精機製品・技術レポート:NSKリニアガイド用「NSK K1™」の開発
リニアガイド用「NSK K1」は潤滑を目的として開発した独自の複合材料「固形油」を、コンパクトな潤滑油供給ユニットとして応用して開発したものである。このように油やグリースを樹脂に含浸させて潤滑に応用する考え方は従来からあったが、直動転がり案内製品に応用した例は今までなかった。
リニアガイドに代表される直動転がり案内製品に用いられる潤滑方法は大きく次の二つに大別できる。その一つはグリース潤滑であり、もう一つはオイル間欠給油潤滑である。両者は使用上、一長一短の特徴を持つことが知られている。
グリース潤滑は経年変化による劣化や流出を生じることから、定期的な補給が必要である。一方、オイル間欠給油潤滑では確実に新しいオイルが供給される半面、オイルタンクヘの給油が必要であり、さらに複雑な配管設備が必要となる。いずれにしても完全なメンテナンスフリーとは呼べないのが現実であった。
従来から市場ではメンテナンスフリーと言うことが叫ばれていたにもかかわらず、リニアガイドを含め直動案内製品にはメンテナンスフリーを可能にするような製品を見ることはできなかった。
そこで市場のニーズを実現するべく、リニアガイド用「NSK K1」の実用化へ向けて開発を進めてきた。当初は搬送系を中心に、軽負荷の用途におけるメンテナンスフリー化や、潤滑油の消失しやすい産業機械・木工機械等の長寿命化を狙って開発を行い、これを実用化して市場に提供してきた。
市場では搬送系にとどまらず工作機械等においても、メンテナンスフリーやクーラントヘの潤滑油混入による腐敗・異臭等の環境問題、省エネルギー等といった、時代のトレンドと合致したことからの反響が大変大きかった。そのため、NSKではその後、工作機械用途を考えた高負荷条件での評価試験を進めた。その結果、このたび実用化の段階にまで到達し、直動案内製品として世界で初めて製品化することができた。
工作機械用途である以上実用化する上では、潤滑油供給能力とともに、切削粉やクーラント等、異物雰囲気中における耐久性能も重要なポイントとなる。
ここでは、それらも踏まえて開発を行ってきたリニアガイド用「NSK K1」の基本特性と、「NSK K1」付きリニアガイドの耐久性能を中心に以下に紹介する。
2. 「固形油」について
2.1. 「固形油」の構造
「固形油」は、潤滑油とそれに親和性のある数種類の分子量の異なるポリオレフィン樹脂とから構成されるユニークな新素材である。この素材は、加熱してポリオレフィン樹脂の融点を超すと流動するので、潤滑油を含有した樹脂素材として任意の形に容易に成形することが可能である。
「固形油」の代表的な機械的性質を表1に示す。併せてプラスチックではナイロン66(PA66)、ゴムとしてニトリルゴム(NBR)についても示す。
表1の硬さについては、ナイロン66とそれ以外では一般的に評価方法(スケール)が異なり(プラスチックはロックウェルRスケール、ゴムはショアーAスケール)、直接比較はできない。そのために曲げ弾性率を併記した。
