Setting the Future in Motion with New Ball Screw Units for Advanced Braking Systems: Part 1 (Strategy)
NSK started mass producing ball screw units for electric hydraulic brake systems at Saitama Plant in March 2018 and at Akagi Plant (NSK Steering Systems) in January 2020. This three-part series will feature the perspectives of the people who created this product. For this first article, we talked with two key individuals at the Automotive Business Division HQ about the significance of NSK's work in bringing this ball screw unit to market. The pair was in charge of directing the project and coordinating all departments involved.
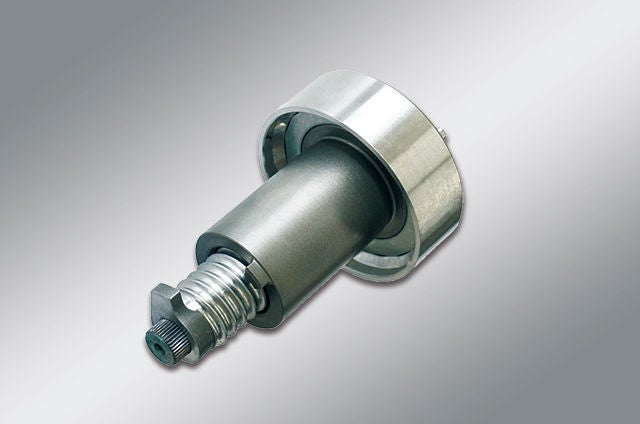
Ball screw unit for electric hydraulic brake systems
Profile
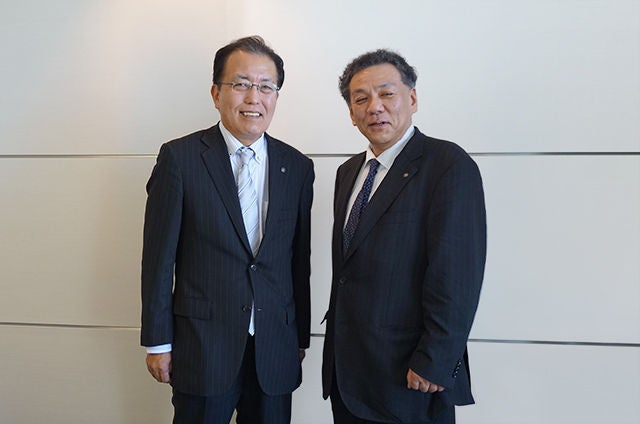
Hiroyuki Ikeda (left)
Senior Manager
Automotive New Business Development Office
Automotive Business Division HQ
Hidenori Kuwata (right)
Senior Specialist
Automotive Steering & Actuator Division HQ
Automotive Business Division HQ
Upfront Investment in an Essential Component for Electric Brake Boosters
Hiroyuki The NSK Saitama Plant has been making ball screw units for automotive regenerative braking systems since 2011. Anticipating growing demand for electric braking systems, we launched a project in 2014 to develop products to meet the demand for full-scale adoption of electric brake boosters.
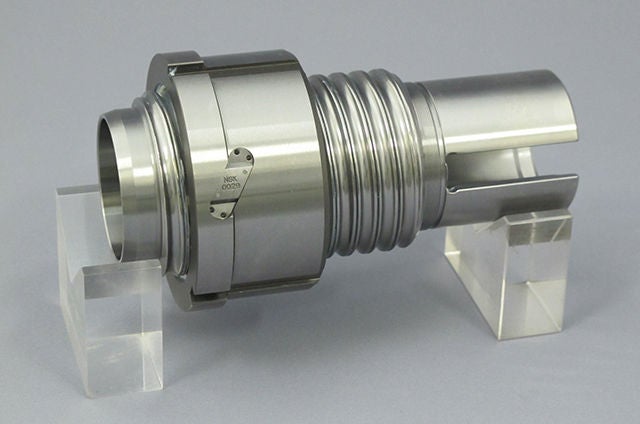
NSK developed the friction ball screw for regenerative braking systems in 2011
Hidenori I was transferred to this department in 2015. As I researched the electric brake market, I soon saw the promise of ball-screw-type electric brake boosters. The ball screw changes the rotating motion of the motor into a linear motion. This change in movement can be achieved with other devices such as a slide screw, but the type using a ball screw offers outstanding responsiveness due to its smooth movement. Responsiveness is vital to maximizing safety in braking systems, especially in autonomous driving to ensure optimal control. Once we ascertained the advantages of the ball screw in terms of responsiveness, ease of installation, and quiet (low-noise) performance, we moved forward with the project.
