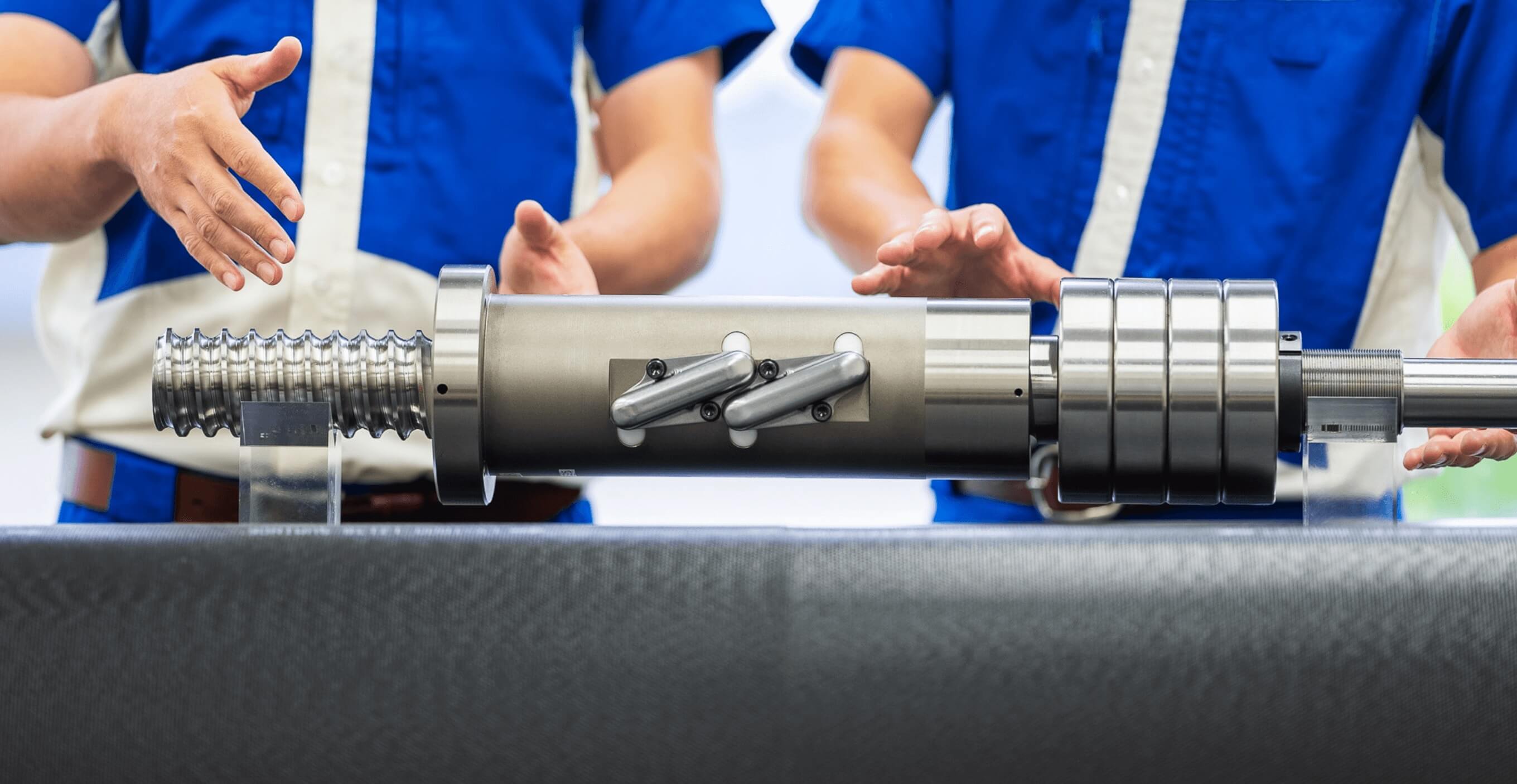
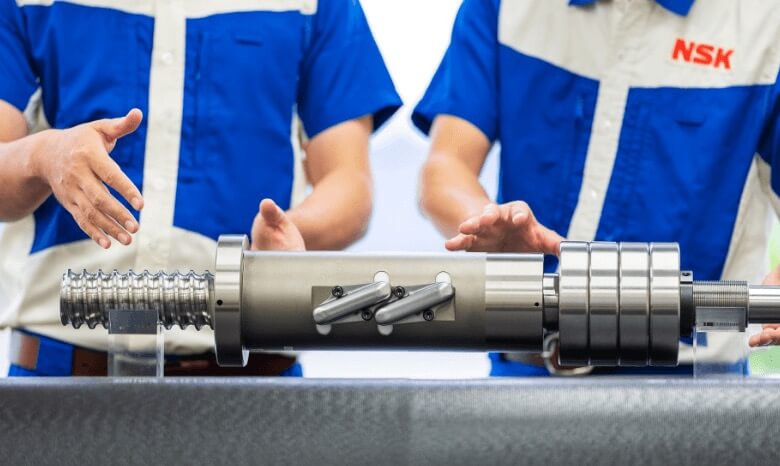
Episode 01
時を超え形に。理想の形状を生み出すNSKの技術力
高負荷駆動用ボールねじ向け長寿命化技術
プロジェクトメンバー
-
ボールねじ技術部リーダー Dさん新卒入社大学を卒業後、NSKのグループ会社に入社し、技術営業職に従事。その後NSKに転籍し、技術部にてボールねじの設計・開発に携わる。現在は、ボールねじの生産工場に設計として駐在し、工場の改善活動や設計品質の向上に取り組む。本プロジェクトでは、開発計画の作成や変化点・変更点における想定不具合の解析、評価方法や評価基準の策定などを行い、プロジェクトリーダー的な役割を果たす。
-
ボールねじ技術部シミュレーション Rさんキャリア入社2019年にキャリア採用で入社。前職は、半導体関連装置の開発・販売を行う企業に勤務。新商品開発部にて機構設計に携わる。その後NSKに入社し、技術部でボールねじの収益改善プロジェクトに参画。現在は、力の伝達を特徴とする大型や高負荷のボールねじの新商品開発に取り組む。本プロジェクトでは、試験機の準備や開発品の耐久試験、信頼性確認などを行った。
-
生産技術センター 設備開発部生産設備開発 Jさん新卒入社NSK入社後、生産技術センター設備開発部に配属。ボールねじや軸受の「機上計測」による作業支援機能開発や高度化技術開発などに携わる。現在は、設備内部の測定器で加工物を計測し、結果を加工に生かすことで生産性向上や製品に新たな価値を付加する技術の開発を担当している。本プロジェクトにおいては、専用機の開発、専用プログラムの作成、加工データと測定データの整合性検証などを行った。
電動射出成形機の機能向上と省エネを目指し
ボールねじの長寿命化技術開発に着手
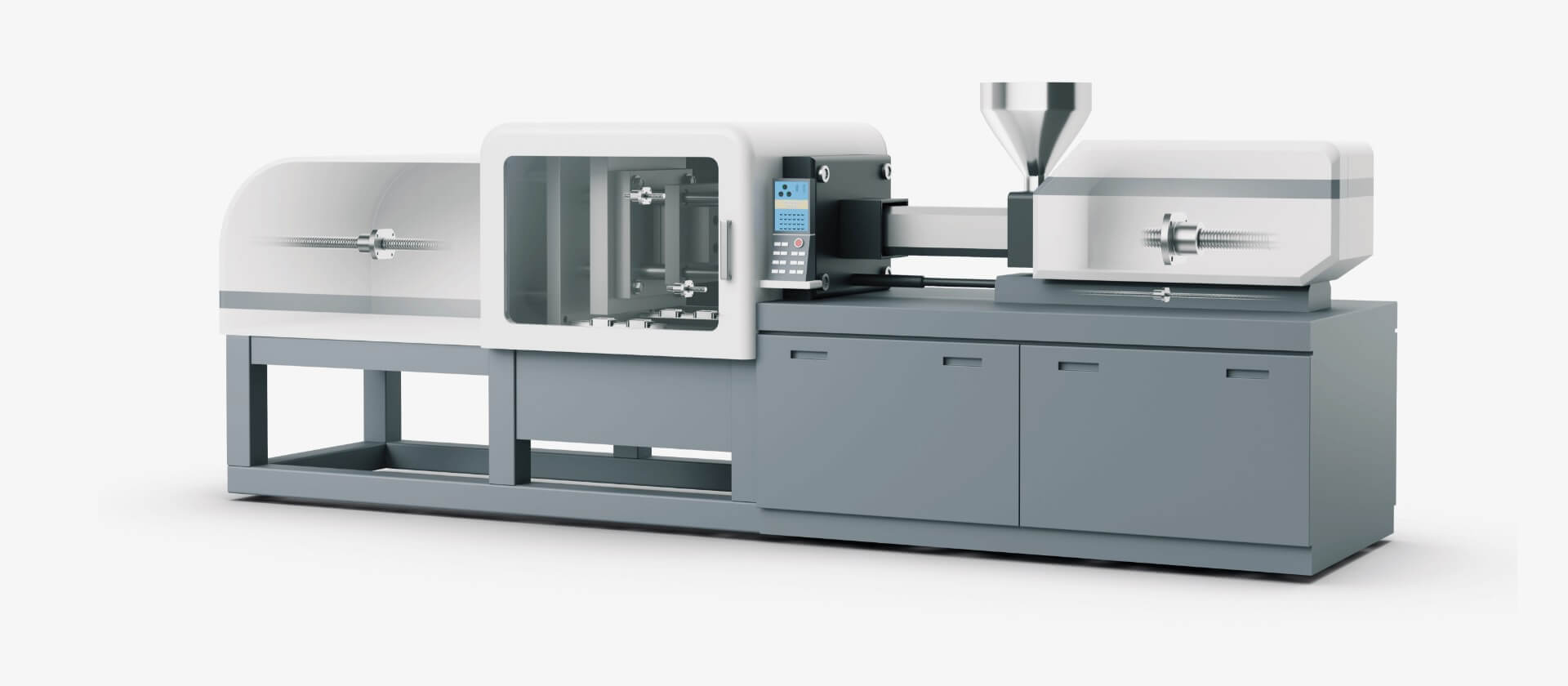
SDGsやカーボンニュートラルへの取り組みが進む中、産業機器もさらなる環境への配慮や機能向上が求められています。
