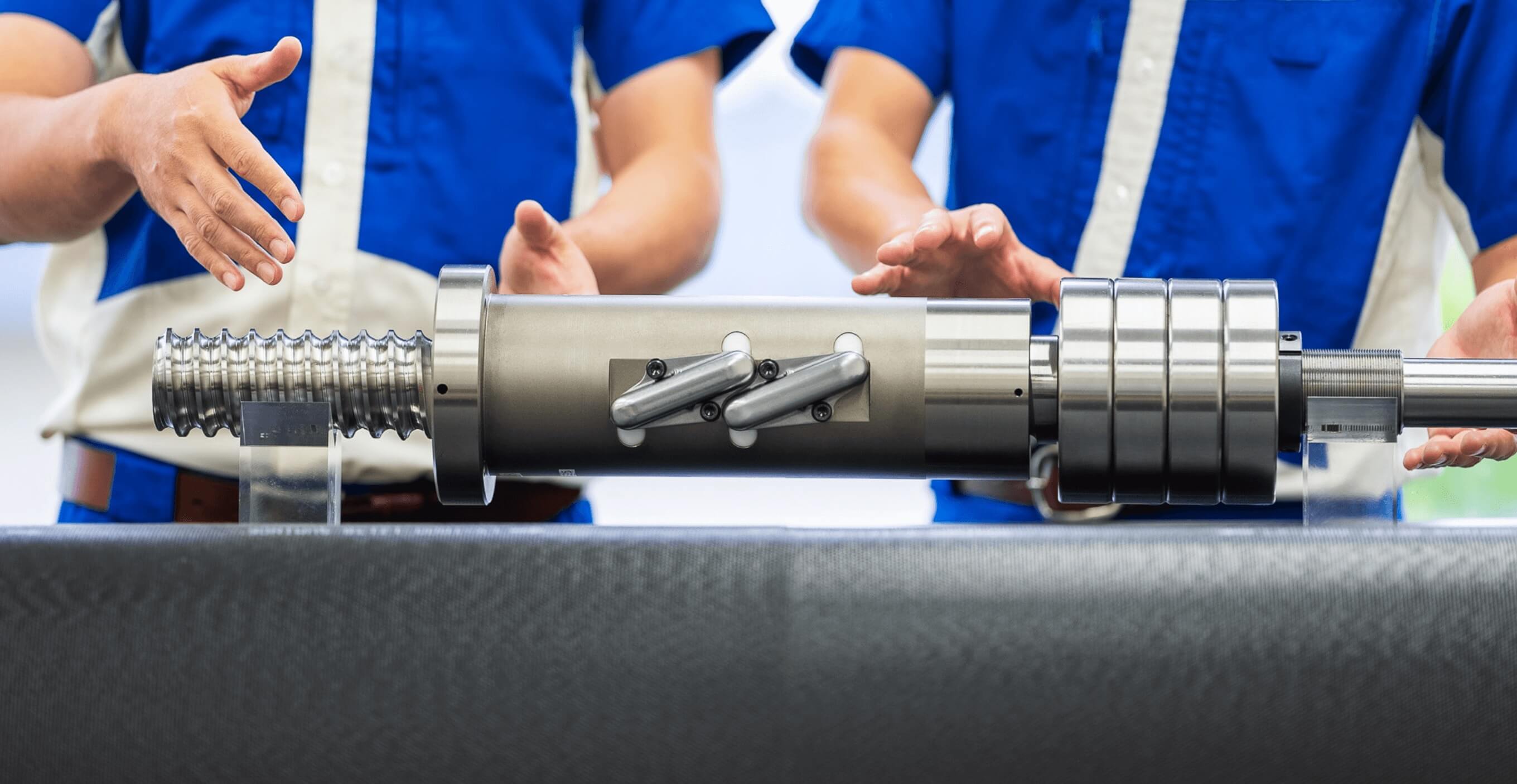
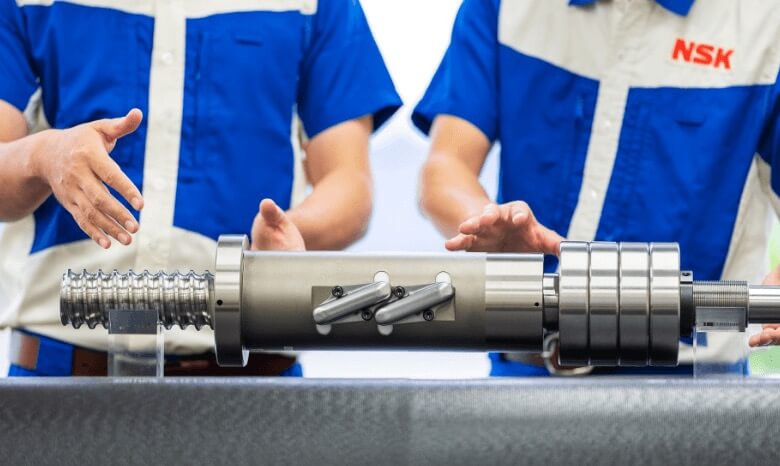
Episode 01
Giving shape to idea years in the making
—How NSK's expertise
creates optimized solutions
Long-life technology for high-load drive ball screws
—How NSK's expertise creates optimized solutions
Meet the Team
-
BS Technology Department
Ball Screw Designer, based at NSK KyushuDaisuke, Team LeaderNew graduate hireAfter graduating from university, Daisuke joined an NSK group company where he worked in sales engineering. He then transferred to NSK Ltd., where he was responsible for designing and developing ball screws in the company's technology divisions. Currently, he is on assignment as a designer at a ball screw manufacturing plant, where he works to improve processes at the plant and enhance design quality. During this project, he served as project leader and created development plans, analyzed assumed defects at change/modification points, and developed evaluation methods and criteria. -
BS Technology Department
Ball Screw Designer, based at NSK KyushuRiga, SimulationMid-career hireRiga joined the company in 2019 as a mid-career hire. Before joining NSK, he worked for a semiconductor equipment development and sales company, where he worked in mechanical design for new product development. After joining NSK, he participated in a technology division project to improve the profitability of ball screws. He currently works in product development of new large-size, high-load ball screws for applications demanding massive linear force. In this project, his role included preparing test equipment, conducting durability tests on developed products, and confirming reliability. -