Hiroyuki Before we even received any orders for the product, we had already established the key production facility, manufacturing method, and a prototype processing line. Thanks to the company's decision to provide this kind of upfront investment, we were able to design the product from a new perspective and develop a unique mass production method. Our efforts over the development years resulted in a system capable of making products at a competitive price point, which ultimately leads to more orders and greater scale.
Hidenori Looking back, I think we were fortunate to receive the company's support in the form of that upfront investment. It allowed us to work on the project with a sense of urgency. We share in NSK's passion to take on new challenges, and this helped motivate all the departments involved to work together to make the project a success.
Autonomous Emergency Braking Systems Becoming Mandatory in Near Future
Hidenori There is a global trend toward requiring installation of autonomous emergency braking systems to prevent collisions and save lives. In fact, these systems will be mandatory for new vehicles sold in Japan in from November 2021 onward. There is always a need for improved vehicle safety, and we expect that ball-screw-type braking systems will be the dominant product in the market by 2023 or 2024. This is based on current pace of orders and the importance our customers are placing on the outstanding responsiveness achieved by ball-screw-type systems. This allows the time between obstacle detection and brake application to be as short as possible.
NSK - We're Setting the Future in Motion
Hiroyuki With the advancing penetration of CASE* technologies in the auto industry, awareness of these new products is increasing throughout NSK. It is, of course, no easy task to make new products a success. With the first prototype we had for this product, it would have taken an unrealistic amount of time to produce a single unit, limiting the maximum efficiency achievable at scale. However, the team worked tirelessly to resolve the issues one by one and made steady progress. I hope this initiative will become a great example of successful upfront investment for the company, thereby having a beneficial impact on other products under development. Going forward, I will keep looking for other products with great potential and work to create products that can deliver on NSK's commitment to "setting the future in motion" and drive the company's future success.
*CASE: Connected (digital network), Autonomous, Shared/Services and Electric.
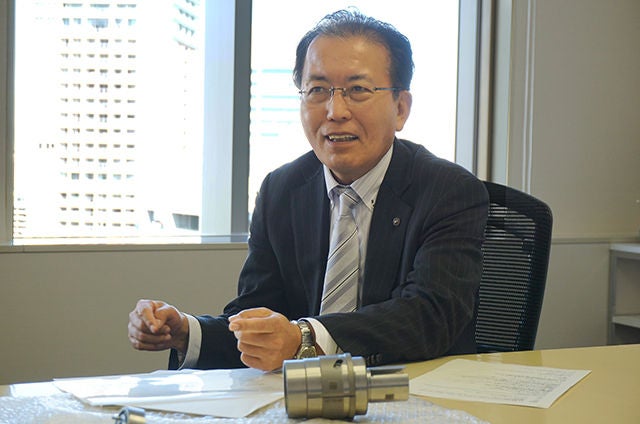
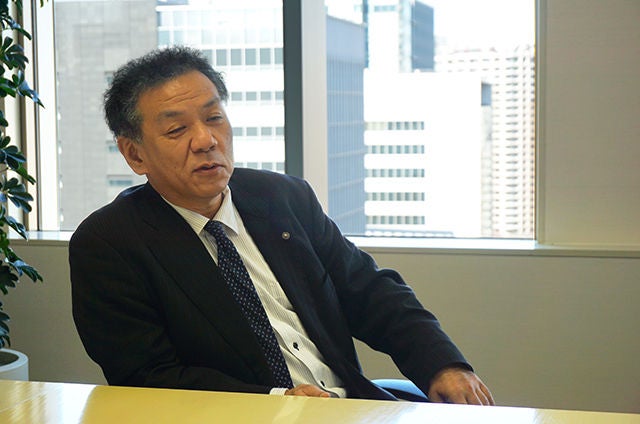
Hidenori I have realized how important it is for us to keep an eye on global market trends, including regulations, while looking for new things that are really needed by customers and society. Although the product took a long time to create, I think its success with customers is a result of our conviction and hard work. I want to continue working with customers to make products that benefit society. My personal mission is to explain to customers the significance of what our technology and production departments have created and the many benefits it delivers to the customer and the end user.