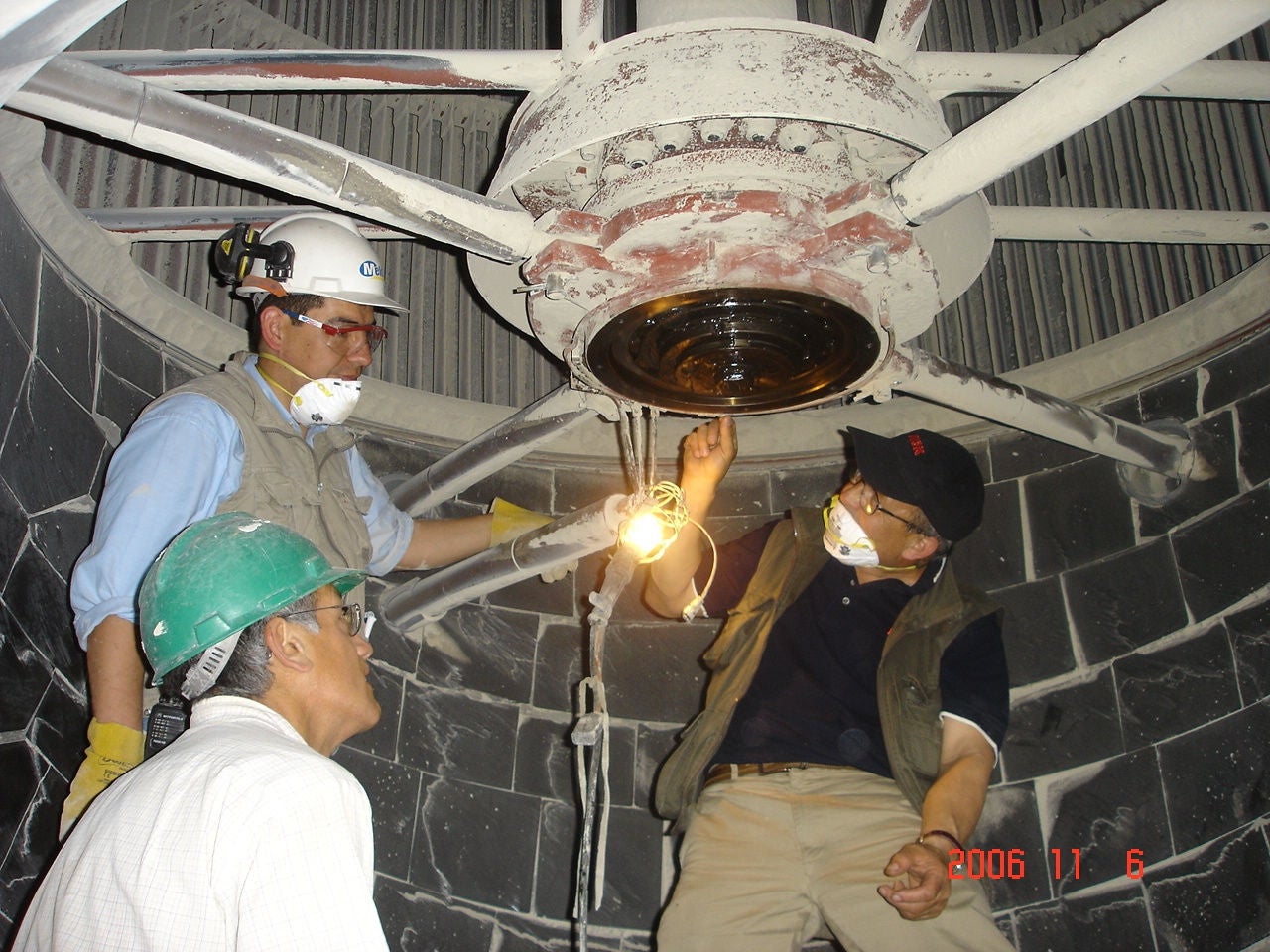
Wir haben ihnen 32.100€ gespart
Das Unternehmen bat NSK um Hilfe. Unser Team hochqualifizierter Ingenieure führte eine gründliche Anwendungsprüfung durch. Dabei stellte sich heraus, dass die vorhandenen gedeckelten Rillenkugellager in einer Umgebung, in der die Betriebstemperaturen regelmäßig 110 °C überstiegen, den hohen Temperaturen und starken Erschütterungen nicht standhalten konnten. Konkret fand man als Hauptursache Fettleckagen und Überhitzung, die direkt zu den Ausfällen führten.
„Diese Erfolgsgeschichte zeigt die herausragende Zuverlässigkeit der maßgeschneiderten Hochtemperaturlagertechnologie von NSK in rauen, vibrationsintensiven Umgebungen“
Anton Mozhaev, Branchenmanager Zement bei NSK Europe
NSK riet dem Unternehmen zum Einsatz einer robusteren Lösung und empfahl Rillenkugellager mit hochtemperaturbeständigen schleifenden Dichtungen aus Fluorkautschuk, speziell ausgewählten hitzestabilisierten Stahlringen und einem C3-Lagerspiel, um der Wärmeausdehnung und der dynamischen Belastung Rechnung zu tragen. Mit diesen Verbesserungen wollte man den Fettaustritt verhindern (oder zumindest drastisch reduzieren), optimale Innentemperaturen aufrechterhalten und die Lagerlebensdauer selbst unter diesen anspruchsvollen Bedingungen verlängern.
Das Unternehmen stimmte einem Test der Lösung zu. Vier Monate lang (die Zeitspanne, in der zuvor die regelmäßigen Ausfälle auftraten) arbeitete das Unternehmen ohne Lagerausfälle und ohne jegliche Wartungseingriffe.
Möchten Sie mehr darüber erfahren, wie NSK Ihre Kosten und Ausfallzeiten reduzieren kann?
Bitte klicken Sie auf die Schaltfläche unten und wir werden Sie mit einem Vertriebsmitarbeiter in Verbindung setzen, der Ihnen helfen wird, die richtige Lösung zum richtigen Preis zu finden.
„Diese Erfolgsgeschichte zeigt die herausragende Zuverlässigkeit der maßgeschneiderten Hochtemperaturlagertechnologie von NSK in rauen, vibrationsintensiven Umgebungen“, so Anton Mozhaev, Branchenmanager Zement bei NSK Europe. Durch unser Verständnis der spezifischen Anwendungsanforderungen und die Entwicklung einer zielgerichteten Lösung konnten wir dem Kunden langfristige Stabilität, Effizienz und erhebliche Kostensenkungen ermöglichen.“
Durch die Umstellung auf die Hochtemperaturlösung konnte der Kunde ungeplante Wartungsarbeiten und damit verbundene Ausfallzeiten vollständig vermeiden; ein Austausch der Komponenten war innerhalb der vier Monate zu keiner Zeit erforderlich (statt wie vorher ganze zehn Mal). Diese Verbesserungen führten nicht nur zu einer erhöhten Betriebssicherheit, sondern auch zu Kosteneinsparungen von insgesamt 32.100 €.
Teilen