Manufacturing Engineering CenterJun, Production Equipment DevelopmentNew graduate hireAfter joining NSK, Jun was assigned to the Manufacturing Engineering Center's Manufacturing Equipment Development Department, where he worked to develop work support functions and advanced technologies using on-machine measurement of ball screws and bearings. He currently works to develop technologies to improve productivity and add new value to products by measuring workpieces using instruments located inside equipment and feeding back the results into the machining process for even higher accuracy. During this project, he developed specialized equipment and programs and verified the consistency between machining data and measurement data.
Extending life, saving energy, and expanding functions in
electric
injection molding machines
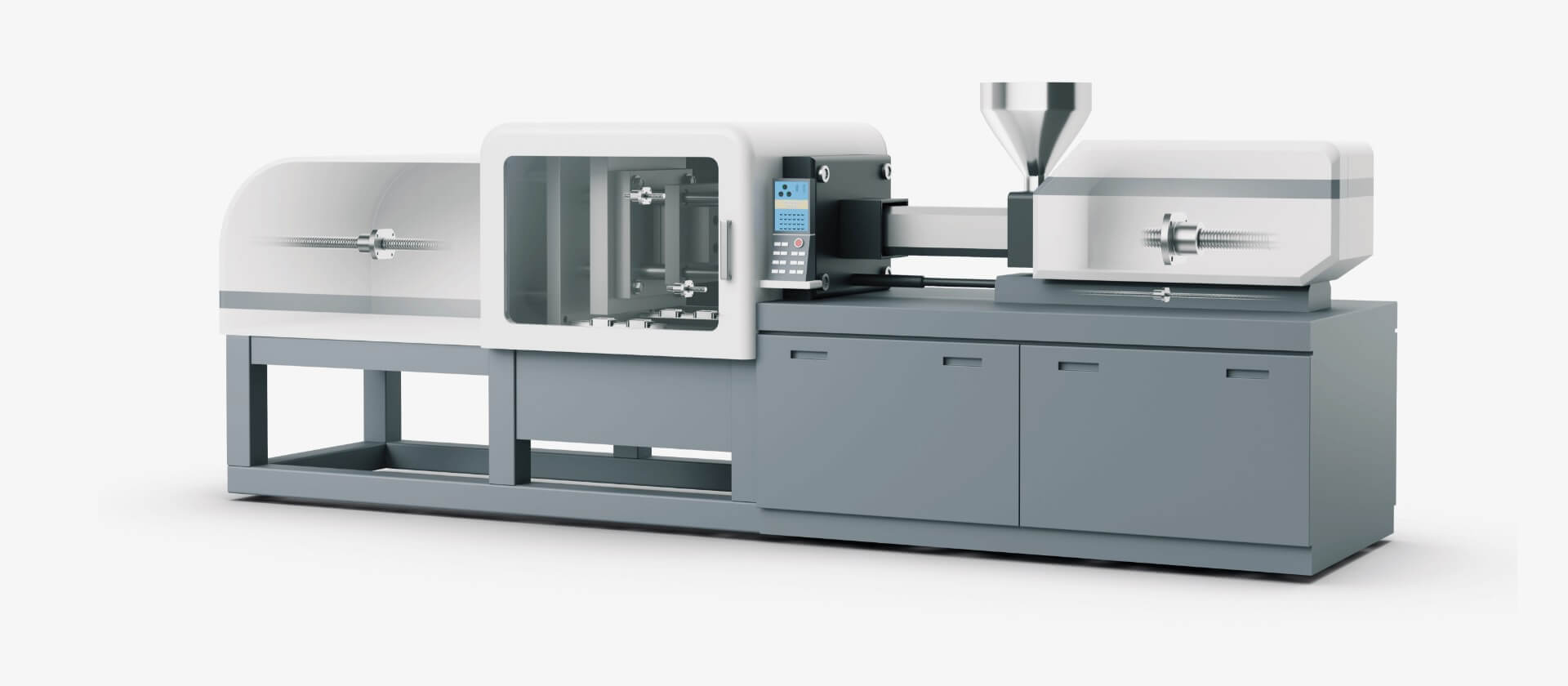
With initiatives to reach SDGs and carbon neutrality gaining traction, components in industrial machinery must reduce environmental impacts while offering improved functionality.
Energy-efficient electric ball screws are replacing hydraulic drive mechanisms in injection molding machines. At the same time, the shift to electric vehicles has increased the need for lightweight plastic parts. Larger and more complex plastic molds require significant improvements in machine capabilities. What’s more, ball screws have to stand up to higher feed speeds while material is extruded in “high-cycle” designs that increase the distance ball screws travel per unit of time, making longer life a top priority.
With the hope of solving these issues for our customers, we embarked on a quest to develop new technology to extend ball screw life.
Development Timeline
-
January to March 2021
Market Analysis/Target Setting
Investigated trends and market needs while assessing offerings from competitors. After studying the benefits we would offer to our customers, we decided to proceed with the development of long-life technology for ball screws.
-
September 2021
Prototype Endurance Test
