Setting the Future in Motion with New Ball Screw Units for Advanced Braking Systems: Part 2 (Product Design)
NSK started mass producing ball screw units for electric hydraulic brake systems at Saitama Plant in March 2018 and at Akagi Plant (NSK Steering Systems) in January 2020. This three-part series will feature the perspectives of the people who created this product. For this article, we talk to one of the key engineers who worked on the product to share his thoughts about the design process.
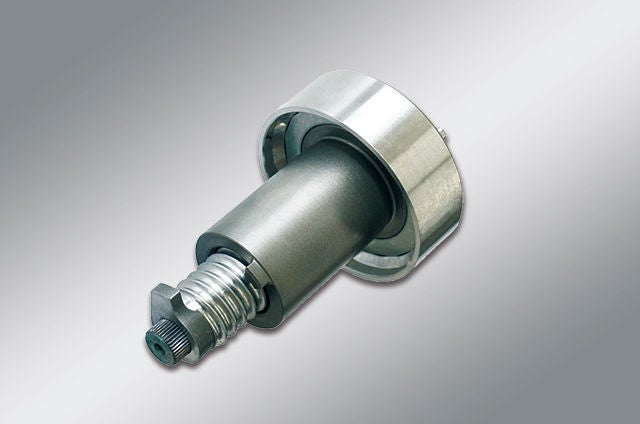
Ball screw unit for electric hydraulic brake systems
Did you miss Part 1 and Part 2? Read them here.
Profile
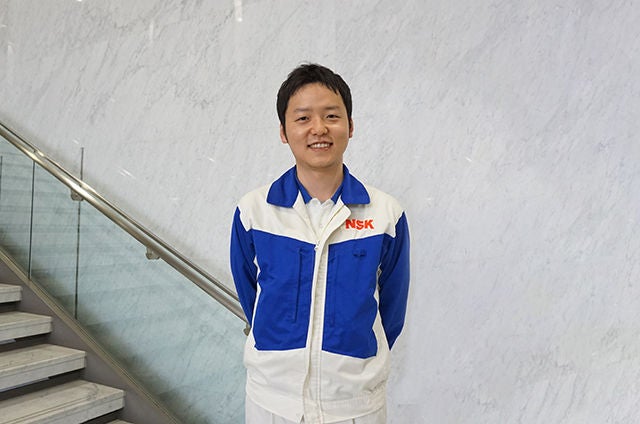
Masato Nakajima
Coordinator
Actuator Technology Department
Steering & Actuator Technology Center
Automotive Business Division HQ
Meeting the Growing Need for Electric Brakes
Ball screw units are found in automotive brake boosters for electric hydraulic brake systems. The booster is used to reduce the amount of force that the driver needs to apply to the brake pedal in order to stop the vehicle. Vacuum boosters have been the main design for this component, traditionally, and they use the suction of negative pressure created by the engine to enhance brake pedal pressure. However, by using a ball screw and an electric motor, the brakes can be applied even before the driver steps on the pedal.
The move to make brake boosters electric began with the growing demand for electric and hybrid vehicles (EVs and HEVs). Since these vehicles feature smaller gas engines or no engines at all, there is insufficient or no suction pressure that can be used for braking. This led to growing demand for electric boosters. In recent years, the heightened need for greater vehicle safety has also increased demand for electric boosters. Starting in November 2021, all new vehicles in Japan will be required to have autonomous emergency braking systems. Accordingly, we expect the demand for ball-screw-type electric hydraulic brake systems to increase as automakers strive to meet the higher safety standards.
Making the Most of All of Our Knowledge
There are several kinds of electric brake boosters, including the slide screw type, but the ball screw type is the most promising. One reason is the outstanding responsiveness it provides. Since there are tiny balls between the screw and the nut, the ball screw delivers very smooth motion. This allows the electric brake motor to activate instantly, resulting in exceptional responsiveness. Going forward, the market for electric brakes will have even higher requirements of electric brakes, and they will have to work effectively even in larger vehicles like pickups. The ball-screw-type system is considered optimal for larger vehicles as well, thanks to its superior responsiveness, which enables rapid, powerful braking.
In developing our ball screw unit, we put particular emphasis on reducing size and weight. NSK has been working on developing these ball screws for 10 years, leveraging feedback from various customers. During this process, the focus has always been on how to reduce the number of components while maintaining the same quality. Parts that are smaller and lighter are easier for customers to incorporate into their products. Thanks to the knowledge we amassed in this process, NSK's latest ball screw unit features an integrated ball screw support structural components, as well as an integrated support bearing. This makes the unit smaller and lighter than ever.
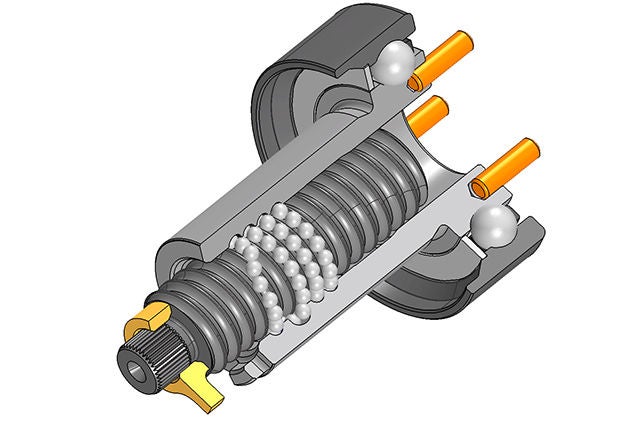
3D model of NSK's ball screw unit for electric-hydraulic brake systems
Focusing on Customer Satisfaction
Since this kind of project was a first for NSK, we explained its necessity to each department involved. This enabled us to move toward mass production with a shared understanding. While holding a total of around 100 weekly meetings with customers, we employed a process of trial and error to ensure that customer needs were met for size and cost.
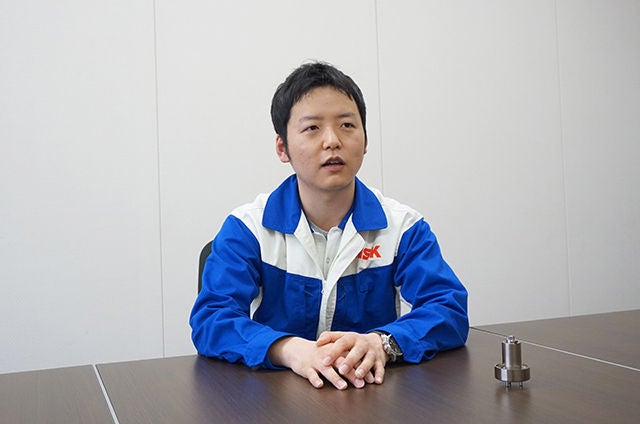
Shouji Going forward, we believe it will be essential to take on the challenge of creating new products in line with dramatic changes in the social environment, values and needs. I hope to utilize this experience of giving shape to a new product to help set the future in motion. We are also working on employee development with the aim of rolling out new products on a global scale.