射出成形機においては、駆動方式が省エネの観点より、油圧式からボールねじを使用した電動式へ切り替わりが進んでいます。また、自動車のEV化により、車体の軽量化を目的に樹脂部品の採用が拡大。形状の複雑化や大型化が進んでいるため、電動射出成形機の生産性向上が求められています。さらに、電動射出成形機の生産性向上の一つとして送り速度(熱で溶かした樹脂材料を押し出す速度)の高速化も進み、ボールねじの単位時間あたりの走行距離も伸びているため、ボールねじを長寿命化する必要性が出てきています。
NSKでは、これらの理由からボールねじの長寿命化技術の開発に着手。本技術を開発することで、お客様の困り事を手助けできればと考えました。
開発年表
Timeline
-
2021年1~3月
市場分析・ターゲット設定など
競合他社で同様の技術がまだ開発されていないことや、市場のニーズ・動向などを調査。本技術が開発されることで顧客が得られるメリットなどを検討した結果、ボールねじの長寿命化技術の開発を進めることが決定した。
-
2021年9月
試作品の耐久試験開始
開発スタートから5カ月程度で、一次試作品が完成。試験装置を準備し、シミュレーション通りの耐久性を有しているか、耐久試験を開始した。
-
2022年1月
耐久試験結果の検証
耐久試験が目標に到達した。さらにボールねじを稼働させることでシミュレーション以上の耐久性があることを確認した。
-
2022年3月
新聞発表
当初の計画通り、各メディアに対して本技術について発表した。
-
2021年4月
開発スタート
DR(デザインレビュー)※1を進めるべく、開発企画・開発計画・DRメンバーを策定。いち早くこの技術を世に送り出すために、2022年3月のメディア発表を目標とし、プロジェクトをスタートした。
-
2021年12月
1次試作品を用いて加工機の評価実施
専用加工機にてシミュレーション通りの加工が行うことができたかの検証を行った結果、一部、適用範囲を見直しが必要と判断。修正を行う。
-
2022年2月
2次試作品を用いて加工機の評価実施
1次試作の評価結果を踏まえて2次試作を製作。専用加工機と測定技術が目標レベルに到達したことを確認した。