First prototype completed after 5 months of development. Test equipment prepared to confirm durability matches simulations.
-
January 2022
Results of Endurance Test
Durability targets reached, with real-world performance exceeding simulations.
-
March 2022
Media Announcement
New technology announced to media outlets on schedule.
-
April 2021
Development Begins
Appointed project members and formulated development plans and proposals in DR1. Project launched, targeting a media announcement in March 2022.
-
December 2021
Evaluation of Machining Equipment for Prototype #1
Results showed that the scope of application and production equipment needed to be partially revised to align with simulations, and fixes were made.
-
February 2022
Evaluation of Machining Equipment for Prototype #2
Created a revised prototype based on previous results. Production equipment and measurement technologies reached target levels.
1Design Review (DR): A process in product development where members within and outside the design dept. evaluate proposed specifications, drawings, etc. to determine if development can proceed while meeting requirements for quality and cost on schedule.
-
January to March 2021
Market Analysis/Target Setting
Investigated trends and market needs while assessing offerings from competitors. After studying the benefits we would offer to our customers, we decided to proceed with the development of long-life technology for ball screws.
-
April 2021
Development Begins
Appointed project members and formulated development plans and proposals in DR1. Project launched, targeting a media announcement in March 2022.
1Design Review (DR): A process in product development where members within and outside the design dept. evaluate proposed specifications, drawings, etc. to determine if development can proceed while meeting requirements for quality and cost on schedule.