「固形油」の機械的性質は、潤滑油を含有しているため、引張り強さは他に比べて小さいものの、硬さすなわち曲げ弾性率はプラスチックとゴムの中間に位置するということができる。「固形油」からの潤滑油供給は、成形時にポリオレフィン樹脂の分子が伸びた状態となっているため、絶えず収縮させようとする残留応力が作用することによって生じる。
また、図1に示すように「固形油」はポリオレフィン樹脂の配合や種類を変えることで潤滑油供給量をコントロールすることができる。
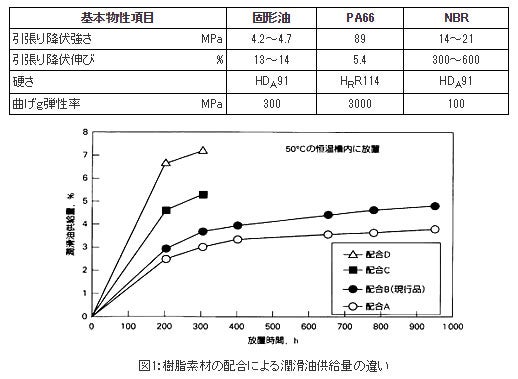
3. リニアガイド用「NSK K1」とその基本性能
3.1. 形状と取付け方法
リニアガイド用「NSK K1」の形状例と取付け例を写真1及び図2に示す。
NSK K1は図2に示すように、リニアガイドのエンドキャップの外側に位置するサイドシールと保護板の間に装着し、NSK K1に設けられた切り欠き部分よりも径の大きい締付けリングを挿入することでNSK K1を変形させ、レールの軌道面により密着させている。そして含有した潤滑油を徐々に軌道面や、軌道面を介して鋼球に供給している。
また、NSK K1の厚さに比べて、締付けリングの厚さが僅かに厚くなっていることから、NSK K1を拘束しない構成となり、NSK K1が経時的に徐々に変形した場合でも、常に転走面に密着し潤滑油を供給する構成となっている。
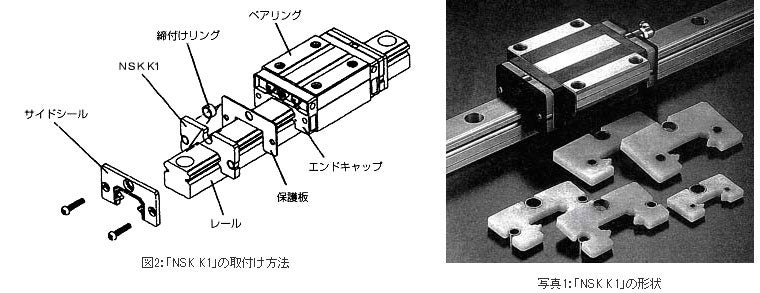
3.2. 潤滑油供給特性
潤滑油と樹脂の組合せによって特性の異なった「固形油」を得ることができる。ここで紹介するリニアガイド用NSK K1は潤滑油を70重量%含油させたものである。
「固形油」の潤滑油供給量は温度とともに増加することが知られている。これは温度上昇に伴ってポリオレフィン樹脂が活性化し、潤滑油を絞り出すための応力が増加することによって、潤滑油供給能力が増すことによる。
これをリニアガイド用NSK K1に成形したもので評価した結果を図3に示す。明らかに潤滑油供給量が雰囲気温度に依存する結果が得られている。
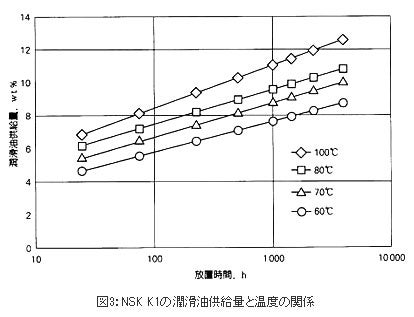
そこで、NSK K1を長期間にわたって高い機能を維持させるために、使用温度の上限を50°C(瞬時では80°C)に規定していた。しかし最近の実験では70~80°C程度の雰囲気中で連続走行させても特に問題の無い結果が得られている。
次に、NSK K1をリニアガイドに取り付け、NSK K1からの潤滑油のみで走行させた際に、単に連続走行させたものと、定期的に染み出た潤滑油をふき取ったものとで比較したところ、後者の方が潤滑油供給量が多いという結果を得た(図4参照)。

これはNSK K1の雰囲気によって、乾燥状態よりも油が存在している方が潤滑油が染み出しにくいという結果である。言い換えれば、リニアガイドにグリース等の潤滑剤が十分存在する間はNSK K1の潤滑油は保持される傾向があるということであり、NSK K1が本来機能しなければならない状態で有効に機能するものと考えられる。