※1製品開発プロセスの節目で、設計開発活動を担当する人だけでなく複数人で設計書や図面などの成果物を評価し、設計開発活動をこのまま進めて、品質・納期・コストなどの設計開発の条件を満たす設計開発活動の結果を出すことができるかどうかを判断する活動のこと。
-
2021年1~3月
市場分析・ターゲット設定など
競合他社で同様の技術がまだ開発されていないことや、市場のニーズ・動向などを調査。本技術が開発されることで顧客が得られるメリットなどを検討した結果、ボールねじの長寿命化技術の開発を進めることが決定した。
-
2021年4月
開発スタート
DR(デザインレビュー)※1を進めるべく、開発企画・開発計画・DRメンバーを策定。いち早くこの技術を世に送り出すために、2022年3月のメディア発表を目標とし、プロジェクトをスタートした。
※1製品開発プロセスの節目で、設計開発活動を担当する人だけでなく複数人で設計書や図面などの成果物を評価し、設計開発活動をこのまま進めて、品質・納期・コストなどの設計開発の条件を満たす設計開発活動の結果を出すことができるかどうかを判断する活動のこと。
-
2021年9月
試作品の耐久試験開始
開発スタートから5カ月程度で、一次試作品が完成。試験装置を準備し、シミュレーション通りの耐久性を有しているか、耐久試験を開始した。
-
2021年12月
1次試作品を用いて加工機の評価実施
専用加工機にてシミュレーション通りの加工が行うことができたかの検証を行った結果、一部、適用範囲を見直しが必要と判断。修正を行う。
-
2022年1月
耐久試験結果の検証
耐久試験が目標に到達した。さらにボールねじを稼働させることでシミュレーション以上の耐久性があることを確認した。
-
2022年2月
2次試作品を用いて加工機の評価実施
1次試作の評価結果を踏まえて2次試作を製作。専用加工機と測定技術が目標レベルに到達したことを確認した。
-
2022年3月
新聞発表
当初の計画通り、各メディアに対して本技術について発表した。
それぞれの専門家が
力を結集して問題を解決
ボールねじの長寿命化技術は、どのようなものでしょうか?