-
September 2021
Prototype Endurance Test
First prototype completed after 5 months of development. Test equipment prepared to confirm durability matches simulations.
-
December 2021
Evaluation of Machining Equipment for Prototype #1
Results showed that the scope of application and production equipment needed to be partially revised to align with simulations, and fixes were made.
-
January 2022
Results of Endurance Test
Durability targets reached, with real-world performance exceeding simulations.
-
February 2022
Evaluation of Machining Equipment for Prototype #2
Created a revised prototype based on previous results. Production equipment and measurement technologies reached target levels.
-
March 2022
Media Announcement
New technology announced to media outlets on schedule.
Bringing specialists together
to tackle issues
How did NSK come up with this original technology to extend the life of ball screws?
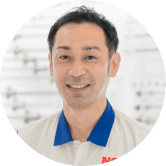
In a ball screw, each ball in the circuit bears load. However, under high loads, this distribution becomes imbalanced and heavier loads act on certain areas of the circuit, shortening the life of the entire ball screw. We saw an opportunity to extend life by tackling the issue of imbalance.
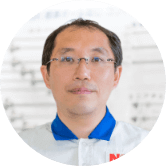
Since all things are made within tolerances, there is always some level of
error. We typically think of the raceway surface of a ball screw as a
perfectly rounded helix, but this ideal is difficult to achieve in practice.
Such variance is what causes certain areas in a circuit to receive higher
loads.
So, we went back to basics in design. We proposed that careful
control of internal specifications would relieve such loads. The long-life
technology we developed is thanks to production equipment that can
consistently deliver on what we envisioned.
What was key to the success of this development?
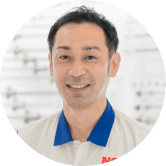
The manufacturing and measuring technologies from Jun’s department were a must. We could come up with the design, but we needed cutting-edge machining technologies to bring our ideas to life.
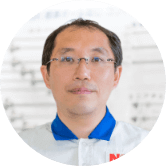
Actually, this project was made possible by work we started seven years ago
to improve efficiency. It wasn’t needed at that time, but we thought it had
the potential to take production to the next level. As this project got
started, someone I worked with from back then suggested that we could use
that technology to create a new product. We realized our efforts from then
could be re-purposed to tackle issues in development.
I never could
have imagined how our work from seven years ago would take shape and evolve
with the contributions of other members on the team. It was a truly
fascinating experience to be a part of!
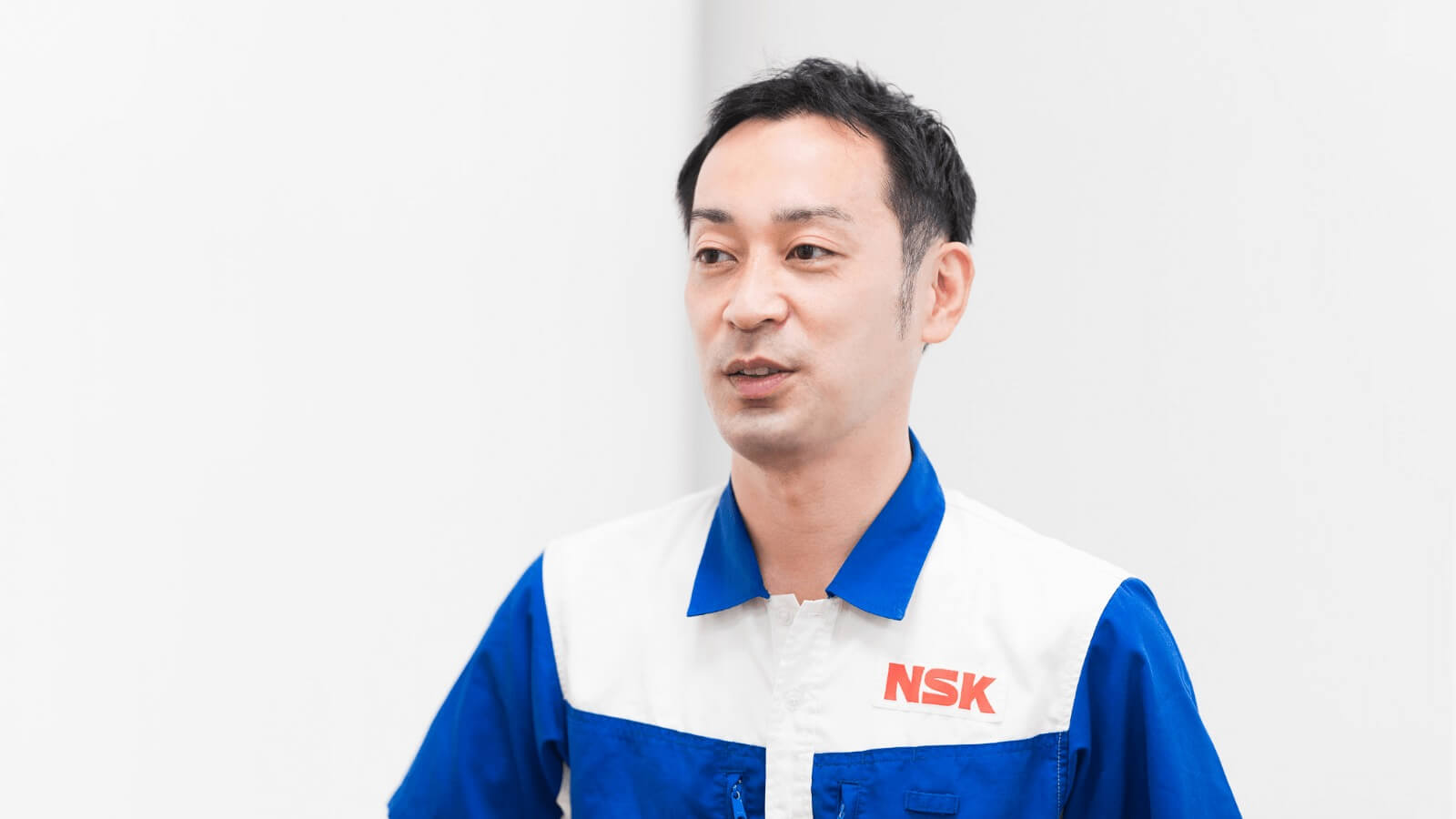
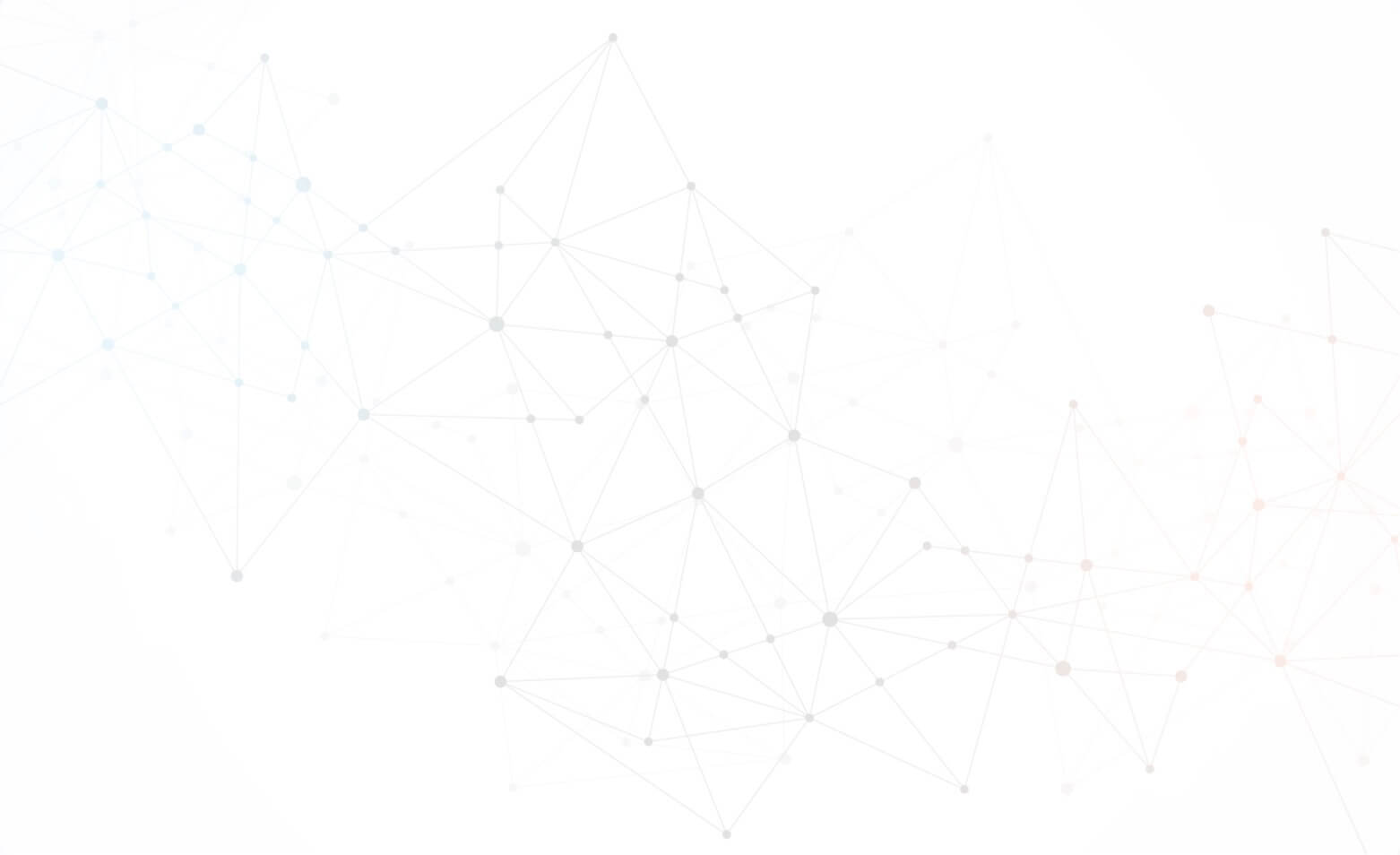
Can you share what technologies were used during development?
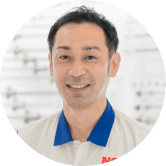
We used “real digital twin”2 technology to its fullest. Early in
the design phase, we ran simulations to test the configuration we thought
would result in longer life.
2NSK’s unique development technology that generates an
accurate virtual copy of the device or product being developed. This
allows engineers to arrive at solutions that break through preconceived
ideas by observing the inside of the proposed product in detail and
understanding its true nature through deduction and modeling.
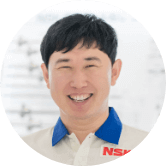
In our evaluations, we tested a real digital twin under load based on customers’ actual usage conditions. Since we were aiming to develop a ball screw with both high load capacity and long life, we needed development analysis that had never been done before.
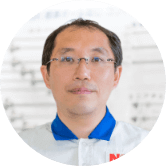
With a real digital twin, we could analyze the inner workings of equipment using the machining technologies we were still considering. Alongside increasing technical knowhow, NSK has been pouring investments into real digital twins with efficiency in mind. It’s thanks to these advancements that our analysis capabilities continue to expand. We were able to make accurate micron-level simulations down to 1/100th the width of a human hair! This also spurred development in measurement technologies.