次にNSK K1の耐薬品性についてであるが、特殊環境として無機酸やアルカリ雰囲気中におけるNSK K1ヘの影響を確認するため、塩酸、硝酸(pH1程度)及び苛性ソーダ(pH13程度)の濃度1モル/リットル中に10日間浸漬放置した際の状況を表2に示す。外観また、NSK K1の潤滑剤供給量(重量変化率)とも、このような酸やアルカリ環境において空気中と何ら変わることがない結果が得られている。
また、一般的なクーラント、潤滑油、グリース等に関しては、それらの色が転写されるほかはほとんど問題無い。しかし、シンナ等の有機溶剤、白灯油、防錆油(白灯油成分を含むもの)中に長時間放置されると、NSK K1に含まれている潤滑油が置換され、著しく機能を失うこともあり得る。

3.3. 潤滑油供給寿命予測
雰囲気温度40℃におけるリニアガイド走行試験をもとにして、NSK K1の潤滑油供給寿命を予測した、経過時間に対する潤滑油供給量を図5に示す。
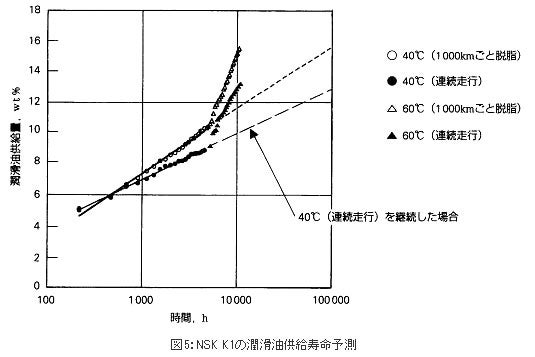
なお、試験を加速させるため途中からは雰囲気温度を40℃から60℃に変更している。
当然ながら雰囲気温度が高くなることで潤滑油供給量の傾きが大きくなっているものの、10数%を越えてもなお走行が可能であり、さらに走行を継続させている。
一般的な機械周りの雰囲気温度を40℃付近と仮定して、本試験において40℃で継続走行させた場合の潤滑油供給寿命を推定する。
最小二乗法により近似線を求め、寿命に達する潤滑油供給量を現状の実績から連続走行で13%、1000kmごとの脱脂品で15%と少なめに見積っても、寿命としておおよそ10万時間が得られる。これは機械の可動時間を年間250日フル稼働としても16年間以上は潤滑油が供給されることを意味し、十分な寿命時間と判断できる。
4. 「NSK K1」付きリニアガイドの耐久性
4.1. 軽負荷条件の耐久性
NSK K1本来の使われ方はグリースとの併用であるが、初期に封入したグリースがその後枯渇した状態を想定し、NSK K1のみの潤滑油でどの程度まで耐久性があるかを、リニアガイドLH30を用い、搬送装置をねらった200m/min送りを超える高速で軽負荷の条件について行った試験の結果を図6に示す。
その結果、NSK K1からの潤滑油のみでも十分に走行が可能な結果が得られた。さらに、有機溶剤等を用いて途中で走行部の脱脂を行っても、それ以降にNSK K1から供給される潤滑油のみで10000km以上の走行が可能という結果が得られている。また、高速走行ということでNSK K1の摩耗を懸念したが、自己潤滑が十分なされ、まったく問題ないということが明らかとなった。
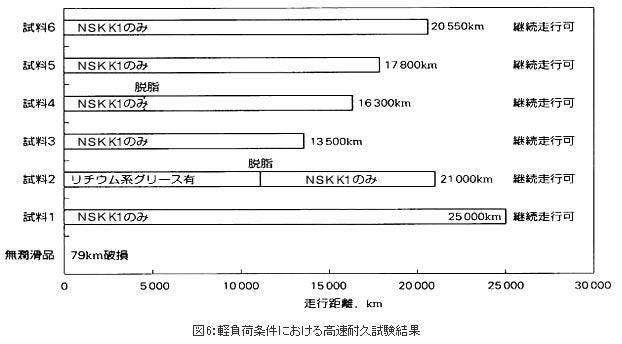
つづいて、同型番のリニアガイドLH30について60m/min送りにおける中速で軽負荷の条件での耐久試験結果を図7に示す。リニアガイドのレールの転走溝を走行途中で脱脂しても、継続的に潤滑油がNSK K1から供給されるため、問題なく走行していることが認められる。