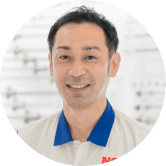
ボールねじは、各回路に充填されたボール一つひとつが荷重を受けています。しかし、荷重が大きくなると、バランスが不均一になって特定の回路に負荷がかかり、ボールねじの寿命が短くなってしまいます。ですから、各回路がバランス良く荷重を受けられれば、寿命を伸ばせるのではと考えました。
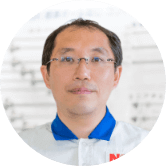
モノを作る時には必ず誤差が出ます。だから、本来、ボールねじは軌道面の螺旋が綺麗な丸を描いていることが理想ですが、なかなかそうはなりません。そのことが特定の回路に負荷がかかる原因になっていました。
今回、設計から提案されたのは、逆にそういったものを好きな形にコントロールすることで、荷重をうまく逃す方法でした。そこで、理想の形状にコントロールできる加工機を作ることでボールねじの長寿命化を実現しました。
今回の開発で、一番ポイントとなった部分を教えてください。
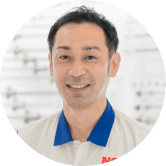
やはりJさんたちの加工技術・測定する技術ですね。私たち設計が考えることを形にできる加工・切削の技術がないと、実現できませんから。
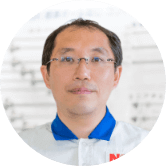