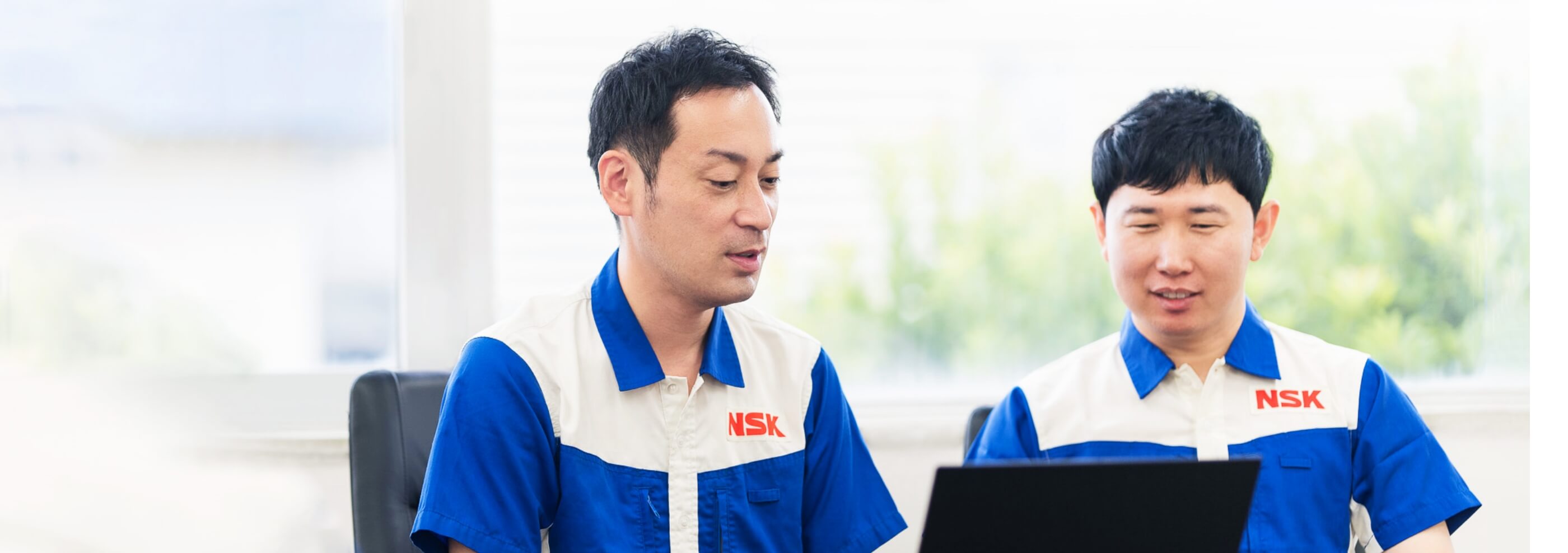
What was the biggest challenge in development?
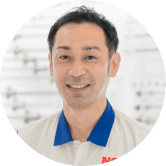
With an extremely short development period, I had to clearly identify all issues right from the start and it was tough to keep up the pace.
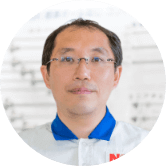
The test equipment was only at our Kyushu Plant, and the pandemic made it difficult to visit often. There was a lot of pressure to gain as many insights as possible from just a few tests. So, we carefully analyzed and reviewed before going ahead with testing at the plant.
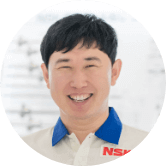
It was particularly hard to set up the right equipment conditions. We wanted to test harsh conditions much more severe than those typically seen by customers and had some difficulty figuring out how to produce high loads and temperatures. But it was worth it; we would not be satisfied with only tests in ideal conditions!
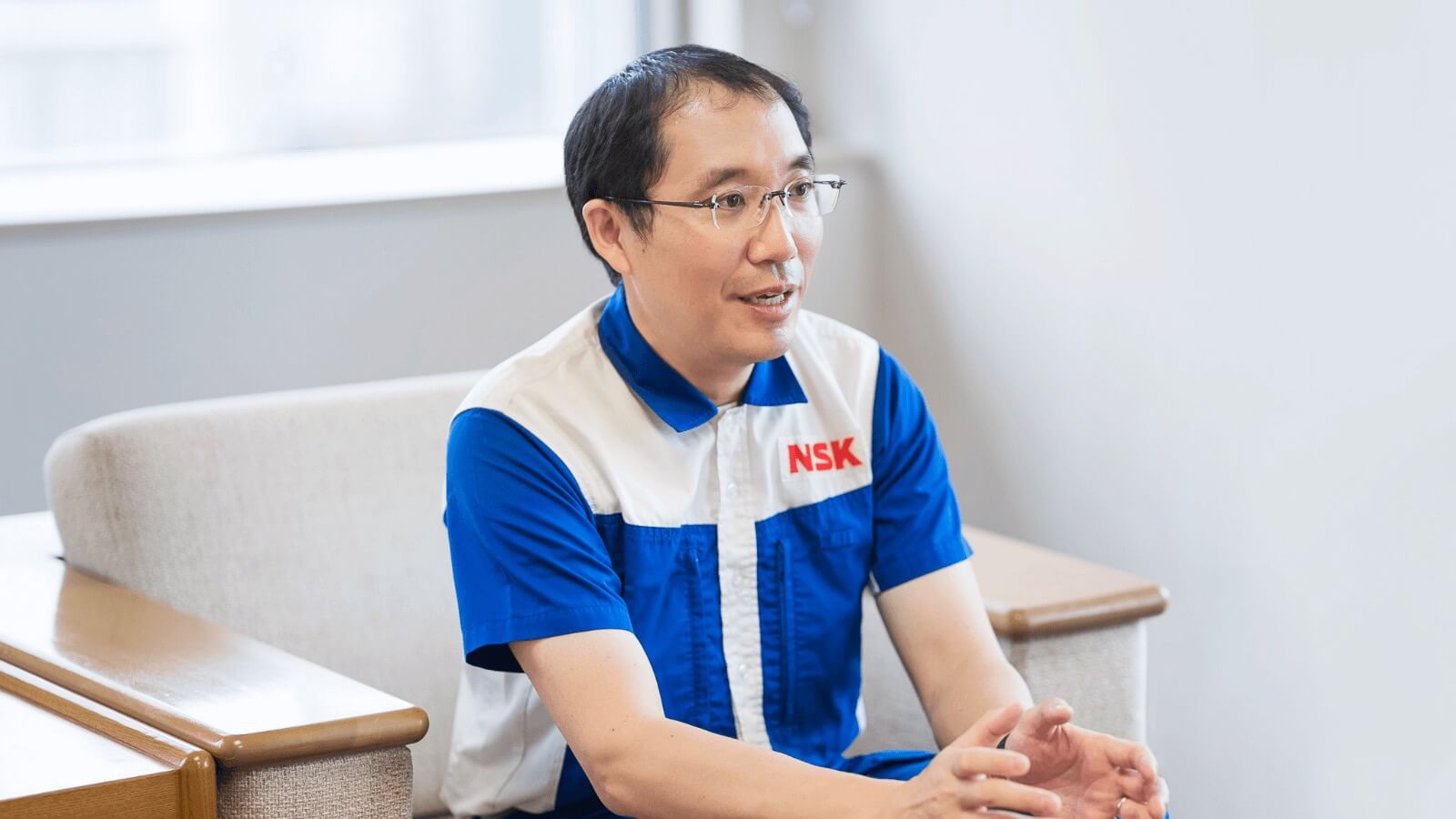

Major developments at NSK often use a cross-departmental approach. What are the advantages of this?
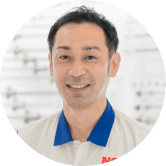
It was my first time to work with such a diverse range of departments, so that was exciting! I’ve always worked in design, so I didn’t know much about production equipment or measuring devices. It was great to tap into Jun’s insights and to work with actual machines–I gained a ton of knowledge. It was also exciting to talk with other members and see a range of ideas come in from different directions.
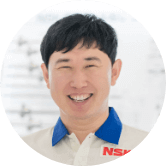