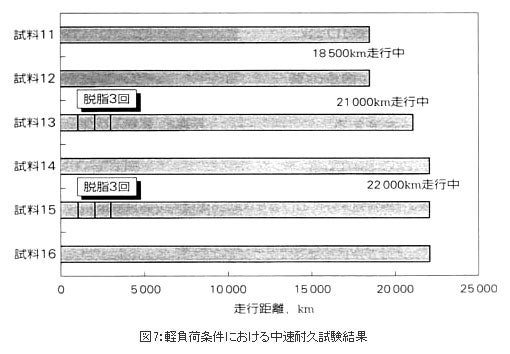
4.2. 高負荷条件の耐久性
リニアガイドの用途として、高負荷条件の代表例が工作機械用の案内である。ここで紹介する耐久試験は、グリース潤滑にNSK K1を付加させることで、工作機械などにおける長期メンテナンスフリー化を目指すものである。
試験は高負荷条件下、すなわちリニアガイドの実用最大荷重の目安として溝の最大接触面圧を約2000MPaに設定し、下記のそれぞれのねらいについて各種試験を行った。
(1) グリース性能が劣化した状態を想定した耐久性評価(NSK K1のみの潤滑油での耐久試験)
(2) 使用して数年後を想定したNSK K1による耐久性評価(NSK K1を一定時間高温に放置して、含有している潤滑油をある割合放出させ、数年後の状態を意図的に作り出す)
(3) 実用条件と同じ条件での耐久性評価(グリース潤滑にNSK K1を付加する)
(4) ねらい(3)の異物雰囲気中での耐久性評価
リニアガイドに装着するNSK K1の枚数については、高負荷条件ではベアリングの片側に2枚付けることを基本とし、片側4枚の場合を含めて試験を行う。また、耐久試験における走行距離の目標は、最近の高速化の動向から判断して、第1ステップとして3000km、第2ステップとして5000kmを考える。
これら各種試験の中から代表として、ねらい(1)の例を下記し、ねらい(4)の例を4.3.1に示す。
試料はリニアガイドLY35を用い、2ベアリング仕様のレール2本でテーブル体として、下記条件で走行させた。
潤滑 NSK K1のみ
シール仕様 NSK K1片側2枚 + 標準サイドシール
予圧荷重 1760N (中予圧)
外部荷重 6080N/ベアリング
最大接触面圧 2060MPa
ストローク 400mm
平均送り速度 24m/min (クランク駆動により 0~37.7m/min で変化)
高負荷条件における5000km走行時の調査結果
走行距離5000km時点での調査結果を表3に示す。参考のため、型番は異なるものの類似した条件でのオイル間欠給油潤滑での試験結果を併記する。剛性の変化などから判断して、オイル間欠給油にそん色のない結果が得られており、さらに走行を継続している。
また、これ以外の、上記したねらいにおける各種試験についても、いずれも目標とした5000kmの走行を超えて順調に走行中であり、工作機械などの高荷重条件についても実用化の目途は十分に得られたと判断している。
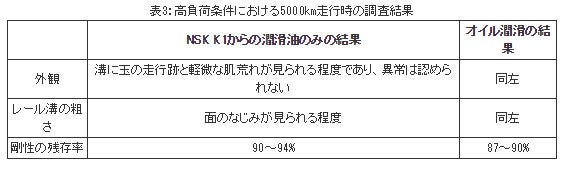
4.3. 異物環境下の耐久性
4.3.1. 異物入りクーラント液雰囲気中
最初に、工作機械を想定した異物環境として、異物入りクーラント液を用いた苛酷条件での試験結果を紹介する。その試験条件を下記する。
試料:リニアガイドLY45BN(重予圧)
計4レール8ベアリング
各レールのシール仕様
(a):NSK K1片側4枚 + 標準サイドシール