実は、今回開発した技術のベースは、7年前に作業効率の向上を目的に開発した機能だったんです。当時は必要なかったのですが、「これを応用すれば生産技術を進化できる」と可能性を感じていました。このプロジェクトが稼働する前に、当時一緒に仕事していた方から「新しい商品の構想に、あの技術が使えないだろうか」と問い合わせがあって。当時の技術を応用すれば問題解決できると考え、今回開発した技術を提案しました。
当時感じていた可能性が、7年の月日を経て、他のメンバーの技術提案も加わって想像を超えた形で進化した。これは、非常に面白い経験でした。
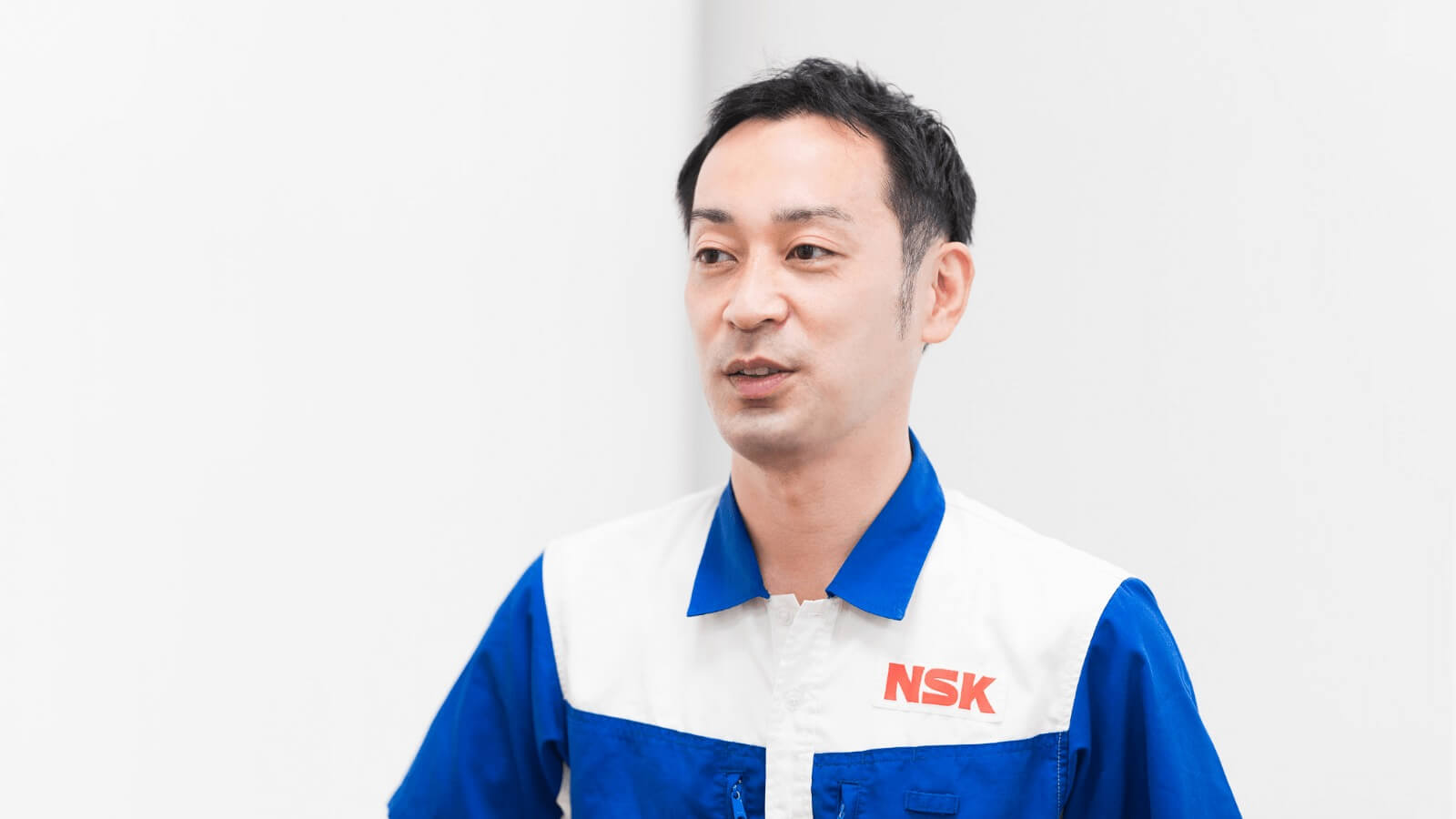
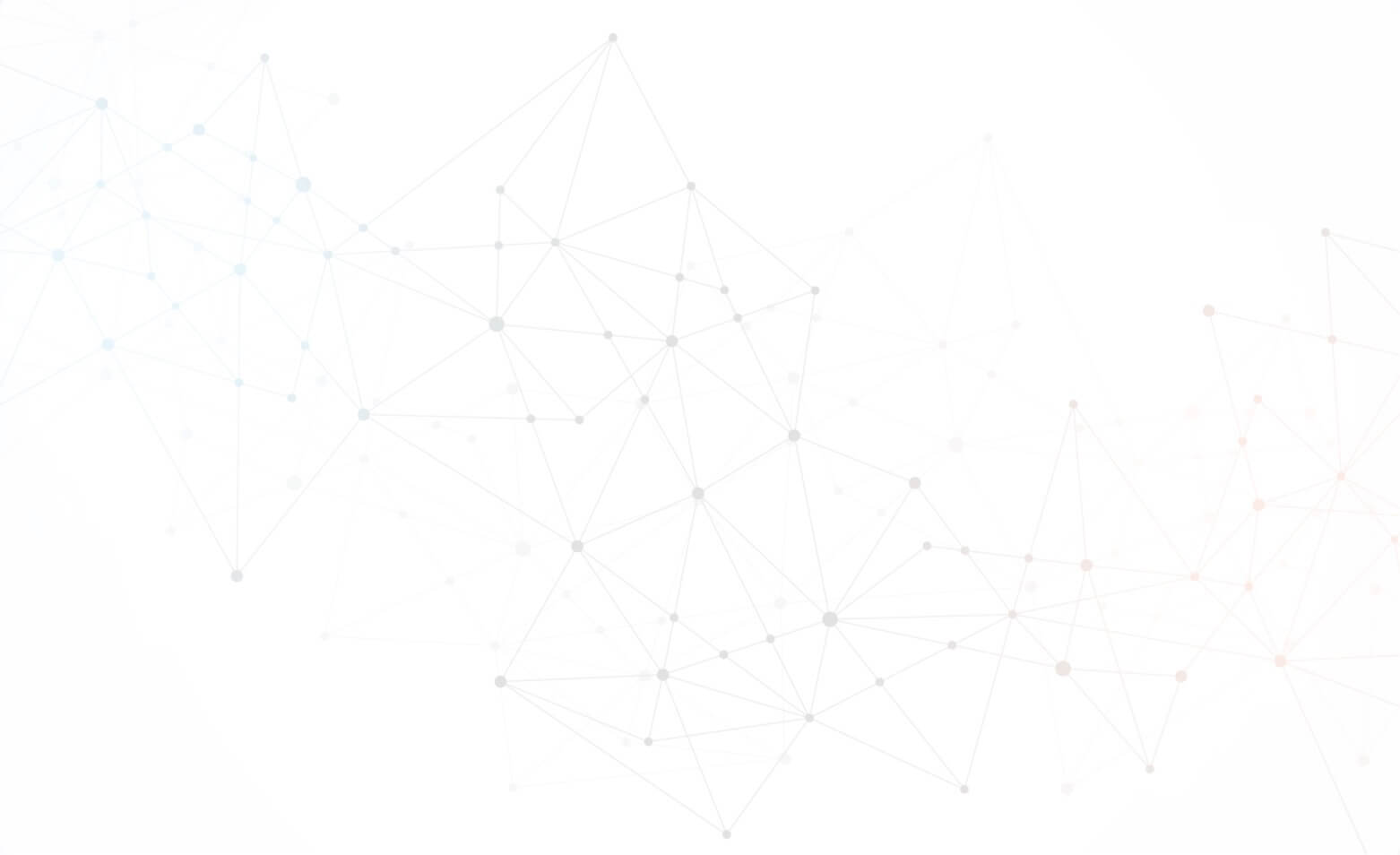
今回の開発において、特に活用した技術はありますか?
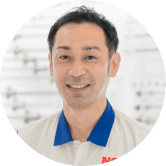
リアルデジタルツイン※2です。設計の段階では、長寿命化につながると想定した形をシミュレーションしていきました。
※2現象の内部を詳細に観察し、そのカラクリの推理、モデル化を通じ本質を理解することで、既成概念を打ち破るソリューションを発想するNSK独自の開発手法。
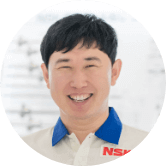
評価では、リアルデジタルツインで実際のお客様の使用条件をもとに負荷を掛けて、テストしました。今回は、高負荷に耐えられて、かつ寿命が長いボールねじを作らなければならなかったので、今までにはない開発解析が必要でした。