At NSK, cross-functional teams are formed right at the start of a project. By gathering people from design, development, production, facilities, marketing, and so on to share their perspectives, we can be sure that a product matches the market. It also helps bring us together closer as an organization and helps the company make full use of the resources and talent we have. This proven system was indispensable in our development process as well.
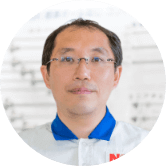
Although I often work with plants to improve products and have ideas on how to solve problems, it’s tough to take this to next level and produce something new. I had a great experience working together with design and development to bring this technology to life. I think it’s a great system because it allows specialists to share their ideas and pursue their own goals.
What motivates you to keep tackling one challenge after another?
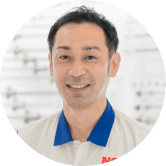
People at NSK are always keen to take on new challenges! Our company culture encourages us to go beyond and we have plenty of opportunities to go ahead and put our ideas into action.
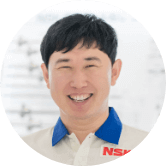
We are targeting manufacturers outside Japan in particular with this product. I'm originally from overseas, so the challenge of taking NSK’s products to the world is a big source of motivation for me.
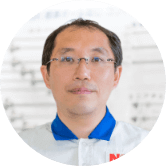
Although many of NSK’s products operate out of sight, they are hard at work in all kinds of places, meaning the world is filled with equipment connected to my work. The world would stand still without the essential products we make, and by reducing friction and energy loss, they also help improve the environment. I stay motivated by thinking how our efforts keep the world moving and are shaping a better future.