(b):NSK K1片側2枚 + 標準サイドシール
(c):標準ダブルシール(NSK K1なし)
(d):標準ダブルシール(オイル間欠給油)
なお、オイル間欠給油での試験は、以前に同一条件で実施したものである。NSK K1片側4枚(1ベアリングあたり8枚)の配分は、試験機の都合により外側6枚、内側2枚に設定した。
潤滑条件 オイル間欠給油を除き、アルバニアNo.2グリース(初期に封入のみ)
予圧荷重 4120N
外部荷重 9800N/ベアリング
ストローク 400mm
平均送り速度 24m/min (クランク駆動により0~37.7m/minで変化)
異物条件 切削液ミクロカット3850LHの30倍希釈液にFCD45鋳物粉115メッシュ5%を混入、レール上溝まで注入し2日間走行、異物液を抜いて5日間走行のパターンを繰り返す。(写真2参照)
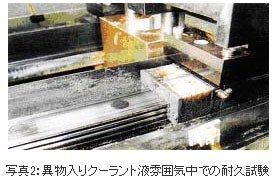
試験はレール(a)(NSK K1片側4枚)とレール(b)(NSK K1片側2枚)とでスタートした。3000km走行時点でレール(b)の側に作動不良によると思われるエンドキャップの破損が生じた。
そこで、レール(b)に代えてレール(c)(NSK K1なし)を取り付け、レール(a)はそのまま継続走行させた。レール(c)は600km走行時点で作動不良によると思われるエンドキャップの破損が発生した。
レール(a)は合計3600kmを走行しても、なお継続走行可能な状況であった。この時点で試験を打切り、分解調査を実施した。その結果を、オイル間欠給油の3000km走行での結果と合わせて、表4に示す。
前述のように、NSK K1なしは600km、NSK K1片側2枚は3000kmでエンドキャップの破損を生じたが、NSK K1片側4枚については試験完了後もなお予圧が残存しており、継続走行可能な状況であった。
試験中、試験機台上で精密ばねばかりを用いて測定した摩擦力の、走行距離に伴う変化を図8に示す。
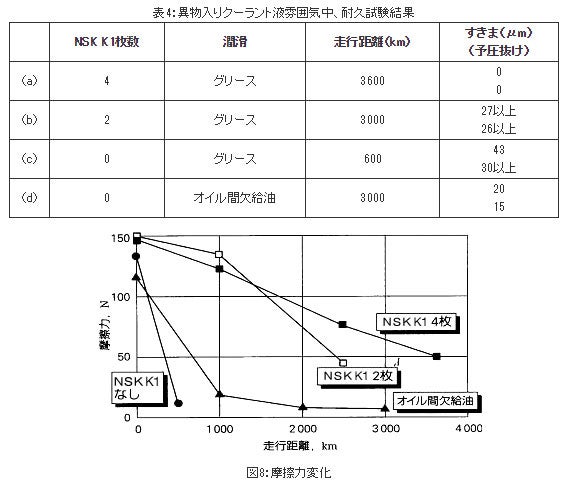
NSK K1を用いないものは初期の摩擦力の低下が大きく、早期に摩耗が進行していたことがうかがわれる。一方、NSK K1付きでは摩擦力の低下が遅れて生じている状況である。NSK K1片側4枚では、3600km走行後も予圧が残存していたことが摩擦力のデータからも裏付けられる結果となっている。
以上の結果から、過酷な異物雰囲気中でのNSK K1の装着枚数は、高負荷条件での基本としたベアリング片側2枚に、さらに1~2枚加えることで大幅な寿命延長が期待できる。
4.3.2. 木材切り屑雰囲気中
過酷な雰囲気条件で、異物によって潤滑油が吸収され潤滑不良を起こす可能性がある例として、木材切り屑などの粉塵が挙げられる。通常木工機械などはこのような環境で使われることが多く、一般的には次のような問題があった。
木材切屑がベアリング内のグリースを枯渇させるばかりでなく、切り屑のベアリング内侵入防止を目的に付けられた標準シールの潤滑をも枯渇させ、ひいてはシールの摩耗につながり、シール機能を失うことで切り屑の侵入が促進され、転動体の循環不良を生じていた。