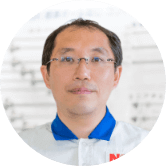
考えている加工技術だと、設備の中でどんな現象が起きるかをリアルデジタルツインで解析しました。近年NSKでは、効率化を考えてリアルデジタルツインにかなり投資をしており、社内にノウハウの蓄積も増えています。そのおかげで解析できる幅も広がって、今回だと髪の毛の100分の1程度とかなり細かいシミュレーションもできました。このことが測定技術の開発にもつながっていると思います。
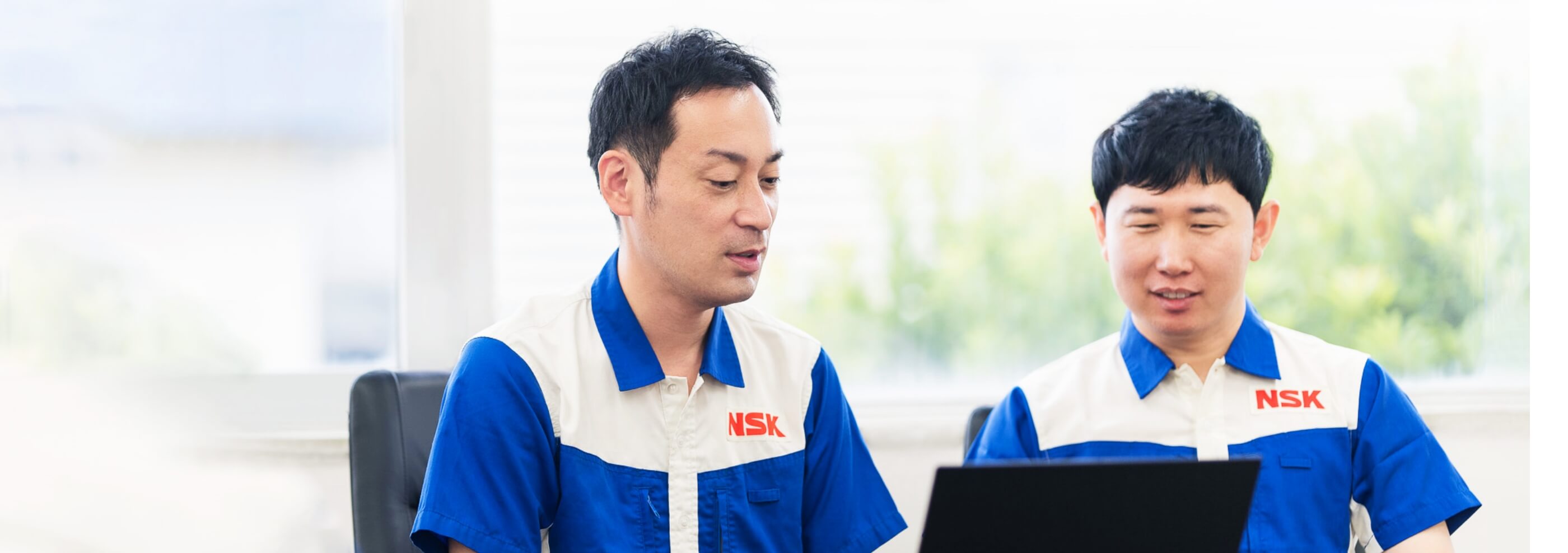
開発中、特に大変だったことがあれば教えてください。
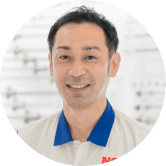
非常に短期間で開発を進めていたので、私は最初に課題をすべて洗い出して、タイムリーに進めていくのが大変でしたね。
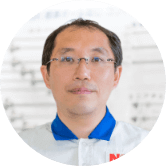
今回の技術に対応している設備は、九州の工場にしかなかったんです。でも、コロナ禍で出張の回数がかなり制限されていて……。少ない検証回数で結果を出さなければならないのがプレッシャーでした。事前の検討や解析を入念に行って、かなり確度を上げてから工場で検証を進めました。
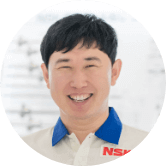