NSK K1はベアリング内の潤滑不良を助けるだけでなく、標準シールの摩耗を防止する作用をも有している。
切り屑雰囲気中において、標準ダブルシール(標準シールを2枚重ねたもの)と、NSK K1付きのものとで、下記条件により耐久試験を行った結果を図9に示す。
試料 LH30
予圧 微予圧
平均送り速度 24m/min
ストローク 400mm
外部荷重 490N/ベアリング
潤滑・シール仕様 AV2グリース + 標準ダブルシール
AV2グリース + NSK K1 + 標準シングルシール
木材切り屑の量による走行距離の違いがあるが、同量の切り屑で比較すると、NSK K1を用いることで約2~4倍の走行距離を得ることができた。
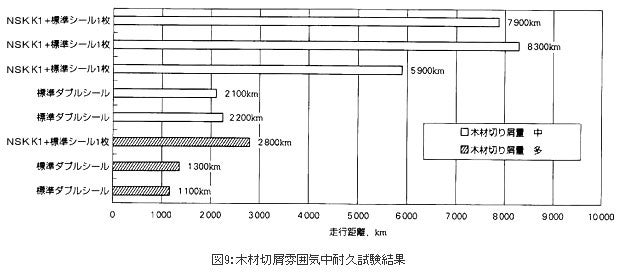
4.3.3. 鋳物切屑雰囲気中
つづいて、異物が鋳物切屑の場合の過酷環境の試験結果を紹介する。
試料 LH30
予圧 すきま互換品
潤滑油 AV2グリース(初期封入のみ)
異物量 1レール当り300g
送り速度 45m/min
ストローク 400mm
鋳物切屑は最初にベアリング両端に振り掛け、カバーを取り付け、その後は1日1回程度ストローク両端に寄せられた切屑をカバー内に戻し、ストロークごとにカバーで切屑が掻き寄せられレールに掛けられるようにした。走行完了時(2000km走行時)のリニアガイドの外観を写真3に示す。
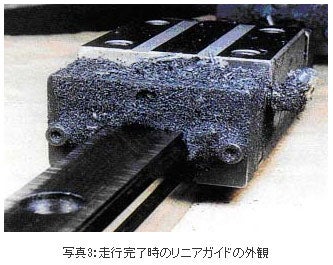
表5に示す試験結果のように、NSK K1を付加した効果が明らかに認められている。特にNSK K1は、標準シールの摩耗、むしれ等に対してかなり効果があり、摩擦力(シール抵抗)の変化が小さいことからもそれが認められている。
また、ベアリング内に侵入した異物量の状況からも、NSK K1は潤滑油補給効果とともにサイドシールとしての効果が期待できる結果が得られている。
試験は2000kmで中止したが、継続して使用した場合、標準シールの摩耗の差によって更に劣化の差が現れ、寿命に大きく影響するものと考えられる。
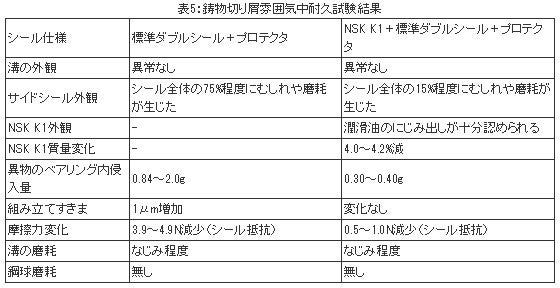
ここで、試験後のNSK K1の潤滑油供給能力について確認するため、試験に用いたNSK K1を室温に24時間放置した後の表面の拡大写真を写真4に示す。表面には鋳物切り屑が付着しているものの潤滑油のにじみ出しが確認でき、十分に機能が維持されていると考えられる。
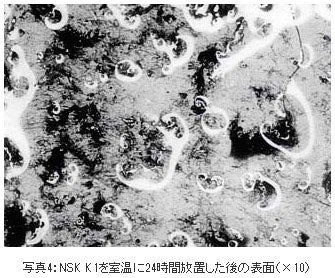
5. 溶接ライン用リニアガイドにおける「NSK K1」の効果
以上はベンチテスト結果からの代表例であるが、ここではフィールドで使用されたNSK K1の一例を紹介する。
自動車製造ラインの溶接機で稼働した、表6に示す仕様のNSK K1付きとNSK K1なしのリニアガイドについての調査結果を下記する。