評価に関しては、実験機で評価をする際の条件設定がかなり難しかったです。お客様の実機の条件を上回るような過酷な条件……高い荷重と温度などをどのように作り出すか、かなり苦労しました。私たちが甘い条件で実験するわけにはいきませんから。
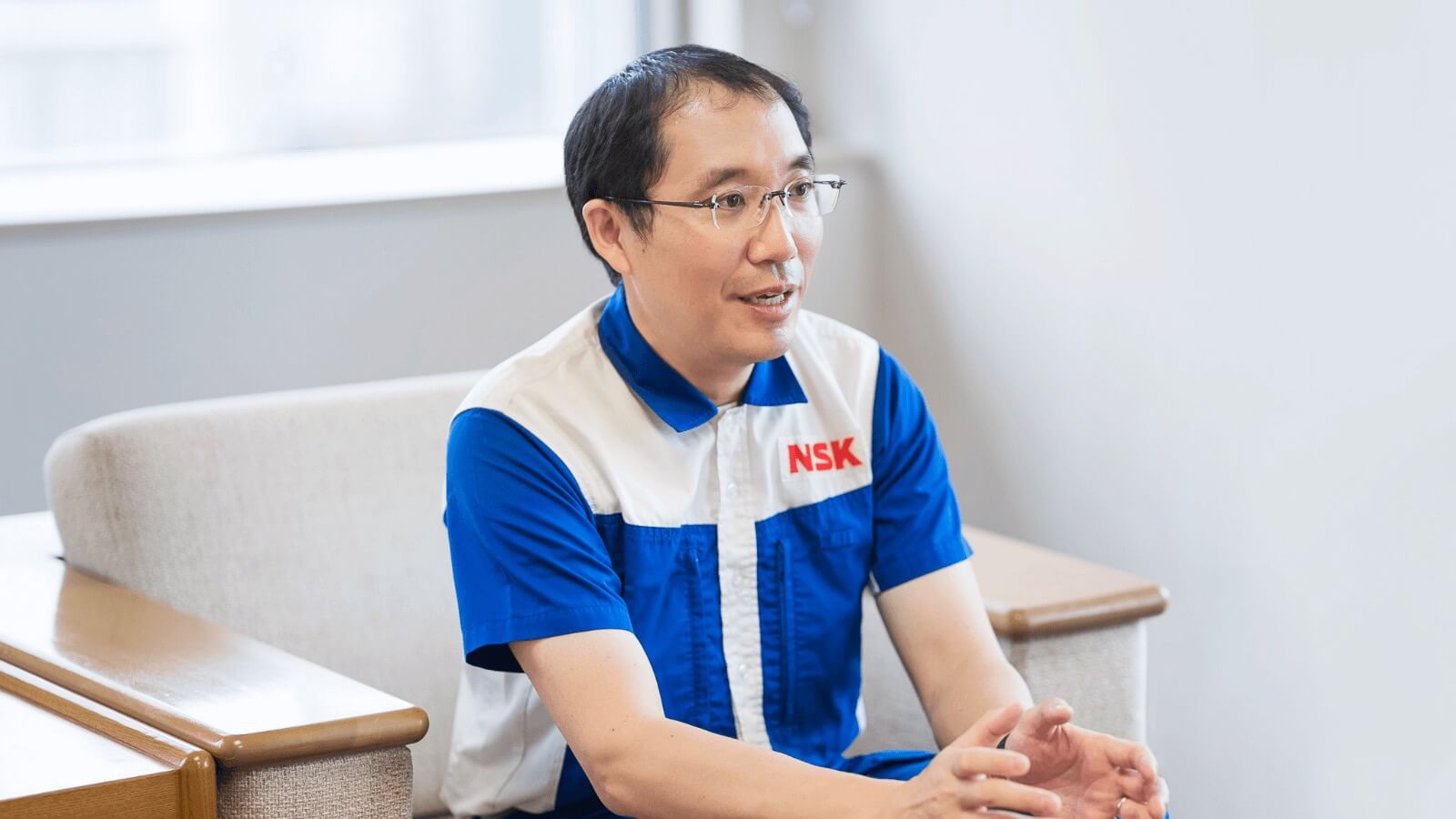

NSKは部署をまたいでの開発が特徴とのことですが、どんな良さがありますか?
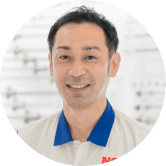
多岐にわたる部署との開発は初めてでしたが、非常に刺激的でした。私はずっと設計業務に携わっていたので、加工機や測定器に関しては勉強不足なところがあって。でも今回、Jさんの知見や実機に触れることができて、新しい知識を得られたのはとても良かったです。それに、メンバーと話す中で、さまざまなアイデアが多方面から出てくるのもワクワクしましたね。
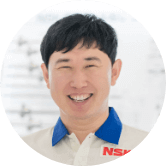
NSKでは、プロジェクトの立ち上げ段階から必ず、機能横断的チームを形成します。設計や開発、製造、設備、マーケティングなど、製品に関わるあらゆる部署の人が集まることで、製品が市場にマッチするかという視点も全員で意識することができます。社内のリソースを最大限発揮できるので、組織全体で一体感も生まれていると思います。おかげで今回も、非常に効率よく開発ができたのではないでしょうか。
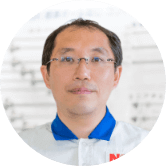
私は普段、工場と従来品の改善を行うことが多く、問題解決に向けたアイデアは持っていても、それをどのように生かせば新商品につながるかがわかりません。でも、設計開発の方々と一緒に取り組むことで、それを現実化していけるのはすごく楽しい経験でした。専門分野を追求している人同士だからこそ出てくる考えでもあるので、非常にいい仕組みだと感じています。
次々に挑戦していく姿勢はどのようなところから生まれていると思いますか?
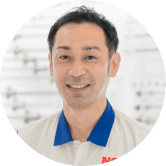
NSKには、前向きな方が多いように感じています。社風としてもいろんなことにチャレンジしていいよ、という土壌があるのではないでしょうか。
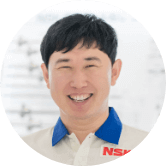
今回の製品は、海外のメーカーもターゲットです。私自身、海外出身ということもあり、世界中の地域や国に対してもNSKの製品を広げていけたらいいなと思っています。その気持ちがチャレンジにつながっていますね。
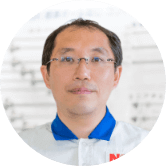
NSKの製品は目立ちませんが、いろいろなものに使われていて、自分が担当している設備が作り出したものが世の中にあふれています。それがないとモノは動かないし、それらが環境を良くすることにもつながっている。私たちの頑張りが、世の中を下支えしている、未来を良くすることにつながっているところがモチベーションになっています。