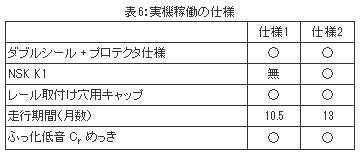
同一機械の同一箇所において先ず仕様1(NSK K1無)で10.5か月間稼働後、仕様2(NSK K1付き)に交換し13か月間稼働した。両者の稼働後の状況には著しい違いが見られ、NSK K1の極めて大きな効果が認められている。(写真5~8参照)
仕様2は仕様1と比較してレール、ベアリングともにボール溝の劣化が明らかに小さく、ボールも同様に仕様2の方が劣化が大幅に小さい。仕様1はレール、ベアリングのボール溝及びボールに錆の発生が認められたが、仕様2には認められなかった。また、ベアリング内へのスパッタ粉の侵入も仕様2の方が若干少ないことが認められた。
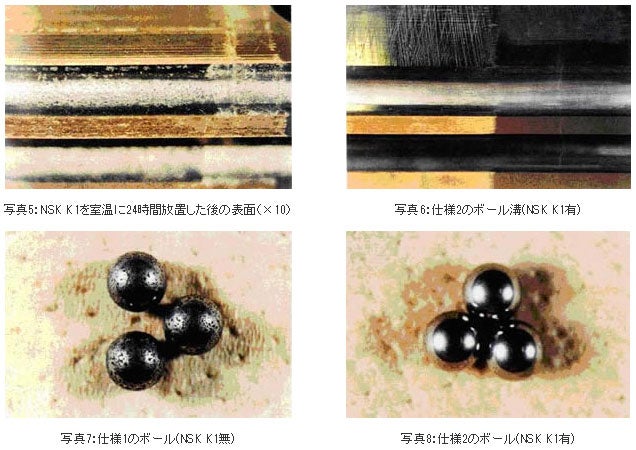
6. 「NSK K1」の最近の動向
6.1. 食品機械用「NSK K1」
機械の衛生管理のため定期的に水等によって洗浄され、潤滑剤としてのグリースが洗い流されやすいものに、食品機械がある。
今まで述べてきた標準のリニアガイド用「NSK K1」でも食品に直接触れる可能性が無い場合には十分使用可能であるが、さらに食品の近くで使用され食品に触れる可能性があるような場合には、組成を吟味する必要がある。
そこでFDA(United States Food and Drug Administration)の認可を得た材料で構成することでより安全な食品機械用NSK K1を開発した。
現在、一般走行耐久試験及び定期的に水没させての試験を行い、食品機械用NSK K1の潤滑性能について評価している最中である(写真9参照)。一般走行試験では現在13000kmを走行中であり、また、水没試験(1日間/週 水没させる)については2000kmを異常なく走行し、標準のNSK K1とほぼ同程度の機能が確認されている。
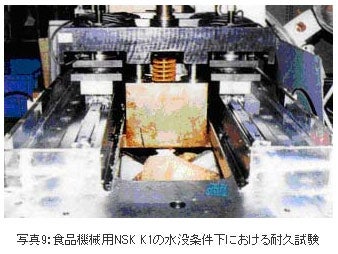
6.2. ボールねじ用「NSK K1」
機械の送り系全体を考えると、リニアガイドとともにボールねじについてもメンテナンスフリー化を図ることが必要である。
NSKでは、リニアガイドと同様の考え方でボールねじ用NSK K1の開発をすすめており、本誌「ボールねじの最近の技術動向」に見られるように、工作機械などの高荷重用途を含めて、実用化の目処を得る状況に至っている。
7. あとがき
各種試験結果から、リニアガイド・ボールねじに「NSK K1」を付けることで、オイル潤滑と同等以上の潤滑性能が得られ、長期メンテナンスフリー化が可能であると考えられる。
特に異物などの悪環境下では、「NSK K1」の潤滑油供給部材としての大きな効果が期待できる。
今後は、リニアガイド、ボールねじともに、さらにデータを蓄積することによって、メンテナンスフリーの信頼性向上を図っていきたい。
参考文献
1) 矢部俊一,植木史雄,高城敏己,松永茂樹,塚田徹,加藤総一郎:NSK Technical Journal, 661 (1996), 36-41